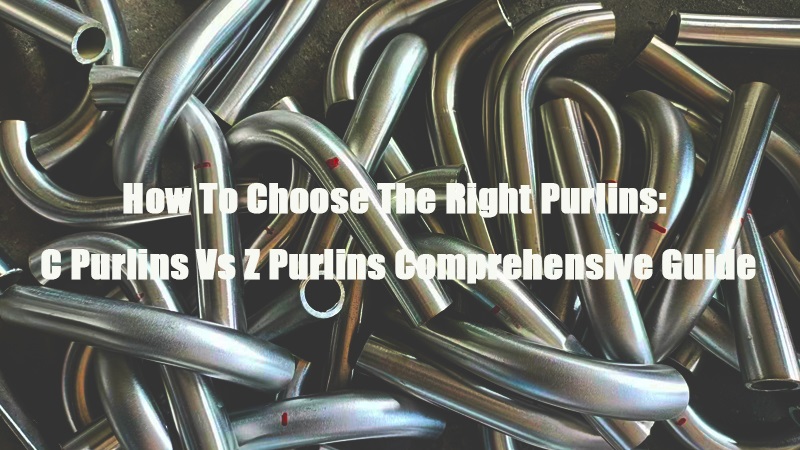
Giới thiệu:
Ống uốn là thành phần quan trọng trong nhiều ngành công nghiệp, bao gồm xây dựng, ô tô, hàng không vũ trụ và kỹ thuật hóa học, do số lượng lớn và nhiều loại. Các bộ phận này đáp ứng nhu cầu ngày càng tăng về trọng lượng sản phẩm và độ bền cao từ cả góc độ vật liệu và kết cấu.
Tuy nhiên, trong quá trình uốn, các vấn đề về ứng suất và biến dạng có thể phát sinh, ảnh hưởng đến hiệu suất của ống và có khả năng dẫn đến các vấn đề về cấu trúc và các vấn đề khác.
Bài viết này nhằm mục đích giải đáp các câu hỏi và câu trả lời liên quan đến ứng suất và biến dạng trong ống uốn bằng thép không gỉ.
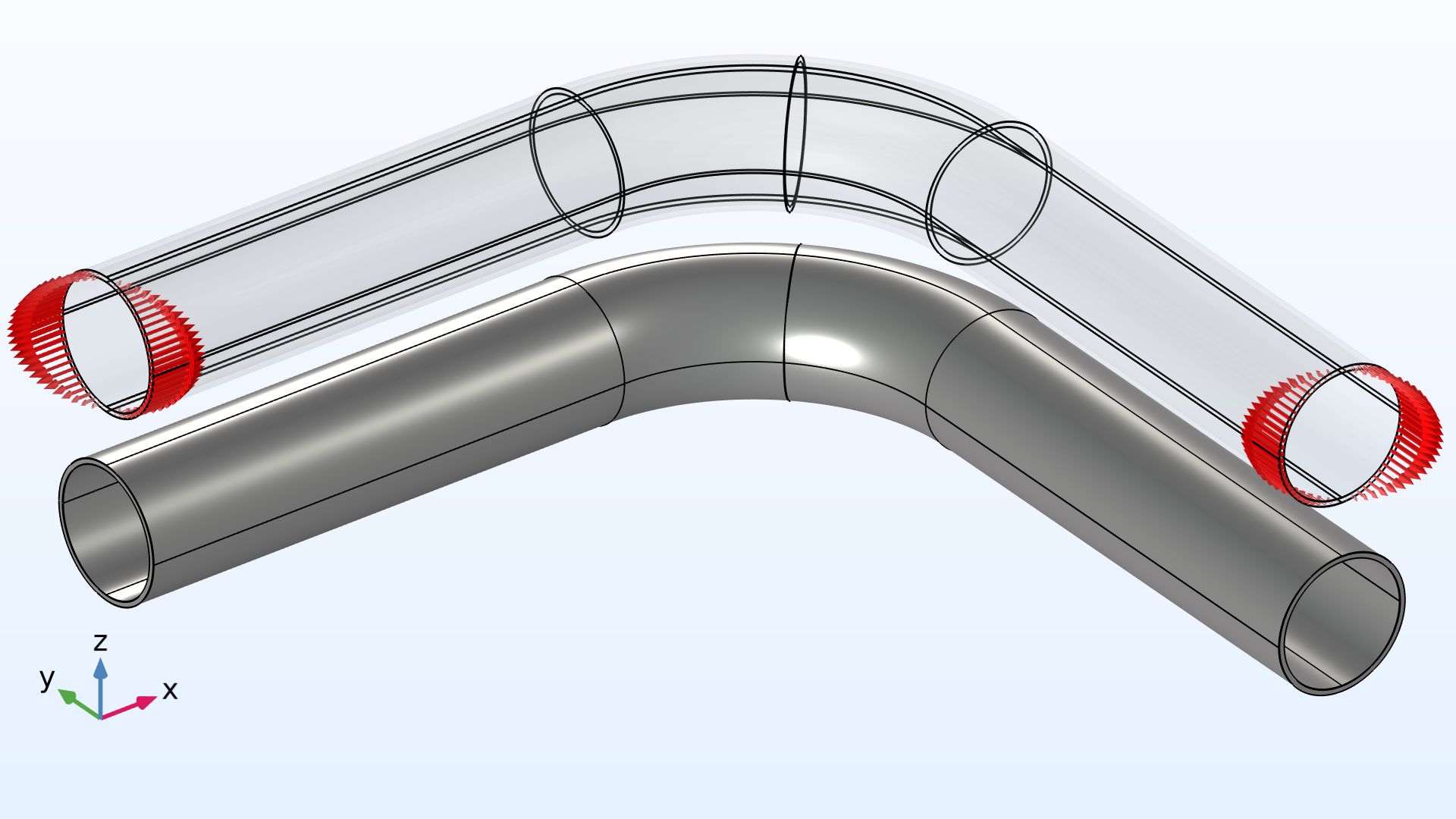
1.0 Nguyên nhân gây ra ứng suất và biến dạng trong ống uốn
1.1 Căng thẳng phát sinh trong quá trình xử lý
Tốc độ làm mát: Trong quá trình uốn, tốc độ làm nguội không đều có thể gây ra sự khác biệt về nhiệt độ bên trong vật liệu ống, dẫn đến các tính chất cơ học khác nhau ở các vùng khác nhau và gây ra ứng suất nhiệt. Khi có sự khác biệt đáng kể về tốc độ làm nguội giữa các vùng, quá trình kéo giãn hoặc ứng suất nén có thể hình thành ở những vùng có nhiệt độ cao hơn và thấp hơn. Sự phân bố ứng suất không đều này có thể dẫn đến biến dạng cục bộ hoặc tích tụ ứng suất dư, ảnh hưởng đến chất lượng của ống.
Quá trình uốn: Trong quá trình uốn ống thép không gỉ, ứng suất kéo xảy ra ở mặt ngoài trong khi ứng suất nén xảy ra ở mặt trong. Sự phân bố ứng suất không đều ở các bộ phận khác nhau có thể gây ra biến dạng như hình bầu dục hoặc nhăn trong quá trình uốn.
Xử lý không đúng cách: Sử dụng khuôn hoặc máy uốn không phù hợp, cài đặt CNC không đúng cách, tốc độ xử lý quá mức hoặc bôi trơn kém có thể dẫn đến hiện tượng tập trung ứng suất cục bộ và biến dạng không thể phục hồi trong ống.
1.2 Tác động của tính chất vật liệu
Căng thẳng bên trong: Đặc biệt đối với vật liệu kim loại cán nguội, ứng suất bên trong vật liệu có thể được giải phóng trong quá trình uốn cong, gây ra hiện tượng uốn cong hoặc cong vênh, ảnh hưởng đến độ chính xác về hình dạng của ống.
Độ cứng cao và Làm cứng bằng phương pháp lạnh: Độ cứng cao của thép không gỉ có thể dẫn đến quá trình tôi nguội trong quá trình uốn, khiến độ cứng của bề mặt vật liệu tăng lên dưới ứng suất kéo, khiến vật liệu giòn hơn.
Độ đàn hồi và độ dẻo: Thép không gỉ có xu hướng nảy lại đáng kể khi uốn cong, dẫn đến độ lệch giữa hình dạng cuối cùng của ống và các yêu cầu thiết kế.
1.3 Cài đặt thiết bị không đúng cách
Lựa chọn khuôn uốn không phù hợp: Việc chọn khuôn có kích thước, bán kính cong hoặc vật liệu không phù hợp cho máy uốn có thể ảnh hưởng đến sự phân bổ ứng suất và biến dạng của ống.
Kiểm soát tốc độ uốn không đúng: Lỗi trong việc lập trình máy uốn hoặc không cài đặt tốc độ uốn theo các vật liệu khác nhau có thể dẫn đến ứng suất không đều lên vật liệu, đặc biệt là trong giai đoạn uốn ban đầu và cuối cùng, dẫn đến biến dạng quá mức cục bộ hoặc biến dạng hình dạng.
2.0 Phương pháp phát hiện ứng suất và biến dạng trong ống uốn
2.1 Công cụ kiểm tra và đo lường trực quan
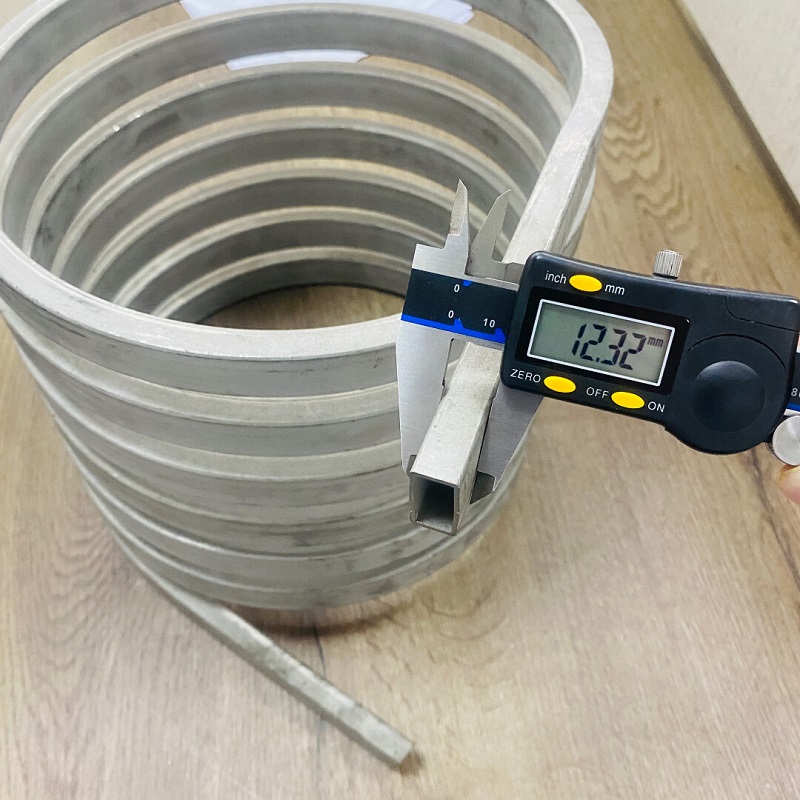
Kiểm tra trực quan: Kiểm tra các vết nứt, vết xước, vết lõm hoặc các khuyết tật khác trên bề mặt ống bằng mắt thường hoặc kính lúp.
Thước cặp và micrômet: Đo đường kính ngoài, đường kính trong và độ dày thành ống để kiểm tra độ chính xác về kích thước và đánh giá độ tròn, đường kính và bán kính uốn của ống để đảm bảo chúng đáp ứng các yêu cầu thiết kế.
2.2 Mẫu tham khảo thử nghiệm
So sánh ống với các mẫu chuẩn để xác định xem nó có đáp ứng các yêu cầu thiết kế hay không.
2.3 Tiêu chuẩn kiểm tra dung sai
Kiểm tra bán kính uốn, góc, kích thước và hình dạng của ống theo tiêu chuẩn dung sai.
2.4 Kiểm tra không phá hủy cho độ chính xác cao
3.0 Giải pháp: Các phương pháp hiệu quả để giải quyết các vấn đề về ứng suất và biến dạng
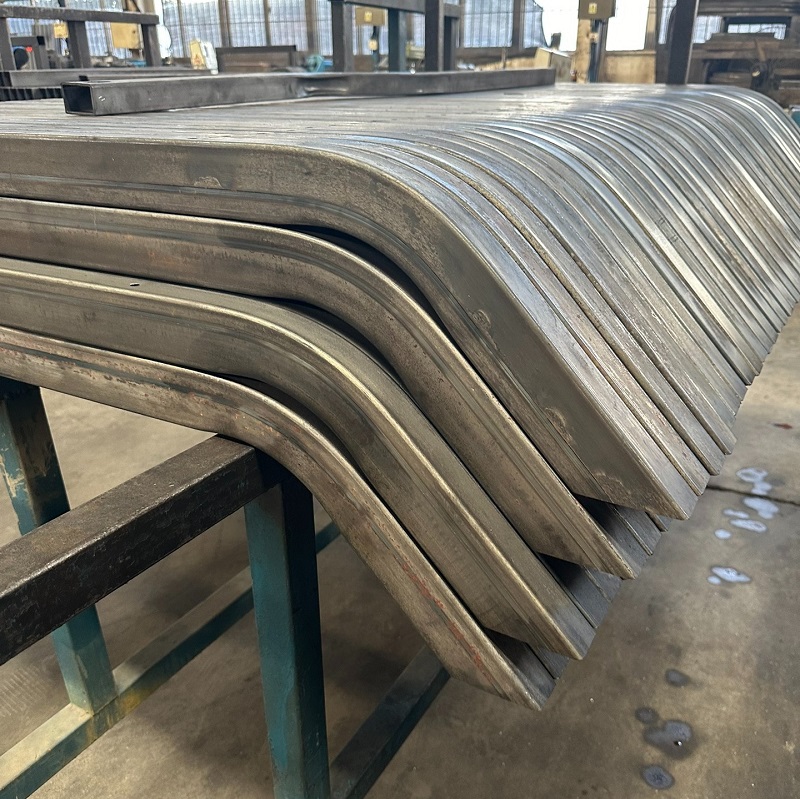
3.1 Tối ưu hóa bán kính uốn cong
Bán kính uốn: Chọn bán kính uốn phù hợp dựa trên độ dày thành ống và đặc tính vật liệu. Bán kính quá nhỏ có thể dẫn đến kéo giãn quá mức ở mặt ngoài và nén ở mặt trong, dẫn đến biến dạng.
Thực hiện theo Nguyên tắc “Bán kính uốn tối thiểu”: Bán kính uốn tối thiểu thường bằng 3-5 lần đường kính ống để giảm sự tập trung ứng suất.
3.2 Kiểm soát tốc độ uốn
Tốc độ uốn: Tốc độ uốn quá nhanh có thể dẫn đến phân bố ứng suất không đều, gây ra biến dạng cục bộ và phục hồi. Ngược lại, tốc độ quá chậm có thể gây ra quá trình làm cứng nguội. Hiện đại máy uốn ống với hệ thống điều khiển CNC có thể được lập trình để xử lý tốc độ uốn cho các vật liệu khác nhau.
3.3 Sử dụng quy trình uốn nhiều lần
Uốn nhiều bước: Thực hiện nhiều bước uốn có thể làm giảm hiệu quả ứng suất ở mỗi lần uốn, do đó làm giảm độ nảy và biến dạng.
3.4 Khuôn máy uốn tùy chỉnh
Chọn khuôn uốn phù hợp với bán kính cong và kích thước phù hợp với thông số kỹ thuật của ống và bảo dưỡng khuôn thường xuyên để đảm bảo bề mặt nhẵn, giảm thiểu hư hỏng ống trong quá trình uốn.
4.0 Những câu hỏi và câu trả lời thường gặp về ứng suất và biến dạng trong ống uốn
Những loại ứng suất nào xảy ra trong ống uốn kim loại?
Ứng suất kéo (mặt ngoài), ứng suất nén (mặt trong) và ứng suất cắt.
Mối quan hệ giữa bán kính uốn tối thiểu và ứng suất là gì?
Bán kính nhỏ hơn sẽ dẫn đến ứng suất cao hơn, có khả năng khiến các đặc tính ban đầu của vật liệu bị hỏng.
Tại sao ứng suất dư lại xảy ra trong quá trình uốn?
Ứng suất dư xảy ra do ứng suất bên trong chưa được giải phóng hoàn toàn trong quá trình uốn.
Làm thế nào để giảm biến dạng khi uốn?
Sử dụng các công cụ uốn thích hợp và máy uốn điều khiển bằng CNC để kiểm soát bán kính, tránh kéo giãn hoặc nén quá mức.
Hiện tượng hồi phục là gì?
Sự phục hồi là khi vật liệu trở lại một phần hình dạng ban đầu sau khi uốn cong, gây ra độ lệch.
Tài liệu tham khảo
- Những ứng suất hấp dẫn trong uốn ống https://www.comsol.com/blogs/the-intriguing-stresses-in-pipe-bends
- Bối cảnh của SIF và Chỉ số ứng suất cho Tải trọng mô men của các thành phần đường ống https://www.osti.gov/biblio/841246
- Các yếu tố tăng cường ứng suất (i-Factors), các yếu tố linh hoạt (k-Factors) và cách xác định chúng cho các thành phần đường ống kim loạiB31J – 2017 https://www.asme.org/codes-standards/find-codes-standards/b31j-stress-intensification-factors-flexibility-factors-determination-metallic-piping-components/2017/pdf