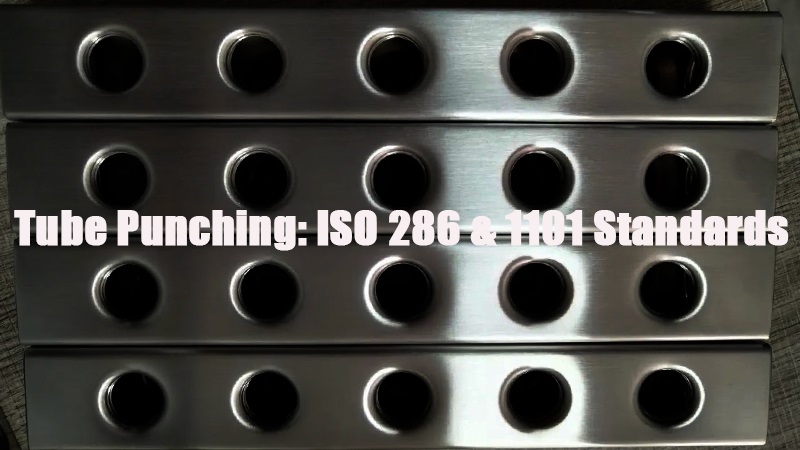
- 1.0 Основные требования к процессу пробивки отверстий в трубах
- 2.0 Применение стандартов ISO при пробивке отверстий в трубах
- 2.1 ISO 286: Стандарты допусков размеров
- 2.2 Таблица допусков размеров ISO 286 – Допуск диаметра отверстия
- 2.3 Таблица допусков размеров ISO 286 – Допуск диаметра вала
- 2.4 Таблица допусков класса IT по стандарту ISO 286
- 2.5 Таблица расчета допусков по ISO 286
- 2.6 Таблица допусков диаметров ISO 286 (диаметры отверстий и валов)
- 2.7 Таблица допусков и посадок по стандарту ISO 286
- 2.8 ISO 1101: Геометрические допуски
- 3.0 Ключевые аспекты ISO 1101: Геометрические допуски
- 4.0 ISO 2768: Общие допуски размеров
- 5.0 Расположение отверстий и другие особые соображения
- 6.0 Руководство по зазорам для штамповки мягкой стали
- 7.0 Рекомендуемое усилие для штамповки мягкой стали
Пробивка отверстий в трубах — важная технология обработки, широко используемая в таких отраслях, как машиностроение, строительство и автомобилестроение. При выполнении пробивки отверстий в трубах решающее значение имеет обеспечение точности диаметра отверстия, его положения и формы, особенно при работе с трубами из разных материалов и с разными спецификациями.
Стандарты ISO содержат подробные спецификации допусков, помогая производителям достигать высокой точности обработки и гарантировать, что каждое отверстие соответствует проектным требованиям, будь то квадратные или круглые трубы.
1.0 Основные требования к процессу пробивки отверстий в трубах
Пробивка отверстий в трубах обычно выполняется с помощью трубопробивного станка. Точность формы и положения отверстий напрямую влияет на адаптивность и эффективность сборки трубы на последующих этапах производства. Поэтому контроль точности обработки является ключом к повышению качества продукции.
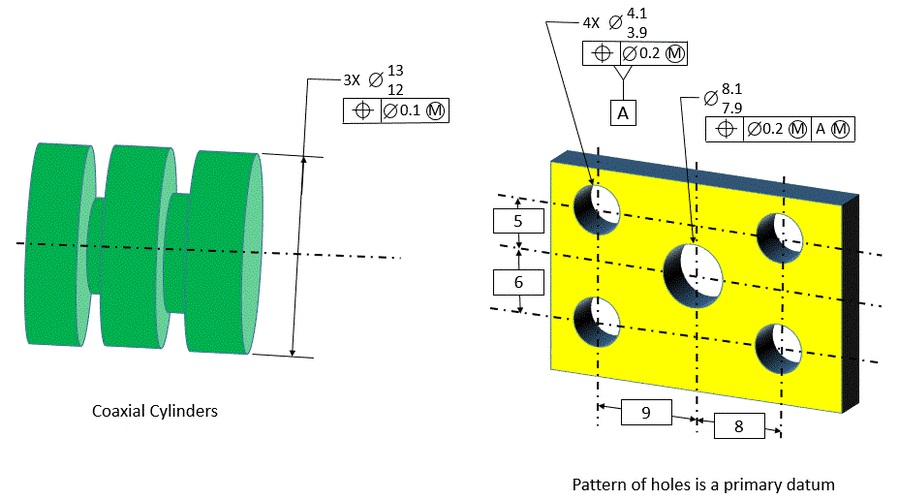
2.0 Применение стандартов ISO при пробивке отверстий в трубах
2.1 ISO 286: Стандарты допусков размеров
ISO 286 содержит спецификации допусков размеров при пробивке отверстий в трубах, диаметра отверстий, диаметра труб и других допусков размеров.
Соблюдение стандарта ISO 286 при пробивке отверстий в трубах гарантирует, что пробитая труба соответствует проектным требованиям, и сводит к минимуму необходимость доработки или появления несоответствующей продукции из-за проблем с допусками.
Допуски ISO для отверстий (ISO 286-2) | ||||||||||||||||||||
Номинальные размеры отверстий (мм) | ||||||||||||||||||||
над | 3 | 6 | 10 | 18 | 30 | 40 | 50 | 65 | 80 | 100 | 120 | 140 | 160 | 180 | 200 | 225 | 250 | 280 | 315 | 355 |
вкл. | 6 | 10 | 18 | 30 | 40 | 50 | 65 | 80 | 100 | 120 | 140 | 160 | 180 | 200 | 225 | 250 | 280 | 315 | 355 | 400 |
микрометры | ||||||||||||||||||||
Е6 | 28 | 34 | 43 | 53 | 66 | 79 | 94 | 110 | 129 | 142 | 161 | |||||||||
20 | 25 | 32 | 40 | 50 | 60 | 72 | 85 | 100 | 110 | 125 | ||||||||||
Е7 | 32 | 40 | 50 | 61 | 75 | 90 | 107 | 125 | 146 | 162 | 185 | |||||||||
20 | 25 | 32 | 40 | 50 | 60 | 72 | 85 | 100 | 110 | 125 | ||||||||||
Е11 | 95 | 115 | 142 | 170 | 210 | 250 | 292 | 335 | 390 | 430 | 485 | |||||||||
20 | 25 | 32 | 40 | 50 | 60 | 72 | 85 | 100 | 110 | 125 | ||||||||||
Е12 | 140 | 175 | 212 | 250 | 300 | 360 | 422 | 485 | 560 | 630 | 695 | |||||||||
20 | 25 | 32 | 40 | 50 | 60 | 72 | 85 | 100 | 110 | 125 | ||||||||||
Е13 | 200 | 245 | 302 | 370 | 440 | 520 | 612 | 715 | 820 | 920 | +1 015 | |||||||||
20 | 25 | 32 | 40 | 50 | 60 | 72 | 85 | 100 | 110 | 125 | ||||||||||
Ф6 | 18 | 22 | 27 | 33 | 41 | 49 | 58 | 68 | 79 | 88 | 98 | |||||||||
10 | 13 | 16 | 20 | 2 | 30 | 36 | 43 | 50 | 56 | 62 | ||||||||||
Ф7 | 22 | 28 | 34 | 41 | 50 | 60 | 71 | 83 | 96 | 108 | 119 | |||||||||
10 | 13 | 16 | 20 | 25 | 30 | 36 | 43 | 50 | 56 | 62 | ||||||||||
Ф8 | 28 | 35 | 43 | 53 | 64 | 76 | 90 | 106 | 122 | 137 | 151 | |||||||||
10 | 13 | 16 | 20 | 25 | 30 | 36 | 43 | 50 | 56 | 62 | ||||||||||
Г6 | 12 | 14 | 17 | 20 | 25 | 29 | 34 | 39 | 44 | 49 | 54 | |||||||||
4 | 5 | 6 | 7 | 9 | 10 | 12 | 14 | 15 | 17 | 18 | ||||||||||
G7 | 16 | 20 | 24 | 28 | 34 | 40 | 47 | 54 | 61 | 69 | 75 | |||||||||
4 | 5 | 6 | 7 | 9 | 10 | 12 | 14 | 15 | 17 | 18 | ||||||||||
G8 | 22 | 27 | 33 | 40 | 48 | 56 | 66 | 77 | 87 | 98 | 107 | |||||||||
4 | 5 | 6 | 7 | 9 | 10 | 12 | 14 | 15 | 17 | 18 | ||||||||||
Н6 | 8 | 9 | 11 | 13 | 16 | 19 | 22 | 25 | 29 | 32 | 36 | |||||||||
0 | 0 | 0 | 0 | 0 | 0 | 0 | 0 | 0 | 0 | 0 | ||||||||||
Н7 | 12 | 15 | 18 | 21 | 25 | 30 | 35 | 40 | 46 | 52 | 57 | |||||||||
0 | 0 | 0 | 0 | 0 | 0 | 0 | 0 | 0 | 0 | 0 | ||||||||||
Н8 | 18 | 22 | 27 | 33 | 39 | 46 | 54 | 63 | 72 | 81 | 89 | |||||||||
0 | 0 | 0 | 0 | 0 | 0 | 0 | 0 | 0 | 0 | 0 | ||||||||||
Н9 | 30 | 36 | 43 | 52 | 62 | 74 | 87 | 100 | 115 | 130 | 140 | |||||||||
0 | 0 | 0 | 0 | 0 | 0 | 0 | 0 | 0 | 0 | 0 | ||||||||||
Н10 | 48 | 58 | 70 | 84 | 100 | 120 | 140 | 160 | 185 | 210 | 230 | |||||||||
0 | 0 | 0 | 0 | 0 | 0 | 0 | 0 | 0 | 0 | 0 | ||||||||||
Н11 | 75 | 90 | 110 | 130 | 160 | 190 | 220 | 250 | 290 | 320 | 360 | |||||||||
0 | 0 | 0 | 0 | 0 | 0 | 0 | 0 | 0 | 0 | 0 | ||||||||||
J6 | 5 | 5 | 6 | 8 | 10 | 13 | 16 | 18 | 22 | 25 | 29 | |||||||||
-3 | -4 | -5 | -5 | -6 | -6 | -6 | -7 | -7 | -7 | -7 | ||||||||||
J7 | 6 | 8 | 10 | 12 | 14 | 18 | 22 | 26 | 30 | 36 | 39 | |||||||||
-6 | -7 | -8 | -9 | -11 | -12 | -13 | -14 | -16 | -16 | -18 | ||||||||||
J8 | 10 | 12 | 15 | 20 | 24 | 28 | 34 | 41 | 47 | 55 | 60 | |||||||||
-8 | -10 | -12 | -13 | -15 | -18 | -20 | -22 | -25 | -26 | -29 | ||||||||||
СП6 | 4 | 4.5 | 5.5 | 6.5 | 8 | 9.5 | 11 | 12.5 | 14.5 | 16 | 18 | |||||||||
-4 | -4.5 | -5.5 | -6.5 | -8 | -9.5 | -11 | -12.5 | -14.5 | -16 | -18 | ||||||||||
СП7 | 6 | 7.5 | 9 | 10.5 | 12.5 | 15 | 17.5 | 20 | 23 | 26 | 28.5 | |||||||||
-6 | -7.5 | -9 | -10.5 | -12.5 | -15 | -17.5 | -20 | -23 | -26 | -28.5 | ||||||||||
СП8 | 9 | 11 | 13.5 | 16.5 | 19.5 | 23 | 27 | 31.5 | 36 | 40.5 | 44.5 | |||||||||
-9 | -11 | -13.5 | -16.5 | -19.5 | -23 | -27 | -31.5 | -36 | -40.5 | -44.5 | ||||||||||
К6 | 2 | 2 | 2 | 2 | 3 | 4 | 4 | 4 | 5 | 5 | 7 | |||||||||
-6 | -7 | -9 | -11 | -13 | -15 | -18 | -21 | -24 | -27 | -29 | ||||||||||
К7 | 3 | 5 | 6 | 6 | 7 | 9 | 10 | 12 | 13 | 16 | 17 | |||||||||
-9 | -10 | -12 | -15 | -18 | -21 | -25 | -28 | -33 | -36 | -40 | ||||||||||
К8 | 5 | 6 | 8 | 10 | 12 | 14 | 16 | 20 | 22 | 25 | 28 | |||||||||
-13 | -16 | -19 | -23 | -27 | -32 | -38 | -43 | -50 | -56 | -61 | ||||||||||
М6 | -1 | -3 | -4 | -4 | -4 | -5 | -6 | -8 | -8 | -9 | -10 | |||||||||
-9 | -12 | -15 | -17 | -20 | -24 | -28 | -33 | -37 | -41 | -46 | ||||||||||
М7 | 0 | 0 | 0 | 0 | 0 | 0 | 0 | 0 | 0 | 0 | 0 | |||||||||
-12 | -15 | -18 | -21 | -25 | -30 | -35 | -40 | -46 | -52 | -57 | ||||||||||
М8 | 2 | 1 | 2 | 4 | 5 | 5 | 6 | 8 | 9 | 9 | 11 | |||||||||
-16 | -21 | -25 | -29 | -34 | -41 | -48 | -55 | -63 | -72 | -78 | ||||||||||
Н6 | -5 | -7 | -9 | -11 | -12 | -14 | -16 | -20 | -22 | -25 | -26 | |||||||||
-13 | -16 | -20 | -24 | -28 | -33 | -38 | -45 | -51 | -57 | -62 | ||||||||||
Н7 | -4 | -4 | -5 | -7 | -8 | -9 | -10 | -12 | -14 | -14 | -16 | |||||||||
-16 | -19 | -23 | -28 | -33 | -39 | -45 | -52 | -60 | -66 | -73 | ||||||||||
Н8 | -2 | -3 | -3 | -3 | -3 | -4 | -4 | -4 | -5 | -5 | -5 | |||||||||
-20 | -25 | -30 | -36 | -42 | -50 | -58 | -67 | -77 | -86 | -94 | ||||||||||
П6 | -9 | -12 | -15 | -18 | -21 | -26 | -30 | -36 | -41 | -47 | -51 | |||||||||
-17 | -21 | -26 | -31 | -37 | -45 | -52 | -61 | -70 | -79 | -87 | ||||||||||
П7 | -8 | -9 | -11 | -14 | -17 | -21 | -24 | -28 | -33 | -36 | -41 | |||||||||
-20 | -24 | -29 | -35 | -42 | -51 | -59 | -68 | -79 | -88 | -98 | ||||||||||
П8 | -12 | -15 | -18 | -22 | -26 | -32 | -37 | -43 | -50 | -56 | -62 | |||||||||
-30 | -37 | -45 | -55 | -65 | -78 | -91 | -106 | -122 | -137 | -151 | ||||||||||
Р6 | -12 | -16 | -20 | -24 | -29 | -35 | -37 | -44 | -47 | -56 | -58 | -61 | -68 | -71 | -75 | -85 | -89 | -97 | -103 | |
-20 | -25 | -31 | -37 | -45 | -54 | -56 | -66 | -69 | -81 | -83 | -86 | -97 | -100 | -104 | -117 | -121 | -133 | -139 | ||
Р7 | -11 | -13 | -16 | -20 | -25 | -30 | -32 | -38 | -41 | -48 | -50 | -53 | -60 | -63 | -67 | -74 | -78 | -87 | -93 | |
-23 | -28 | -34 | -41 | -50 | -60 | -62 | -73 | -76 | -88 | -90 | -93 | -106 | -109 | -113 | -126 | -130 | -144 | -150 |
2.2 Таблица допусков размеров ISO 286 – Допуск диаметра отверстия
В данной таблице описаны допуски диаметра отверстий на основе различных классов IT (классов допуска) для различных диапазонов диаметров отверстий.
Диапазон размеров (мм) | IT7 Допуск (мм) | IT8 Допуск (мм) | Допуск IT9 (мм) |
1 – 3 | ±0,020 | ±0,025 | ±0,030 |
3 – 6 | ±0,025 | ±0,030 | ±0,035 |
6 – 10 | ±0,030 | ±0,035 | ±0,040 |
10 – 18 | ±0,035 | ±0,040 | ±0,045 |
18 – 30 | ±0,040 | ±0,045 | ±0,050 |
30 – 50 | ±0,050 | ±0,060 | ±0,070 |
2.3 Таблица допусков размеров ISO 286 – Допуск диаметра вала
В данной таблице приведены допуски на диаметр вала в зависимости от различных классов IT.
Диапазон размеров (мм) | IT7 Допуск (мм) | IT8 Допуск (мм) | Допуск IT9 (мм) |
1 – 3 | ±0,020 | ±0,025 | ±0,030 |
3 – 6 | ±0,025 | ±0,030 | ±0,035 |
6 – 10 | ±0,030 | ±0,035 | ±0,040 |
10 – 18 | ±0,035 | ±0,040 | ±0,045 |
18 – 30 | ±0,045 | ±0,050 | ±0,060 |
30 – 50 | ±0,060 | ±0,070 | ±0,080 |
2.4 Таблица допусков класса IT по стандарту ISO 286
В этой таблице показан диапазон допусков для различных классов IT, что помогает выбрать подходящую точность допуска.
Уровень ИТ | Диапазон допуска (мм) |
IT01 | ±0,0025 |
ИТ2 | ±0,005 |
ИТ3 | ±0,010 |
IT4 | ±0,015 |
ИТ5 | ±0,025 |
IT6 | ±0,050 |
IT7 | ±0,080 |
IT8 | ±0,120 |
IT9 | ±0,180 |
2.5 Таблица расчета допусков по ISO 286
В этой таблице показаны допустимые отклонения между отверстиями и валами для различных допусков (например, H7 и H7).
Тип посадки | Допуск отверстия (мм) | Допуск вала (мм) |
Н7 | ±0,025 | 0.000 |
Н8 | ±0,030 | 0.000 |
h7 | ±0,025 | ±0,000 |
h8 | ±0,030 | ±0,000 |
2.6 Таблица допусков диаметров ISO 286 (диаметры отверстий и валов)
В данной таблице приведены допуски на диаметры отверстий и валов в различных размерных диапазонах, применимые для контроля точности посадки при механической обработке.
Диапазон размеров (мм) | Допуск отверстия (мм) | Допуск вала (мм) |
3 – 6 | ±0,025 | ±0,020 |
6 – 10 | ±0,035 | ±0,030 |
10 – 18 | ±0,045 | ±0,035 |
18 – 30 | ±0,060 | ±0,045 |
30 – 50 | ±0,080 | ±0,060 |
2.7 Таблица допусков и посадок по стандарту ISO 286
В этой таблице перечислены различные допуски (например, H7, h7 и P7) для посадок отверстий и валов, что помогает обеспечить точность посадки.
Тип посадки | Допуск отверстия (мм) | Допуск вала (мм) |
Н7 | ±0,025 | 0.000 |
Н8 | ±0,030 | 0.000 |
h7 | ±0,025 | ±0,000 |
h8 | ±0,030 | ±0,000 |
П7 | ±0,030 | 0.000 |
2.8 ISO 1101: Геометрические допуски
Стандарт ISO 1101 гарантирует, что положение и форма отверстия после пробивки соответствуют требованиям конструкции, особенно для прецизионной обработки, где точность положения отверстия имеет решающее значение. Правильно устанавливая геометрические допуски, производители могут гарантировать точное положение и форму каждого отверстия, избегая ошибок при сборке и сварке.
ISO 1101 — это международный стандарт, определяющий геометрические допуски для механических деталей, такие как их форма, точность размеров и требования к сборке. Он предоставляет символы и методы для указания допустимых геометрических отклонений в процессах производства и сборки. Геометрические допуски обычно применяются к деталям, требующим высокой точности, таким как подшипники, шестерни и рейки.
3.0 Ключевые аспекты ISO 1101: Геометрические допуски
Символы геометрических допусков
ISO 1101 определяет различные символы для представления различных геометрических требований. Общие геометрические символы допусков включают:
- Прямолинейность (⎯): Гарантирует, что поверхность или контур остаются прямыми в указанном диапазоне.
- Плоскость (▭): Гарантирует, что поверхность остается в пределах заданной плоской плоскости.
- Округлость (О): Обеспечивает округлость круглого контура в допустимых пределах.
- Цилиндричность (◯): Гарантирует, что цилиндрическая форма остается в пределах указанного диапазона допусков как для оси, так и для диаметра.
- Перпендикулярность (⊥): Обеспечивает перпендикулярность двух поверхностей или осей.
- Параллелизм (∥): Обеспечивает параллельность двух поверхностей или линий.
- Концентричность (⌀): Обеспечивает перекрытие осей двух круглых элементов.
- Допуск положения (⊙): Определяет допуск расположения отверстий, валов или других элементов в пространстве.
3.1 Геометрические допуски с указанием размеров
Геометрические допуски обычно сочетаются с размерами для указания точной формы и требований к сборке заготовки. Например:
- Геометрические допуски отверстий: часто используются для указания положения и отклонения отверстий в плоскости.
- Геометрические допуски вала: могут включать прямолинейность, круглость или концентричность.
3.2 Применение геометрических допусков
На практике геометрические допуски используются наряду с другими размерными допусками, чтобы гарантировать, что продукт может функционировать правильно во время сборки и использования. ISO 1101 содержит подробные правила интерпретации и применения этих символов допусков, чтобы гарантировать, что производственные процессы соответствуют проектным спецификациям.
3.3 Таблицы общих геометрических допусков
Тип допуска | Символ | Значение | Область применения |
Прямолинейность | ⎯ | Гарантирует, что поверхность или линия находится в заданном диапазоне прямолинейности. | Используется для всех линейных контуров и поверхностей. |
Плоскостность | ▭ | Гарантирует, что поверхность плоская, а все точки находятся в пределах заданной плоскости. | Используется для плоских обработанных деталей |
Округлость | О | Гарантирует, что контур находится в пределах указанного диапазона округлости | Используется для круглых элементов, таких как валы и отверстия. |
Цилиндричность | ◯ | Гарантирует, что цилиндрическая поверхность находится в указанном диапазоне цилиндричности. | Используется для всех цилиндрических деталей. |
Перпендикулярность | ⊥ | Обеспечивает перпендикулярное отношение между двумя поверхностями или осями | Используется для деталей, требующих точной сборки. |
Параллелизм | ∥ | Обеспечивает параллельность двух поверхностей или линий | Используется для компонентов, требующих точной сборки. |
4.0 ISO 2768: Общие допуски размеров
ISO 2768 содержит общие рекомендации по допускам для размеров в механическом проектировании, которые включают допуски размеров как для линейных, так и для угловых размеров. Он часто используется для некритических размеров, которые не требуют точного контроля допусков. Для пробивки отверстий в трубах этот стандарт помогает поддерживать общую точность размеров для деталей, которые не участвуют напрямую в ключевых функциональных соединениях, но все же должны соответствовать стандартам качества.
4.1 Таблица допусков ISO 2768 – Общие допуски для линейных размеров
Размеры (мм) | Допуск (мм) |
0.5 – 3 | ±0,05 |
3 – 6 | ±0,10 |
6 – 30 | ±0,15 |
30 – 120 | ±0,20 |
120 – 400 | ±0,30 |
400 – 1000 | ±0,50 |
4.2 Таблица допусков ISO 2768 – Общие допуски для угловых размеров
Угол (°) | Допуск (°) |
0 – 10 | ±1,0 |
10 – 30 | ±1,5 |
30 – 90 | ±2,0 |
90 – 180 | ±2,5 |
Эти допуски применяются для обеспечения правильной сборки деталей, даже если они не столь критичны с точки зрения точности размеров.
5.0 Расположение отверстий и другие особые соображения
Помимо размерных и геометрических допусков, контроль положения отверстий является еще одним критическим фактором при пробивке отверстий в трубах. Положение отверстий относительно общей конструкции трубы должно соответствовать указанным в проекте позиционным допускам. ISO 1101 определяет, как определять позиционные допуски для отверстий, гарантируя, что отверстия пробиты в правильных местах относительно трубы.
Допуск положения (ISO 1101): Допуск положения определяет допустимое отклонение для расположения отверстия. Обычно он определяется точкой отсчета или базой и имеет решающее значение для обеспечения правильного совмещения отверстий с другими деталями, например, когда трубы свариваются или устанавливаются с другими компонентами.
6.0 Руководство по зазорам для штамповки мягкой стали
Руководство по зазорам для штамповки мягкой стали | |||||||||||||||||||
Толщина мягкой стали | |||||||||||||||||||
Ударить кулаком Размер |
1/8 | 1/4 | 3/8 | 1/2 | 5/8 | 3/4 | 7/8 | 1″ | |||||||||||
3/16 | 13/64 | ||||||||||||||||||
1/4 | 17/64 | ||||||||||||||||||
5/16 | 21/64 | 11/32 | |||||||||||||||||
3/8 | 25/64 | 13/32 | 13/32 | ||||||||||||||||
7/16 | 29/64 | 15/32 | 15/32 | ||||||||||||||||
1/2 | 33/64 | 17/32 | 17/32 | 9/16 | |||||||||||||||
9/16 | 37/64 | 19/32 | 19/32 | 5/8 | |||||||||||||||
5/8 | 41/64 | 21/32 | 21/32 | 11/16 | 11/16 | ||||||||||||||
11/16 | 45/64 | 23/32 | 23/32 | 3/4 | 3/4 | ||||||||||||||
3/4 | 49/64 | 25/32 | 25/32 | 13/16 | 13/16 | 27/32 | |||||||||||||
13/16 | 53/64 | 27/32 | 27/32 | 7/8 | 7/8 | 29/32 | |||||||||||||
7/8 | 57/64 | 29/32 | 29/32 | 15/16 | 15/16 | 31/32 | 31/32 | ||||||||||||
15/16 | 61/64 | 31/32 | 31/32 | 1 | 1 | 1-1/32 | 1-1/32 | ||||||||||||
1 | 1-1/64 | 1-1/32 | 1-1/32 | 1-1/16 | 1-1/16 | 1-3/32 | 1-3/32 | 1-1/8 | |||||||||||
1-1/16 | 1-5/64 | 1-3/32 | 1-3/32 | 1-1/8 | 1-1/8 | 1-5/32 | 1-5/32 | 1-3/16 | |||||||||||
1-1/8 | 1-9/64 | 1-5/32 | 1-5/32 | 1-3/16 | 1-3/16 | 1-7/32 | 1-7/32 | 1-1/4 | |||||||||||
1-3/16 | 1-13/64 | 1-7/32 | 1-7/32 | 1-1/4 | 1-1/4 | 1-9/32 | 1-9/32 | 1-5/16 | |||||||||||
1-1/4 | 1-17/64 | 1-9/32 | 1-9/32 | 1-5/16 | 1-5/16 | 1-11/32 | 1-11/32 | 1-3/8 | |||||||||||
1-5/16 | 1-21/64 | 1-11/32 | 1-11/32 | 1-3/8 | 1-3/8 | 1-13/32 | 1-13/32 | 1-7/16 | |||||||||||
1-3/8 | 1-25/64 | 1-13/32 | 1-13/32 | 1-7/16 | 1-7/16 | 1-15/32 | 1-15/32 | 1-1/2 | |||||||||||
1-7/16 | 1-29/64 | 1-15/32 | 1-15/32 | 1-1/2 | 1-1/2 | 1-17/32 | 1-17/32 | 1-9/16 | |||||||||||
1-1/2 | 1-33/64 | 1-17/32 | 1-17/32 | 1-9/16 | 1-9/16 | 1-19/32 | 1-19/32 | 1-5/8 |
7.0 Рекомендуемое усилие для штамповки мягкой стали
Рекомендуемое усилие для штамповки мягкой стали | |||||||||||||||||||||
Толщина Мягкая сталь |
Размер пуансона | ||||||||||||||||||||
3/16 | 1/4 | 5/16 | 3/8 | 7/16 | 1/2 | 9/16 | 5/8 | 11/16 | 3/4 | 13/16 | 7/8 | 15/16 | 1″ | 1-1/8 | 1-1/4 | ||||||
3/16 1/4 |
.187 | 3 | 4 | 5 | 6 | 7 | 7 | 8 | 9 | 10 | 11 | 12 | 13 | 14 | 15 | 17 | 19 | ||||
.250 | 5 | 6 | 8 | 9 | 10 | 11 | 12 | 14 | 15 | 16 | 18 | 19 | 20 | 22 | 25 | ||||||
3/8 | .375 | 11 | 13 | 15 | 17 | 19 | 21 | 22 | 24 | 26 | 28 | 30 | 34 | 38 | |||||||
1/2 | .500 | 20 | 22 | 25 | 28 | 30 | 32 | 35 | 38 | 40 | 45 | 50 | |||||||||
5/8 | .625 | 31 | 34 | 38 | 41 | 44 | 47 | 50 | 56 | 62 | |||||||||||
3/4 | .750 | 45 | 49 | 52 | 56 | 60 | 68 | 75 | |||||||||||||
7/8 | .875 | 61 | 66 | 70 | 79 | 88 | |||||||||||||||
1 | |||||||||||||||||||||
1.000 | 80 | 90 |
7.1 Заключение
Стандарты допуска ISO играют решающую роль в обеспечении точности выполнения пробивки отверстий в трубах и других операций по обработке. Соблюдая эти международно признанные стандарты, производители могут гарантировать, что пробитые отверстия соответствуют как размерным, так и геометрическим требованиям, что приводит к выпуску высококачественной и надежной продукции.
7.2 Приложение: Обычно используемые допуски при пробивке отверстий в трубах
Тип | Допуск (мм) | Примечания |
Диаметр отверстия | ±0,10 – ±0,20 | Зависит от размера и материала трубы |
Положение отверстия | ±0,10 – ±0,20 | На основе опорной точки или исходной точки |
Перпендикулярность | ±0,05 – ±0,10 | Обеспечивает перпендикулярность отверстий трубе |
Круглость отверстий | ±0,05 – ±0,10 | Обеспечивает круглость отверстий |
Плоскостность отверстия | ±0,05 – ±0,10 | Обеспечивает ровность поверхности пробитого отверстия |
Используя эти таблицы и следуя соответствующим стандартам, производители могут гарантировать точность процесса пробивки отверстий и правильную стыковку труб в конечном изделии.
https://www.dimensionalconsulting.com/tolerance-of-position.html
https://slideplayer.com/slide/15857807/
https://www.clevelandsteeltool.com/