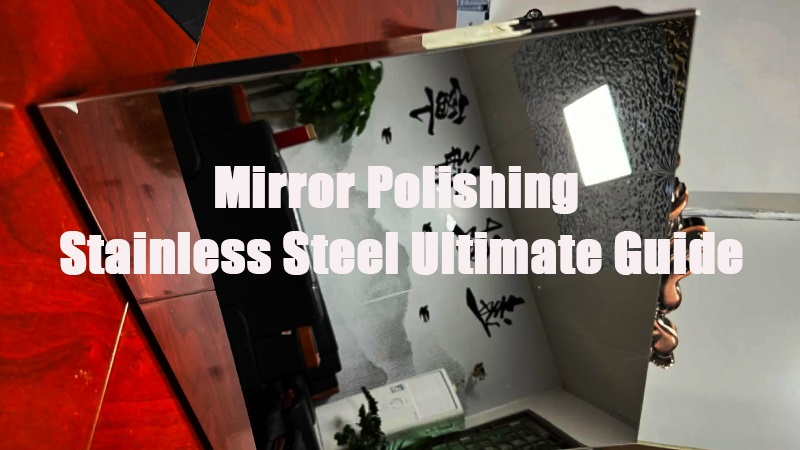
- 1.0 Definition and Purpose of Mirror Polishing
- 2.0 Common Polishing Grades
- 3.0 What is No. 8 Finish?
- 4.0 Applications of Mirror Polishing in Industry
- 5.0 Overview of the Stainless Steel Mirror Polishing Process
- 6.0 Stainless Steel Mirror Polishing Techniques
- 7.0 Types and Selection of Mirror Polishing Machine
- 8.0 Types of Polishing Agents and Selection Recommendations
- 9.0 How to Address Overheating Issues During Polishing
- 10.0 Remedies for Fine Scratches
- 11.0 Maintenance and Care for Polished Stainless Steel
- 12.0 Daily Maintenance Tips to Prevent Oxidation and Scratches
- 13.0 Cleaning Methods for Mirror Polished Stainless Steel
- 14.0 How to Achieve a Matte or Brushed Effect
- 15.0 Common Issues and Solutions During the Polishing Process
1.0 Definition and Purpose of Mirror Polishing
The stainless steel mirror finish results from fine grinding and polishing and is characterized by high gloss and smoothness. Typically, sandpaper with a grit of over 600 and professional polishing equipment are used to ensure a flawless surface that attains the ideal mirror finish.
The No. 8 Finish, also known as mirror polishing, is a type of stainless steel surface treatment that undergoes multiple grinding and polishing stages to achieve extremely high smoothness and reflectivity. It is widely used in high-end decoration and product applications.
2.0 Common Polishing Grades
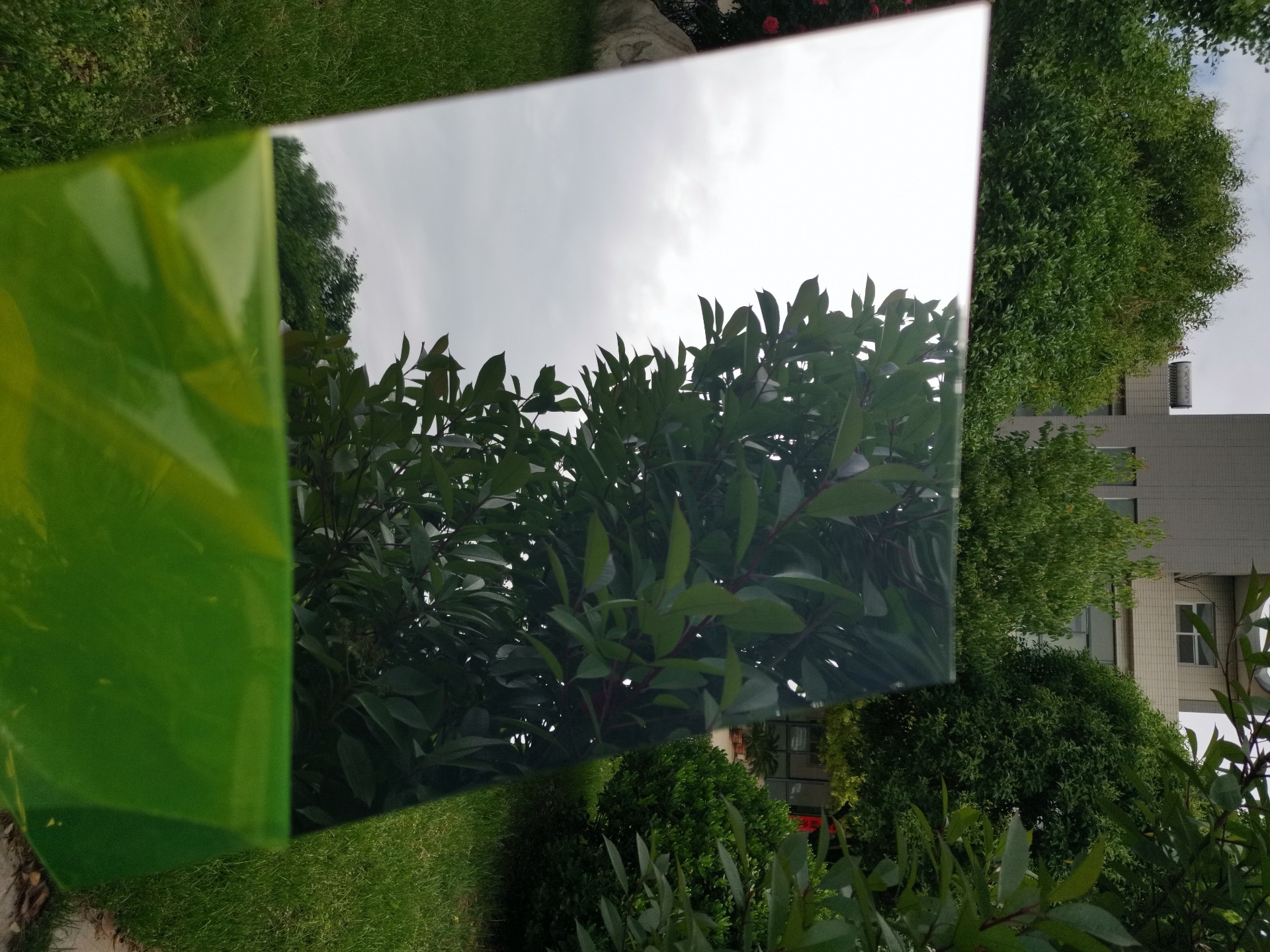
Polishing Grade | Description | Application Areas |
Buffing #400 | Basic polishing, smooth surface, moderate gloss | General decorative use, surface finishing |
Gloss Buffing Finish #600 | High gloss, fine surface | Interior architecture, appliance surfaces |
Buffed Mirror Finish NO.700 | Primary mirror effect, high smoothness | Stainless steel decorative panels, kitchen equipment |
Glazed Mirror Finish NO.8 | Premium mirror polishing, extremely high brightness | High-end decoration, luxury automotive parts |
Mirror Finish #800 | Extremely high reflectivity, nearly perfect mirror reflection | Luxury goods, electronic device casings |
Super Mirror Finish #1000 | Further enhanced smoothness, extremely high reflectivity | Precision decoration, electronic casings |
Fine Mirror Finish #1200 | Fine mirror effect, uniform surface | Art pieces, polishing high-end mechanical parts |
Ultra Mirror Finish #1500 | Highest level mirror polishing, extremely smooth surface | Medical equipment, aerospace equipment, high-end decorative parts |
3.0 What is No. 8 Finish?
No. 8 Finish is a method of treating stainless steel surfaces, also referred to as mirror polishing or “super mirror polishing.” It represents the highest level of gloss and polishing effect, achieved using sandpaper with a grit of over 600 and special polishing techniques.
Various types of stainless steel surface treatments are available under different processing methods (such as cold rolling, hot rolling, and bright annealing) and steel grades (including SUS304, SUS316, ferritic, and duplex stainless steel).
4.0 Applications of Mirror Polishing in Industry
Surface Finish Type | Thickness | Cold Rolling (NO.2B) | Hot Rolling (NO.1) | Bright Annealing (BA) | SUS304 | SUS316 | Ferritic Stainless Steel | Duplex Stainless Steel |
#800 Real Mirror Finish | All available | O | O | O | O | O | O | O |
Polished Mirror No.8 (BA) | 0.3mm-2.0mm | X | X | O | O | △ | X | X |
Buff Mirror #700k (BA) | 0.3mm-2.0mm | X | X | O | O | △ | X | X |
Combination Buff Mirror #700S K (2B) | All available | O | O | O | O | O | O | O |
Shiny Polish #700k (2B) | All available | O | O | O | O | O | O | O |
Buff Polish #400k (2B) | All available | O | O | O | O | O | O | O |
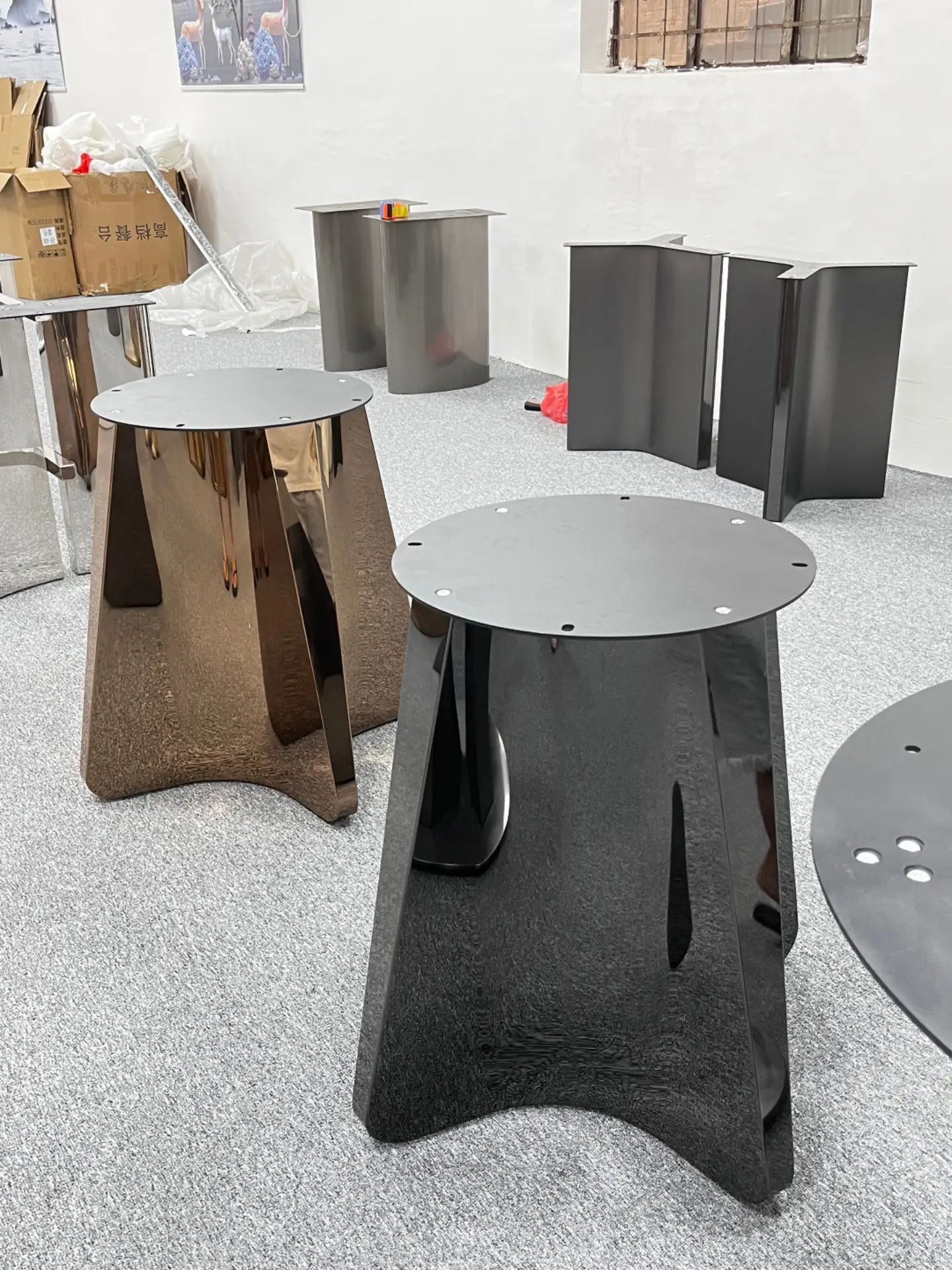
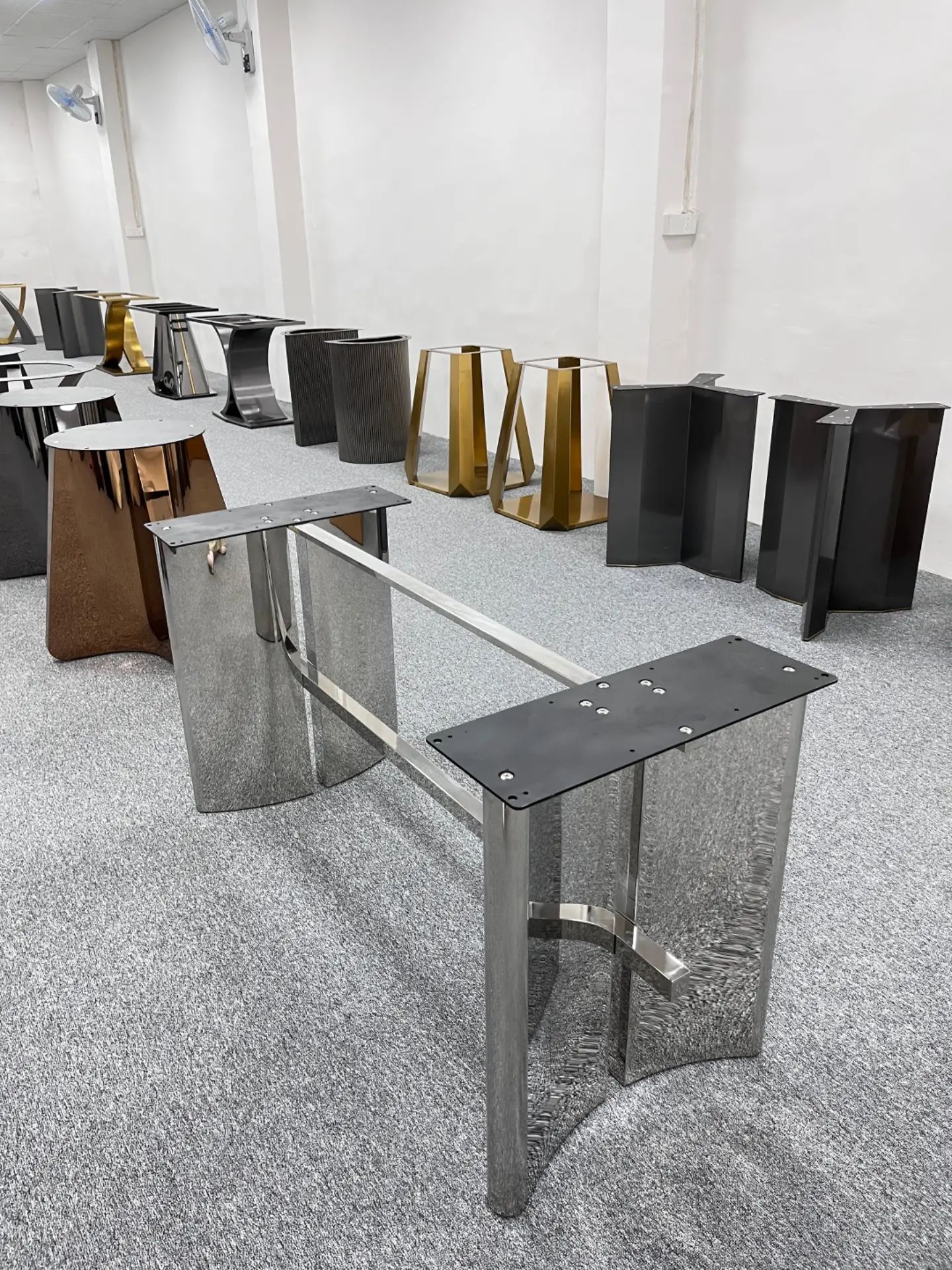
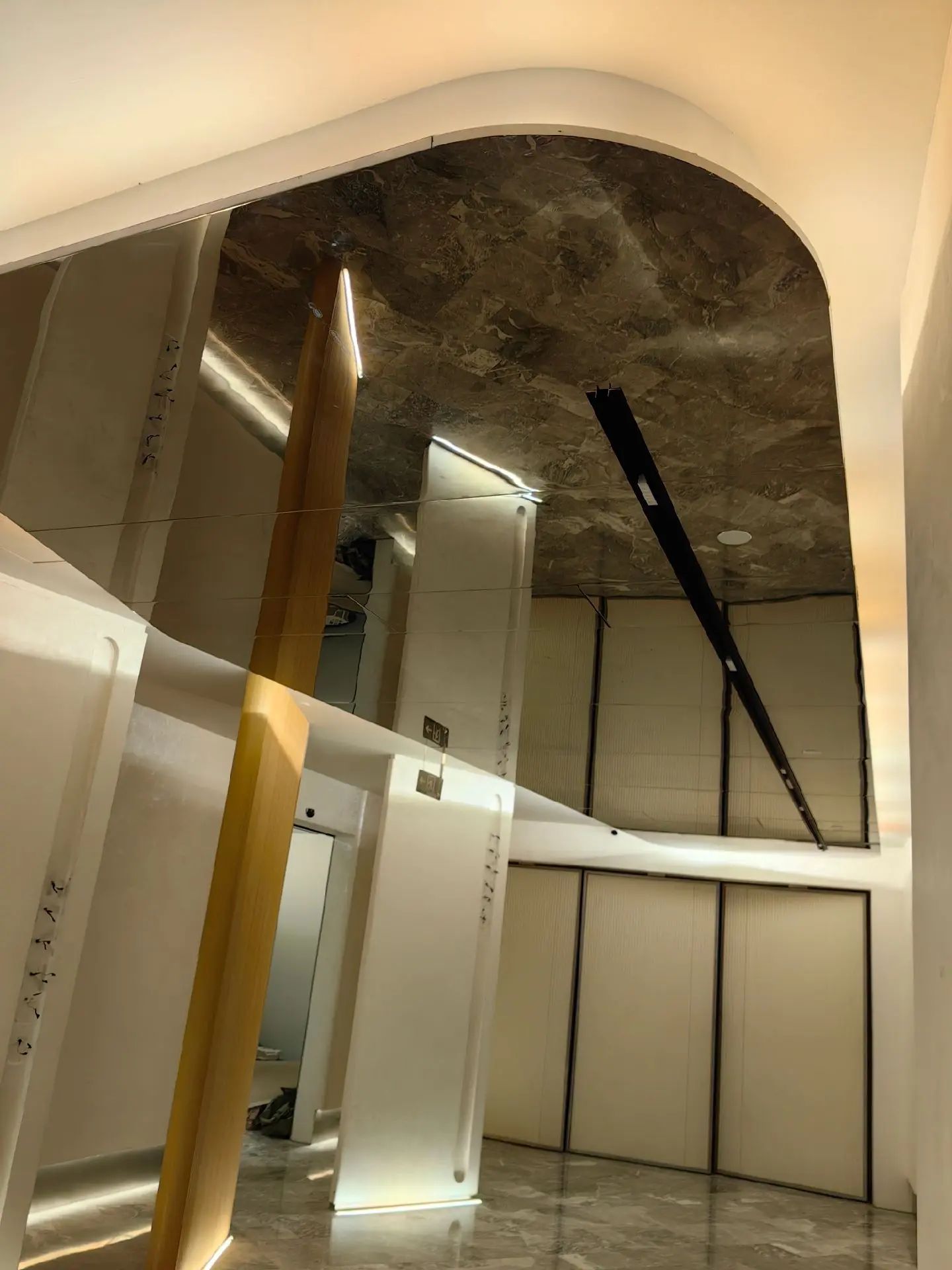
4.1 Architectural Decoration:
- Exterior Facades: Mirror stainless steel is used for building curtain walls.
- Interior Decoration: Used for walls, columns, railings, etc.
4.2 Furniture Design:
- High-End Furniture: Mirror-polished stainless steel is commonly used for the frames and decorative elements of tables and chairs.
- Decorative Accessories: Stainless steel vases, mirror frames, etc.
4.3 Home Appliances:
- Kitchen Equipment: Shells of refrigerators, ovens, and dishwashers.
- Small Appliances: Shells of coffee machines, juicers, etc.
4.4 Automotive Industry:
- Exterior Facades: Decorative strips, rims, etc.
- Interior Decoration: Mirror finish stainless steel is also commonly used in car interiors.
4.5 Art and Sculpture:
Metal works with a mirror finish are often used in art installations and sculptures.
5.0 Overview of the Stainless Steel Mirror Polishing Process
- Coarse Grinding: Use coarse sandpaper or abrasives to initially grind the stainless steel surface, removing oxidation layers and surface defects.
- Fine Grinding: Use finer sandpaper for additional smoothing, preparing the surface for polishing.
- Polishing: Employ polishing wheels and specialized polishing agents to treat the stainless steel surface, achieving the mirror finish.
- Cleaning: Thoroughly rinse the polished surface with clean water to remove any residual polishing agents and abrasive particles.
- Inspection: Check the mirror finish to ensure that the surface gloss and smoothness meet the requirements.
- Protective Treatment: A protective agent can be applied to the surface to prevent oxidation and maintain gloss, extending its lifespan.
6.0 Stainless Steel Mirror Polishing Techniques
- Initial Grinding: Use 40 to 80 grit coarse sandpaper to ensure the removal of obvious scratches.
- Progressive Refinement: Use 100 or 160-grit sandpaper, followed by 200-grit sandpaper, to ensure even grinding.
- Repeated Grinding: Depending on the condition of the metal and the amount of grinding needed, typically 4 to 8 rounds of grinding are required, gradually using finer sandpaper.
- Pressure Control: Apply consistent and light to medium pressure to avoid excessive wear or indentations.
- Final Polishing: Finally, use 2000 to 4000 grit sandpaper, then wipe the metal surface, apply the polishing compound, and polish with medium pressure.
- Check Results: Wipe with a microfiber cloth and check the gloss. If not satisfied, reapply the polishing compound for additional polishing.
7.0 Types and Selection of Mirror Polishing Machine
Mirror Polishing Machines are essential equipment for achieving high-gloss metal surface treatment and are widely used in manufacturing, decoration, and craft production.
- Manual Polishing Machine
- Automatic Polishing Machine
- Vibratory Polishing Machine
- Disc Polishing Machine
- Long Belt Polishing Machine
8.0 Types of Polishing Agents and Selection Recommendations
Choosing the right polishing agent is key to achieving high-quality polishing results. Based on the specific material type, desired gloss level, and polishing stage, the appropriate selection and combination of different polishing agents can effectively enhance polishing efficiency and results.
- Polishing Paste
Characteristics: Usually contains abrasives and lubricants, suitable for metal polishing.
Selection Recommendation: Choose different grits of polishing paste based on the desired gloss level.
- Liquid Polishing Agent
Characteristics: Suitable for mechanical polishing, easy to apply, and effectively cleans surfaces.
Selection Recommendation: Choose a suitable liquid polishing agent based on material characteristics and polishing requirements.
- Abrasive Powder
Characteristics: Suitable for coarse and fine grinding stages, with varying particle sizes and compositions.
Selection Recommendation: Select suitable abrasive powder for different materials and process stages.
- Solid Polishing Sticks
Characteristics: Solid form, suitable for small areas and detailed work.
Selection Recommendation: Choose solid polishing sticks appropriate for the target material and polishing level.
9.0 How to Address Overheating Issues During Polishing
During the polishing process, overheating can lead to material deformation, oxidation, or a decline in surface quality. Here are some suggestions for handling overheating issues:
- Control Pressure: Apply appropriate pressure to avoid excessive force.
- Adjust Polishing Speed: Lowering the speed of the Polishing machine can help reduce the generation of friction heat.
- Use Coolants: Spraying coolant or lubricant during polishing can effectively lower temperatures.
- Regularly Inspect Tools: Ensure the condition of polishing tools and materials; replace abrasives in a timely manner to avoid increased heat due to excessive wear.
10.0 Remedies for Fine Scratches
- Fine scratches can affect the appearance after polishing. Here are some remedial measures:
- Use Fine Sandpaper: Select high-grit sandpaper (such as 800 to 2000 grit) and gently sand the scratched area, ensuring even pressure.
- Apply Polishing Agent: After sanding, apply an appropriate amount of polishing agent, using a polishing cloth or pad to restore gloss.
- Local Treatment: For deeper scratches, consider using specialized scratch repair agents, following the instructions provided.
11.0 Maintenance and Care for Polished Stainless Steel
To maintain the gloss and quality of stainless steel surfaces, proper maintenance and care are crucial:
- Regular Cleaning: Use a mild detergent and soft cloth to clean the stainless steel surface regularly, preventing dust and dirt accumulation.
- Avoid Corrosive Substances: Avoid using cleaning products that contain chlorine or other corrosive ingredients to prevent damage to the surface.
- Use Protective Agents: Applying a specialized stainless steel protective agent can enhance surface protection and extend the gloss retention time.
- Regular Inspection: Periodically check the polished surface and promptly address any scratches or oxidation to maintain optimal condition.
12.0 Daily Maintenance Tips to Prevent Oxidation and Scratches
- Regular Cleaning: Use a mild detergent and soft cloth to clean the surface regularly, avoiding the accumulation of dirt and dust.
- Avoid Scratching: Use soft cloths or sponges and avoid hard cleaning tools like steel wool to minimize scratch risk.
- Protective Coatings: Regularly apply specialized stainless steel protective agents to form a protective layer that helps prevent oxidation and scratches.
- Avoid Contact with Corrosive Substances: Keep stainless steel away from acidic or corrosive materials, such as bleach and chlorine.
13.0 Cleaning Methods for Mirror Polished Stainless Steel
Warm Water and Soap: Use warm water and a neutral soap solution to gently wash the surface, removing dirt and grease.
- Soft Cloth Wiping: Wipe with a soft microfiber cloth, avoiding rough materials that could scratch the surface.
- Cleaning Agent Selection: Use cleaners specifically designed for stainless steel to effectively remove dirt without damaging the mirror gloss.
- Regular Polishing: Periodically use polishing agents to restore the mirror effect and maintain shine.
14.0 How to Achieve a Matte or Brushed Effect

Typically, you can achieve a matte finish with one or two polishing grades, such as 240 grit, followed by 300 or 400 grit.
- Achieving a Matte Effect:Use 1 to 2 polishing grades, for example, using 240 grit sandpaper, followed by 300 or 400 grit.
- Creating a Brushed Surface:Use coated sanding belts or drums with 150 to 240 grit, or medium to very fine non-woven abrasives.
- Achieving a Matte or Satin Effect:Use coated abrasives in the range of 220 to 240 grit or very fine non-woven abrasive belts, rollers, or discs.
- Pay Attention to Sanding Direction:For a brushed effect, ensure the grain goes in the same direction. Use sanding belts or wheels to set the texture pattern.
- Advantages of Brushed Finishes:Common in kitchens and well-lit spaces, brushed finishes reduce reflective light and avoid glare.
- Corrosion Resistance Considerations:Brushed finishes may reduce corrosion resistance, so a rust-resistant coating should be applied.
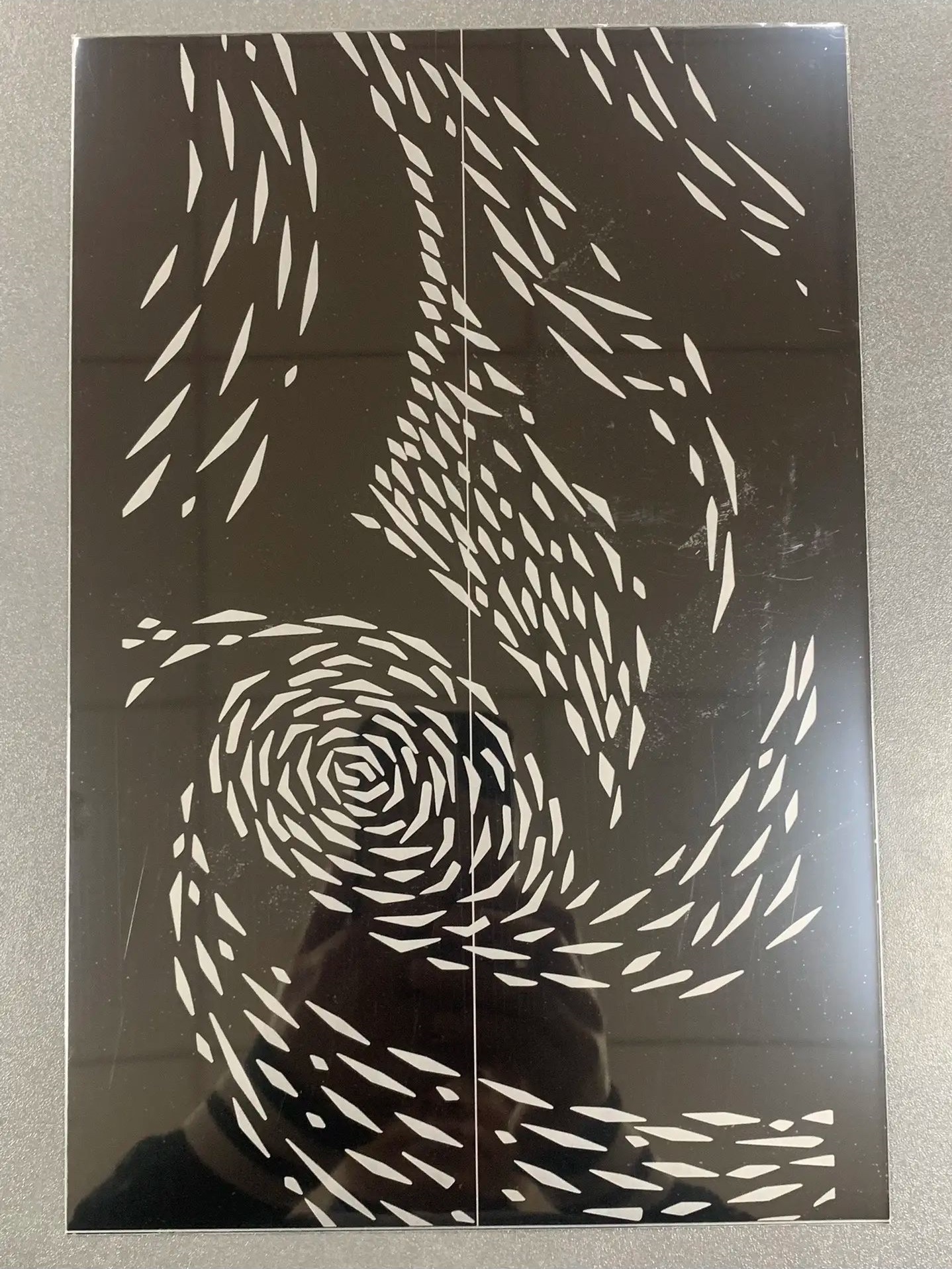
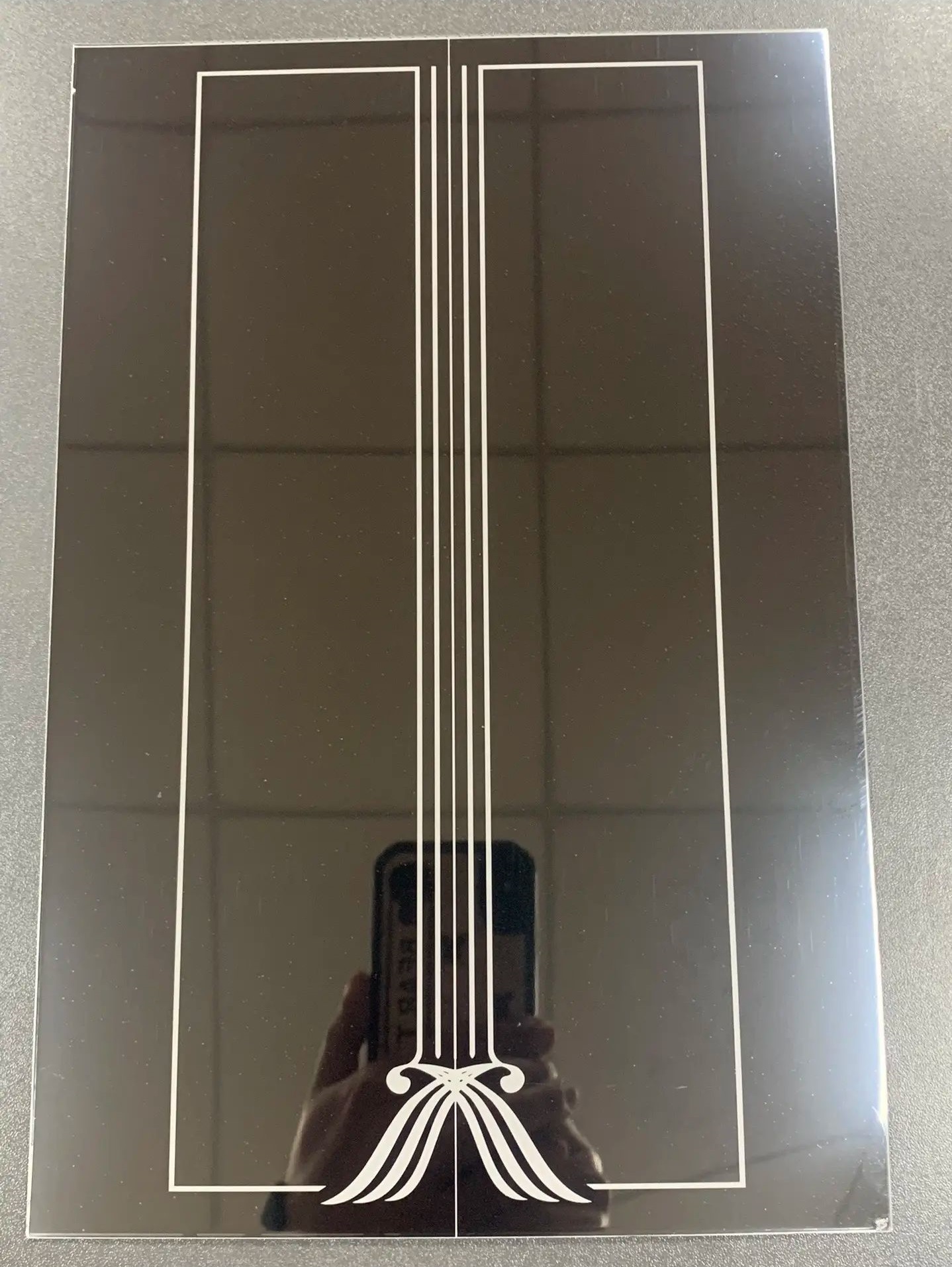
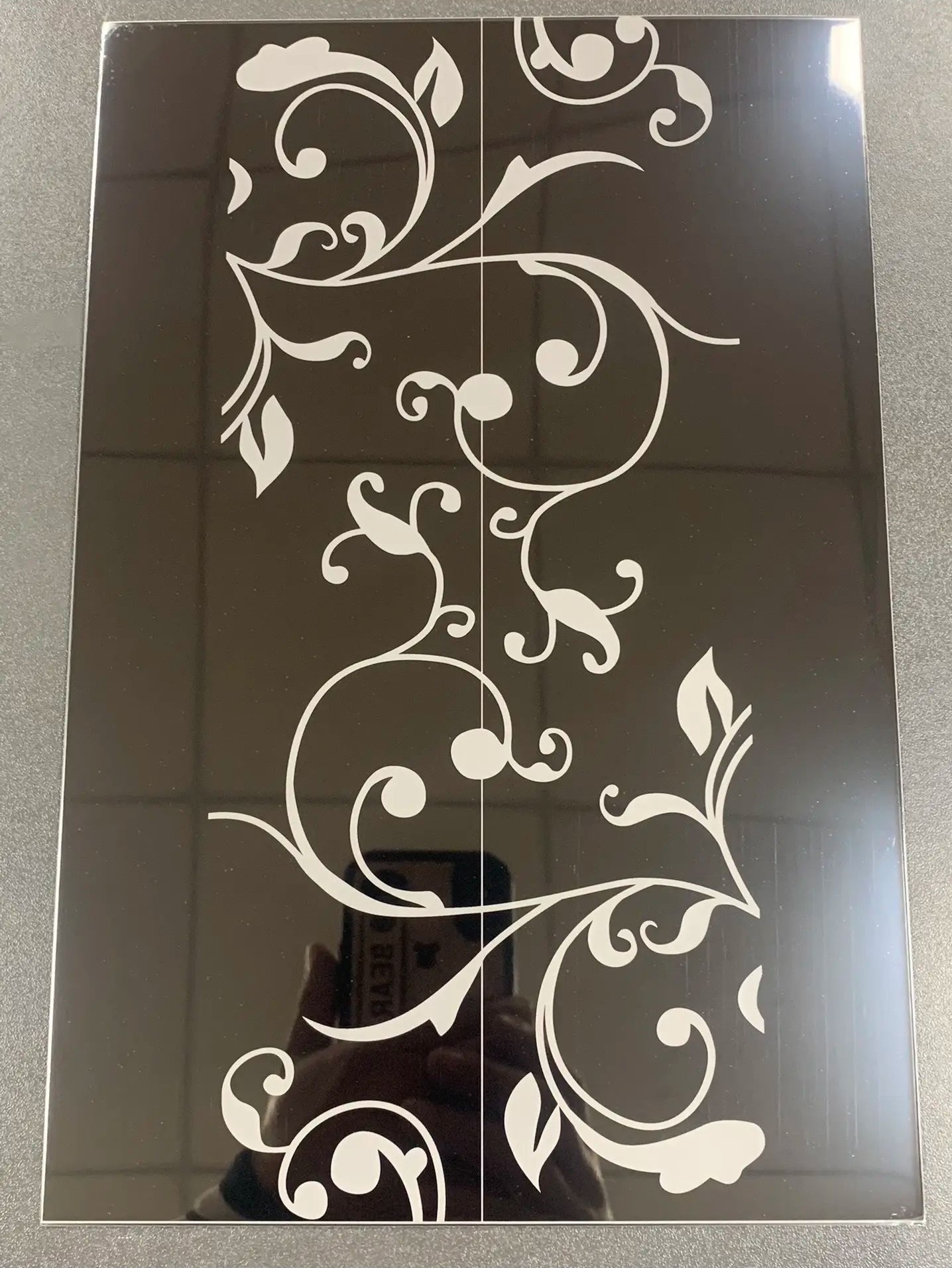
15.0 Common Issues and Solutions During the Polishing Process
Scratches on the Workpiece Surface After Polishing
Check the choice of abrasives and tools to ensure that suitable abrasives are used. Avoid staying in the same position for too long. Use fine-grit abrasives for repair.
Surface Gloss Not Meeting Expectations After Polishing
Review the polishing time and speed. Extend the polishing time or increase the amount of polishing agent used. Confirm that all polishing stages have been completed.
Uneven Surface After Polishing
Ensure consistent pressure and movement during polishing. Reapply fine grinding and polishing, paying special attention to uneven areas.
Burn Marks on the Surface
Reduce polishing speed and pressure to avoid concentrated heat. Fine grinding techniques can be used for repairs.
Residue from Polishing Agents
Thoroughly clean the surface after polishing to remove any residual polishing agents. Use warm water and a mild detergent if necessary, followed by wiping with a soft cloth. Regularly inspect the surface to ensure no residues are left, which can affect the final appearance.
References:
https://www.empireabrasives.com/blog/buff-polish-stainless-steel-beginners-guide/
https://www.onlinemetals.com/en/polishing-metal-mirror-finish
www.mako-metal.com/eng/archives/2238