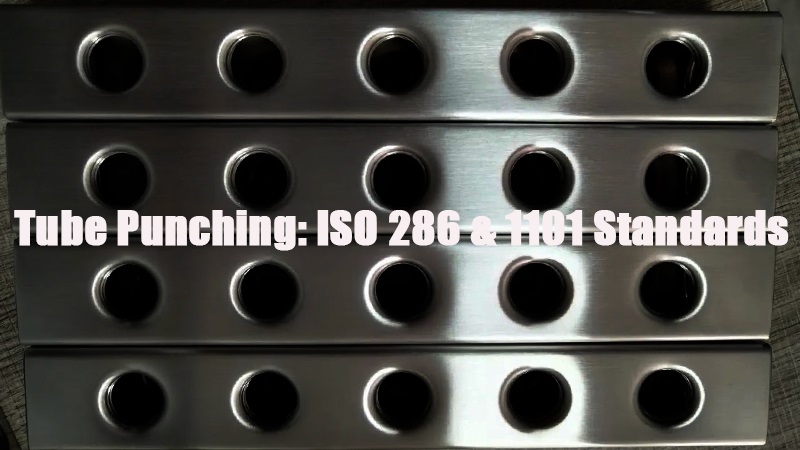
파이프 홀 펀칭은 기계, 건설, 자동차와 같은 산업에서 널리 사용되는 중요한 가공 기술입니다. 파이프 홀 펀칭을 수행할 때, 특히 다양한 재료와 사양의 파이프를 다룰 때 홀 직경, 홀 위치 및 홀 모양의 정확성을 보장하는 것이 중요합니다.
ISO 표준은 허용 오차에 대한 자세한 사양을 제공하여 제조업체가 고정밀 가공을 달성하고 각 구멍이 사각 파이프든 원형 파이프든 설계 요구 사항을 충족하는지 확인하는 데 도움이 됩니다.
1.0 파이프 홀 펀칭 가공을 위한 기본 요구 사항
파이프 홀 펀칭은 일반적으로 파이프 펀칭 머신을 사용하여 수행됩니다. 구멍 모양과 위치의 정확도는 후속 생산 단계에서 파이프의 적응성과 조립 효과에 직접적인 영향을 미칩니다. 따라서 가공 정확도를 제어하는 것이 제품 품질을 개선하는 데 중요합니다.
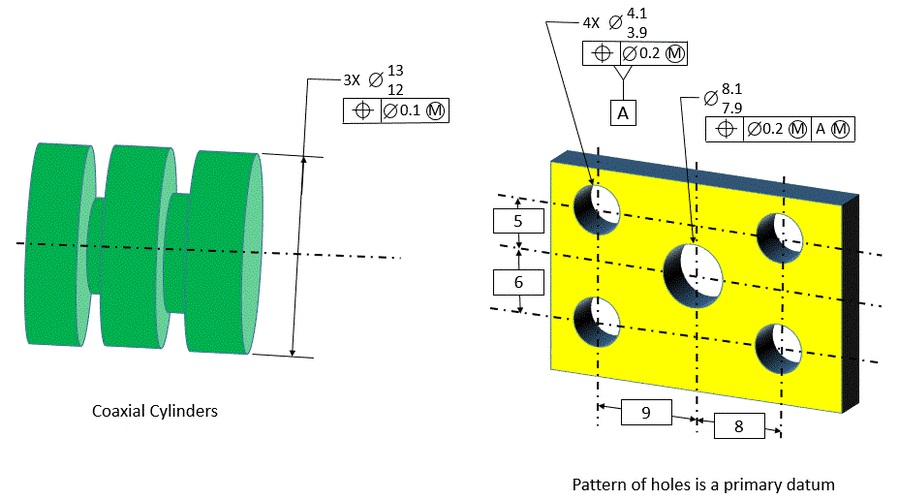
2.0 파이프 홀 펀칭에 ISO 표준 적용
2.1 ISO 286: 치수 허용 표준
ISO 286은 파이프 구멍 펀칭의 치수 공차, 구멍 직경, 파이프 직경 및 기타 치수 공차에 대한 사양을 제공합니다.
파이프 펀칭 시 ISO 286 표준을 준수하면 펀칭된 파이프가 설계 요구 사항을 충족하고 허용 오차 문제로 인해 발생하는 재작업이나 불량 제품을 최소화할 수 있습니다.
구멍에 대한 ISO 허용 오차(ISO 286-2) | ||||||||||||||||||||
공칭 구멍 크기(mm) | ||||||||||||||||||||
~ 위에 | 3 | 6 | 10 | 18 | 30 | 40 | 50 | 65 | 80 | 100 | 120 | 140 | 160 | 180 | 200 | 225 | 250 | 280 | 315 | 355 |
주식회사 | 6 | 10 | 18 | 30 | 40 | 50 | 65 | 80 | 100 | 120 | 140 | 160 | 180 | 200 | 225 | 250 | 280 | 315 | 355 | 400 |
마이크로미터 | ||||||||||||||||||||
E6 | 28 | 34 | 43 | 53 | 66 | 79 | 94 | 110 | 129 | 142 | 161 | |||||||||
20 | 25 | 32 | 40 | 50 | 60 | 72 | 85 | 100 | 110 | 125 | ||||||||||
E7 | 32 | 40 | 50 | 61 | 75 | 90 | 107 | 125 | 146 | 162 | 185 | |||||||||
20 | 25 | 32 | 40 | 50 | 60 | 72 | 85 | 100 | 110 | 125 | ||||||||||
이11 | 95 | 115 | 142 | 170 | 210 | 250 | 292 | 335 | 390 | 430 | 485 | |||||||||
20 | 25 | 32 | 40 | 50 | 60 | 72 | 85 | 100 | 110 | 125 | ||||||||||
E12 | 140 | 175 | 212 | 250 | 300 | 360 | 422 | 485 | 560 | 630 | 695 | |||||||||
20 | 25 | 32 | 40 | 50 | 60 | 72 | 85 | 100 | 110 | 125 | ||||||||||
E13 | 200 | 245 | 302 | 370 | 440 | 520 | 612 | 715 | 820 | 920 | +1 015 | |||||||||
20 | 25 | 32 | 40 | 50 | 60 | 72 | 85 | 100 | 110 | 125 | ||||||||||
F6 | 18 | 22 | 27 | 33 | 41 | 49 | 58 | 68 | 79 | 88 | 98 | |||||||||
10 | 13 | 16 | 20 | 2 | 30 | 36 | 43 | 50 | 56 | 62 | ||||||||||
F7 | 22 | 28 | 34 | 41 | 50 | 60 | 71 | 83 | 96 | 108 | 119 | |||||||||
10 | 13 | 16 | 20 | 25 | 30 | 36 | 43 | 50 | 56 | 62 | ||||||||||
F8 | 28 | 35 | 43 | 53 | 64 | 76 | 90 | 106 | 122 | 137 | 151 | |||||||||
10 | 13 | 16 | 20 | 25 | 30 | 36 | 43 | 50 | 56 | 62 | ||||||||||
G6 | 12 | 14 | 17 | 20 | 25 | 29 | 34 | 39 | 44 | 49 | 54 | |||||||||
4 | 5 | 6 | 7 | 9 | 10 | 12 | 14 | 15 | 17 | 18 | ||||||||||
G7 | 16 | 20 | 24 | 28 | 34 | 40 | 47 | 54 | 61 | 69 | 75 | |||||||||
4 | 5 | 6 | 7 | 9 | 10 | 12 | 14 | 15 | 17 | 18 | ||||||||||
G8 | 22 | 27 | 33 | 40 | 48 | 56 | 66 | 77 | 87 | 98 | 107 | |||||||||
4 | 5 | 6 | 7 | 9 | 10 | 12 | 14 | 15 | 17 | 18 | ||||||||||
H6 | 8 | 9 | 11 | 13 | 16 | 19 | 22 | 25 | 29 | 32 | 36 | |||||||||
0 | 0 | 0 | 0 | 0 | 0 | 0 | 0 | 0 | 0 | 0 | ||||||||||
H7 | 12 | 15 | 18 | 21 | 25 | 30 | 35 | 40 | 46 | 52 | 57 | |||||||||
0 | 0 | 0 | 0 | 0 | 0 | 0 | 0 | 0 | 0 | 0 | ||||||||||
H8 | 18 | 22 | 27 | 33 | 39 | 46 | 54 | 63 | 72 | 81 | 89 | |||||||||
0 | 0 | 0 | 0 | 0 | 0 | 0 | 0 | 0 | 0 | 0 | ||||||||||
H9 | 30 | 36 | 43 | 52 | 62 | 74 | 87 | 100 | 115 | 130 | 140 | |||||||||
0 | 0 | 0 | 0 | 0 | 0 | 0 | 0 | 0 | 0 | 0 | ||||||||||
H10 | 48 | 58 | 70 | 84 | 100 | 120 | 140 | 160 | 185 | 210 | 230 | |||||||||
0 | 0 | 0 | 0 | 0 | 0 | 0 | 0 | 0 | 0 | 0 | ||||||||||
H11 | 75 | 90 | 110 | 130 | 160 | 190 | 220 | 250 | 290 | 320 | 360 | |||||||||
0 | 0 | 0 | 0 | 0 | 0 | 0 | 0 | 0 | 0 | 0 | ||||||||||
J6 | 5 | 5 | 6 | 8 | 10 | 13 | 16 | 18 | 22 | 25 | 29 | |||||||||
-3 | -4 | -5 | -5 | -6 | -6 | -6 | -7 | -7 | -7 | -7 | ||||||||||
제7 | 6 | 8 | 10 | 12 | 14 | 18 | 22 | 26 | 30 | 36 | 39 | |||||||||
-6 | -7 | -8 | -9 | -11 | -12 | -13 | -14 | -16 | -16 | -18 | ||||||||||
J8 | 10 | 12 | 15 | 20 | 24 | 28 | 34 | 41 | 47 | 55 | 60 | |||||||||
-8 | -10 | -12 | -13 | -15 | -18 | -20 | -22 | -25 | -26 | -29 | ||||||||||
JS6 | 4 | 4.5 | 5.5 | 6.5 | 8 | 9.5 | 11 | 12.5 | 14.5 | 16 | 18 | |||||||||
-4 | -4.5 | -5.5 | -6.5 | -8 | -9.5 | -11 | -12.5 | -14.5 | -16 | -18 | ||||||||||
JS7 | 6 | 7.5 | 9 | 10.5 | 12.5 | 15 | 17.5 | 20 | 23 | 26 | 28.5 | |||||||||
-6 | -7.5 | -9 | -10.5 | -12.5 | -15 | -17.5 | -20 | -23 | -26 | -28.5 | ||||||||||
JS8 | 9 | 11 | 13.5 | 16.5 | 19.5 | 23 | 27 | 31.5 | 36 | 40.5 | 44.5 | |||||||||
-9 | -11 | -13.5 | -16.5 | -19.5 | -23 | -27 | -31.5 | -36 | -40.5 | -44.5 | ||||||||||
K6 | 2 | 2 | 2 | 2 | 3 | 4 | 4 | 4 | 5 | 5 | 7 | |||||||||
-6 | -7 | -9 | -11 | -13 | -15 | -18 | -21 | -24 | -27 | -29 | ||||||||||
케이7 | 3 | 5 | 6 | 6 | 7 | 9 | 10 | 12 | 13 | 16 | 17 | |||||||||
-9 | -10 | -12 | -15 | -18 | -21 | -25 | -28 | -33 | -36 | -40 | ||||||||||
케이8 | 5 | 6 | 8 | 10 | 12 | 14 | 16 | 20 | 22 | 25 | 28 | |||||||||
-13 | -16 | -19 | -23 | -27 | -32 | -38 | -43 | -50 | -56 | -61 | ||||||||||
엠6 | -1 | -3 | -4 | -4 | -4 | -5 | -6 | -8 | -8 | -9 | -10 | |||||||||
-9 | -12 | -15 | -17 | -20 | -24 | -28 | -33 | -37 | -41 | -46 | ||||||||||
엠7 | 0 | 0 | 0 | 0 | 0 | 0 | 0 | 0 | 0 | 0 | 0 | |||||||||
-12 | -15 | -18 | -21 | -25 | -30 | -35 | -40 | -46 | -52 | -57 | ||||||||||
M8 | 2 | 1 | 2 | 4 | 5 | 5 | 6 | 8 | 9 | 9 | 11 | |||||||||
-16 | -21 | -25 | -29 | -34 | -41 | -48 | -55 | -63 | -72 | -78 | ||||||||||
N6 | -5 | -7 | -9 | -11 | -12 | -14 | -16 | -20 | -22 | -25 | -26 | |||||||||
-13 | -16 | -20 | -24 | -28 | -33 | -38 | -45 | -51 | -57 | -62 | ||||||||||
N7 | -4 | -4 | -5 | -7 | -8 | -9 | -10 | -12 | -14 | -14 | -16 | |||||||||
-16 | -19 | -23 | -28 | -33 | -39 | -45 | -52 | -60 | -66 | -73 | ||||||||||
N8 | -2 | -3 | -3 | -3 | -3 | -4 | -4 | -4 | -5 | -5 | -5 | |||||||||
-20 | -25 | -30 | -36 | -42 | -50 | -58 | -67 | -77 | -86 | -94 | ||||||||||
P6 | -9 | -12 | -15 | -18 | -21 | -26 | -30 | -36 | -41 | -47 | -51 | |||||||||
-17 | -21 | -26 | -31 | -37 | -45 | -52 | -61 | -70 | -79 | -87 | ||||||||||
P7 | -8 | -9 | -11 | -14 | -17 | -21 | -24 | -28 | -33 | -36 | -41 | |||||||||
-20 | -24 | -29 | -35 | -42 | -51 | -59 | -68 | -79 | -88 | -98 | ||||||||||
P8 | -12 | -15 | -18 | -22 | -26 | -32 | -37 | -43 | -50 | -56 | -62 | |||||||||
-30 | -37 | -45 | -55 | -65 | -78 | -91 | -106 | -122 | -137 | -151 | ||||||||||
R6 | -12 | -16 | -20 | -24 | -29 | -35 | -37 | -44 | -47 | -56 | -58 | -61 | -68 | -71 | -75 | -85 | -89 | -97 | -103 | |
-20 | -25 | -31 | -37 | -45 | -54 | -56 | -66 | -69 | -81 | -83 | -86 | -97 | -100 | -104 | -117 | -121 | -133 | -139 | ||
R7 | -11 | -13 | -16 | -20 | -25 | -30 | -32 | -38 | -41 | -48 | -50 | -53 | -60 | -63 | -67 | -74 | -78 | -87 | -93 | |
-23 | -28 | -34 | -41 | -50 | -60 | -62 | -73 | -76 | -88 | -90 | -93 | -106 | -109 | -113 | -126 | -130 | -144 | -150 |
2.2 ISO 286 치수 허용 오차 표 – 구멍 직경 허용 오차
이 표는 다양한 구멍 직경 범위에 대한 다양한 IT 등급(공차 등급)에 따른 구멍 직경 공차를 설명합니다.
크기 범위(mm) | IT7 허용오차(mm) | IT8 허용오차(mm) | IT9 허용오차(mm) |
1 – 3 | ±0.020 | ±0.025 | ±0.030 |
3 – 6 | ±0.025 | ±0.030 | ±0.035 |
6 – 10 | ±0.030 | ±0.035 | ±0.040 |
10 – 18 | ±0.035 | ±0.040 | ±0.045 |
18 – 30 | ±0.040 | ±0.045 | ±0.050 |
30 – 50 | ±0.050 | ±0.060 | ±0.070 |
2.3 ISO 286 치수 허용 오차 표 – 샤프트 직경 허용 오차
이 표는 다양한 IT 등급에 따른 샤프트 직경 허용 오차를 보여줍니다.
크기 범위(mm) | IT7 허용오차(mm) | IT8 허용오차(mm) | IT9 허용오차(mm) |
1 – 3 | ±0.020 | ±0.025 | ±0.030 |
3 – 6 | ±0.025 | ±0.030 | ±0.035 |
6 – 10 | ±0.030 | ±0.035 | ±0.040 |
10 – 18 | ±0.035 | ±0.040 | ±0.045 |
18 – 30 | ±0.045 | ±0.050 | ±0.060 |
30 – 50 | ±0.060 | ±0.070 | ±0.080 |
2.4 ISO 286 IT 등급 허용 오차 표
이 표는 다양한 IT 등급에 대한 허용 오차 범위를 보여주며, 적절한 허용 오차 정밀도를 선택하는 데 도움이 됩니다.
IT 등급 | 허용 범위 (mm) |
IT01 | ±0.0025 |
IT2 | ±0.005 |
IT3 | ±0.010 |
IT4 | ±0.015 |
IT5 | ±0.025 |
IT6 | ±0.050 |
IT7 | ±0.080 |
IT8 | ±0.120 |
IT9 | ±0.180 |
2.5 ISO 286 허용 범위 계산 표
이 표는 다양한 허용 오차 대역(예: H7 및 H7)에 대한 구멍과 샤프트 사이의 허용 편차를 보여줍니다.
핏 타입 | 구멍 허용 오차(mm) | 샤프트 허용 오차(mm) |
H7 | ±0.025 | 0.000 |
H8 | ±0.030 | 0.000 |
h7 | ±0.025 | ±0.000 |
h8 | ±0.030 | ±0.000 |
2.6 ISO 286 직경 허용 오차 표(구멍 및 샤프트 직경)
이 표는 기계 가공에서 정밀 제어에 적용되는 다양한 크기 범위 내의 구멍 및 샤프트 직경에 대한 허용 오차를 보여줍니다.
크기 범위(mm) | 구멍 허용 오차(mm) | 샤프트 허용 오차(mm) |
3 – 6 | ±0.025 | ±0.020 |
6 – 10 | ±0.035 | ±0.030 |
10 – 18 | ±0.045 | ±0.035 |
18 – 30 | ±0.060 | ±0.045 |
30 – 50 | ±0.080 | ±0.060 |
2.7 ISO 286 허용 범위 및 적합 표
이 표에는 구멍과 샤프트 맞춤에 대한 다양한 허용 오차 범위(예: H7, h7, P7)가 나열되어 있어 맞춤 정확성을 보장하는 데 도움이 됩니다.
핏 타입 | 구멍 허용 오차(mm) | 샤프트 허용 오차(mm) |
H7 | ±0.025 | 0.000 |
H8 | ±0.030 | 0.000 |
h7 | ±0.025 | ±0.000 |
h8 | ±0.030 | ±0.000 |
P7 | ±0.030 | 0.000 |
2.8 ISO 1101: 기하학적 허용 오차
ISO 1101 표준은 펀칭 후 구멍 위치와 모양이 설계 요구 사항을 충족하는지 확인합니다. 특히 구멍 위치 정확도가 중요한 정밀 가공의 경우 더욱 그렇습니다. 제조업체는 기하학적 공차를 적절히 설정함으로써 각 구멍의 정확한 위치와 모양을 보장하여 조립 및 용접 중 오류를 방지할 수 있습니다.
ISO 1101은 기계 부품의 형상, 치수 정확도, 조립 요구 사항과 같은 기하학적 공차를 정의하는 국제 표준입니다. 제조 및 조립 공정에서 허용되는 기하학적 편차를 나타내는 기호와 방법을 제공합니다. 기하학적 공차는 일반적으로 베어링, 기어, 랙과 같이 높은 정밀도가 필요한 부품에 적용됩니다.
3.0 ISO 1101의 주요 측면: 기하학적 허용 오차
기하학적 허용오차 기호
ISO 1101은 다양한 기하학적 요구 사항을 나타내는 다양한 기호를 정의합니다. 일반적인 기하학적 허용 오차 기호는 다음과 같습니다.
- 직진성 (⎯): 지정된 범위 내에서 표면이나 윤곽이 직선을 유지하도록 보장합니다.
- 평탄도 (▭): 표면이 지정된 평면 내에 유지되도록 보장합니다.
- 원형도(O): 원형 윤곽의 둥글림이 허용 범위 내에 있는지 확인합니다.
- 원통형(◯): 축과 직경 모두에 대해 지정된 허용 오차 범위 내에 원통형 모양이 유지되도록 보장합니다.
- 수직성 (⊥): 두 표면 또는 축 사이의 관계가 수직인지 확인합니다.
- 병렬성(∥): 두 개의 표면이나 선이 평행을 유지하도록 합니다.
- 동심원성 (⌀): 두 개의 원형 피처의 축이 겹치도록 합니다.
- 위치 허용 오차(⊙): 공간의 구멍, 샤프트 또는 기타 피처에 대한 위치 허용 오차를 정의합니다.
3.1 치수 지정을 통한 기하학적 공차
기하학적 공차는 일반적으로 치수 지정과 결합되어 작업물의 정확한 모양과 조립 요구 사항을 지정합니다. 예를 들어:
- 구멍 기하 공차: 평면에서 구멍의 위치와 편차를 지정하는 데 자주 사용됩니다.
- 샤프트 기하학적 공차: 직진성, 원형도 또는 동심도가 포함될 수 있습니다.
3.2 기하학적 공차의 응용
실제로 기하학적 공차는 다른 치수 공차와 함께 사용되어 제품이 조립 및 사용 중에 올바르게 작동할 수 있도록 합니다. ISO 1101은 이러한 공차 기호를 해석하고 적용하여 제조 프로세스가 설계 사양을 충족하도록 하는 자세한 규칙을 제공합니다.
3.3 일반적인 기하학적 허용오차 표
허용오차 유형 | 상징 | 의미 | 적용범위 |
직진성 | ⎯ | 표면 또는 선이 지정된 직진도 범위 내에 있는지 확인합니다. | 모든 선형 윤곽 및 표면에 사용됨 |
평탄 | ▭ | 모든 점이 지정된 평면 내에 있는 평평한 표면을 보장합니다. | 평면 가공 부품에 사용 |
둥글림 | 영형 | 윤곽이 지정된 원형도 범위 내에 있는지 확인합니다. | 샤프트 및 구멍과 같은 원형 기능에 사용됨 |
원통형 | ◯ | 원통형 표면이 지정된 원통형 범위 내에 있는지 확인합니다. | 모든 원통형 부품에 사용 |
수직 | ⊥ | 두 표면 또는 축 사이의 수직 관계를 보장합니다. | 정밀한 조립이 필요한 부품에 사용 |
병행 | ∥ | 두 개의 표면 또는 선이 평행한지 확인합니다. | 정밀한 조립이 필요한 부품에 사용 |
4.0 ISO 2768: 치수에 대한 일반 허용 오차
ISO 2768은 선형 및 각도 치수에 대한 치수 공차를 포함하여 기계 설계의 치수에 대한 일반적인 공차 지침을 제공합니다. 이는 정밀한 공차 제어가 필요하지 않은 비중요 치수에 자주 사용됩니다. 파이프 홀 펀칭의 경우 이 표준은 주요 기능 연결에 직접 관련되지 않지만 여전히 품질 표준을 충족해야 하는 부품에 대한 전반적인 치수 정확도를 유지하는 데 도움이 됩니다.
4.1 ISO 2768 허용오차표 – 선형 치수에 대한 일반 허용오차
치수(mm) | 허용오차(mm) |
0.5 – 3 | ±0.05 |
3 – 6 | ±0.10 |
6 – 30 | ±0.15 |
30 – 120 | ±0.20 |
120 – 400 | ±0.30 |
400 – 1000 | ±0.50 |
4.2 ISO 2768 허용오차표 – 각도 치수에 대한 일반 허용오차
각도(°) | 허용오차(°) |
0 – 10 | ±1.0 |
10 – 30 | ±1.5 |
30 – 90 | ±2.0 |
90 – 180 | ±2.5 |
이러한 허용 오차는 치수 정밀도 측면에서 그다지 중요하지 않더라도 부품을 올바르게 조립할 수 있도록 보장하기 위해 적용됩니다.
5.0 구멍 위치 및 기타 특별 고려 사항
치수 및 기하학적 공차 외에도 구멍 위치 제어는 파이프 구멍 펀칭의 또 다른 중요한 요소입니다. 파이프의 전체 구조에 대한 구멍의 위치는 설계의 지정된 위치 공차를 충족해야 합니다. ISO 1101은 구멍에 대한 위치 공차를 정의하는 방법을 지정하여 구멍이 파이프에 대해 올바른 위치에 펀칭되도록 합니다.
위치 허용 오차(ISO 1101): 위치 허용 오차는 구멍 위치에 대한 허용 가능한 편차를 정의합니다. 이는 일반적으로 참조점이나 데이텀으로 정의되며 파이프를 용접하거나 다른 구성 요소와 장착할 때와 같이 구멍이 다른 부분과 올바르게 정렬되도록 하는 데 중요합니다.
6.0 연강 펀칭을 위한 클리어런스 가이드
연강 펀칭을 위한 클리어런스 가이드 | |||||||||||||||||||
연강의 두께 | |||||||||||||||||||
펀치 크기 |
1/8 | 1/4 | 3/8 | 1/2 | 5/8 | 3/4 | 7/8 | 1″ | |||||||||||
3/16 | 13/64 | ||||||||||||||||||
1/4 | 17/64 | ||||||||||||||||||
5/16 | 21/64 | 11/32 | |||||||||||||||||
3/8 | 25/64 | 13/32 | 13/32 | ||||||||||||||||
7/16 | 29/64 | 15/32 | 15/32 | ||||||||||||||||
1/2 | 33/64 | 17/32 | 17/32 | 9/16 | |||||||||||||||
9/16 | 37/64 | 19/32 | 19/32 | 5/8 | |||||||||||||||
5/8 | 41/64 | 21/32 | 21/32 | 11/16 | 11/16 | ||||||||||||||
11/16 | 45/64 | 23/32 | 23/32 | 3/4 | 3/4 | ||||||||||||||
3/4 | 49/64 | 25/32 | 25/32 | 13/16 | 13/16 | 27/32 | |||||||||||||
13/16 | 53/64 | 27/32 | 27/32 | 7/8 | 7/8 | 29/32 | |||||||||||||
7/8 | 57/64 | 29/32 | 29/32 | 15/16 | 15/16 | 31/32 | 31/32 | ||||||||||||
15/16 | 61/64 | 31/32 | 31/32 | 1 | 1 | 1-1/32 | 1-1/32 | ||||||||||||
1 | 1-1/64 | 1-1/32 | 1-1/32 | 1-1/16 | 1-1/16 | 1-3/32 | 1-3/32 | 1-1/8 | |||||||||||
1-1/16 | 1-5/64 | 1-3/32 | 1-3/32 | 1-1/8 | 1-1/8 | 1-5/32 | 1-5/32 | 1-3/16 | |||||||||||
1-1/8 | 1-9/64 | 1-5/32 | 1-5/32 | 1-3/16 | 1-3/16 | 1-7/32 | 1-7/32 | 1-1/4 | |||||||||||
1-3/16 | 1-13/64 | 1-7/32 | 1-7/32 | 1-1/4 | 1-1/4 | 1-9/32 | 1-9/32 | 1-5/16 | |||||||||||
1-1/4 | 1-17/64 | 1-9/32 | 1-9/32 | 1-5/16 | 1-5/16 | 1-11/32 | 1-11/32 | 1-3/8 | |||||||||||
1-5/16 | 1-21/64 | 1-11/32 | 1-11/32 | 1-3/8 | 1-3/8 | 1-13/32 | 1-13/32 | 1-7/16 | |||||||||||
1-3/8 | 1-25/64 | 1-13/32 | 1-13/32 | 1-7/16 | 1-7/16 | 1-15/32 | 1-15/32 | 1-1/2 | |||||||||||
1-7/16 | 1-29/64 | 1-15/32 | 1-15/32 | 1-1/2 | 1-1/2 | 1-17/32 | 1-17/32 | 1-9/16 | |||||||||||
1-1/2 | 1-33/64 | 1-17/32 | 1-17/32 | 1-9/16 | 1-9/16 | 1-19/32 | 1-19/32 | 1-5/8 |
7.0 연강 펀칭에 권장되는 톤수
연강 펀칭에 권장되는 톤수 | |||||||||||||||||||||
두께 연강 |
펀치 크기 | ||||||||||||||||||||
3/16 | 1/4 | 5/16 | 3/8 | 7/16 | 1/2 | 9/16 | 5/8 | 11/16 | 3/4 | 13/16 | 7/8 | 15/16 | 1″ | 1-1/8 | 1-1/4 | ||||||
3/16 1/4 |
.187 | 3 | 4 | 5 | 6 | 7 | 7 | 8 | 9 | 10 | 11 | 12 | 13 | 14 | 15 | 17 | 19 | ||||
.250 | 5 | 6 | 8 | 9 | 10 | 11 | 12 | 14 | 15 | 16 | 18 | 19 | 20 | 22 | 25 | ||||||
3/8 | .375 | 11 | 13 | 15 | 17 | 19 | 21 | 22 | 24 | 26 | 28 | 30 | 34 | 38 | |||||||
1/2 | .500 | 20 | 22 | 25 | 28 | 30 | 32 | 35 | 38 | 40 | 45 | 50 | |||||||||
5/8 | .625 | 31 | 34 | 38 | 41 | 44 | 47 | 50 | 56 | 62 | |||||||||||
3/4 | .750 | 45 | 49 | 52 | 56 | 60 | 68 | 75 | |||||||||||||
7/8 | .875 | 61 | 66 | 70 | 79 | 88 | |||||||||||||||
1 | |||||||||||||||||||||
1.000 | 80 | 90 |
7.1 결론
ISO 공차 표준은 파이프 홀 펀칭 및 기타 가공 작업이 정확하게 수행되도록 하는 데 중요한 역할을 합니다. 이러한 국제적으로 인정된 표준을 따르면 제조업체는 펀칭된 홀이 치수 및 기하학적 요구 사항을 모두 충족하는지 확인할 수 있어 고품질의 신뢰할 수 있는 제품을 생산할 수 있습니다.
7.2 부록: 파이프 홀 펀칭에서 일반적으로 사용되는 허용 오차
유형 | 허용오차(mm) | 노트 |
구멍 직경 | ±0.10 – ±0.20 | 파이프 크기 및 재질에 따라 다름 |
홀 위치 | ±0.10 – ±0.20 | 기준점 또는 데이텀을 기준으로 |
수직 | ±0.05 – ±0.10 | 구멍이 파이프와 수직인지 확인합니다. |
구멍의 둥글림 | ±0.05 – ±0.10 | 구멍이 원형을 유지하도록 합니다. |
구멍의 평탄도 | ±0.05 – ±0.10 | 펀칭된 구멍 표면이 평평한 상태를 유지하도록 합니다. |
이러한 표를 참조하고 적절한 표준을 따르면, 제조업체는 펀칭 공정이 정밀성을 유지하고 최종 제품에서 파이프가 올바르게 맞춰지는지 확인할 수 있습니다.
https://www.dimensionalconsulting.com/tolerance-of-position.html
https://slideplayer.com/slide/15857807/
https://www.clevelandsteeltool.com/