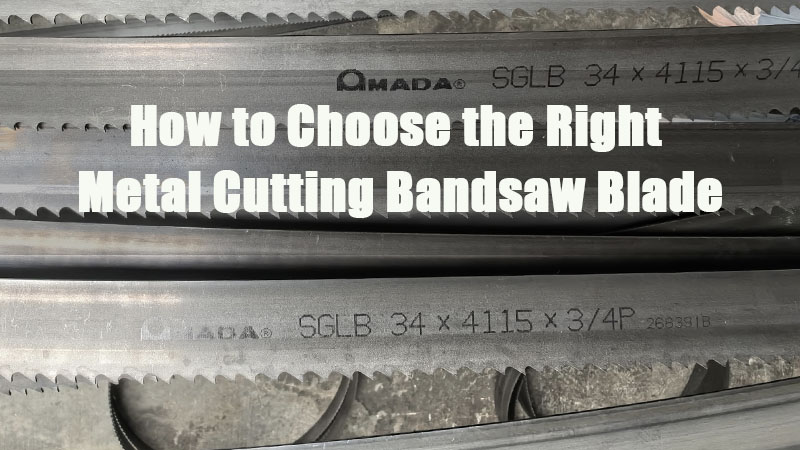
1.0 Blade Material Selection
1.1 Carbon Steel Blades
Carbon steel blades are basic and affordable, ideal for cutting softer metals such as aluminum, copper, brass, bronze, and other nonferrous metals. Suitable for workshops with occasional bandsaw use.
1.2 Bi-Metal Blades
Bi-metal blades are the industry standard for versatile cutting tasks. Featuring a high-speed steel (HSS) cutting edge welded to a flexible alloy steel back, they combine hardness with flexibility. They are durable and suitable for cutting a wide range of materials, including stainless steel.
1.3 Carbide Tipped Blades
Carbide tipped blades are best for cutting hard or abrasive materials, including hardened steels and exotic alloys. Tungsten carbide teeth brazed onto a flexible steel band provide exceptional durability, especially for high-volume production.
2.0 Tooth Pitch (TPI) and Its Importance
2.1 Why TPI Matters
TPI (teeth per inch) affects cutting speed, surface finish, and vibration. Higher TPI delivers a finer cut but slower feed rate. Lower TPI allows faster cutting but results in a rougher surface.
2.2 TPI and Material Thickness
TPI is inversely related to material thickness. Thin materials require a high TPI to reduce vibration and tooth chipping. Thick materials need a lower TPI for aggressive cutting and efficient chip removal.
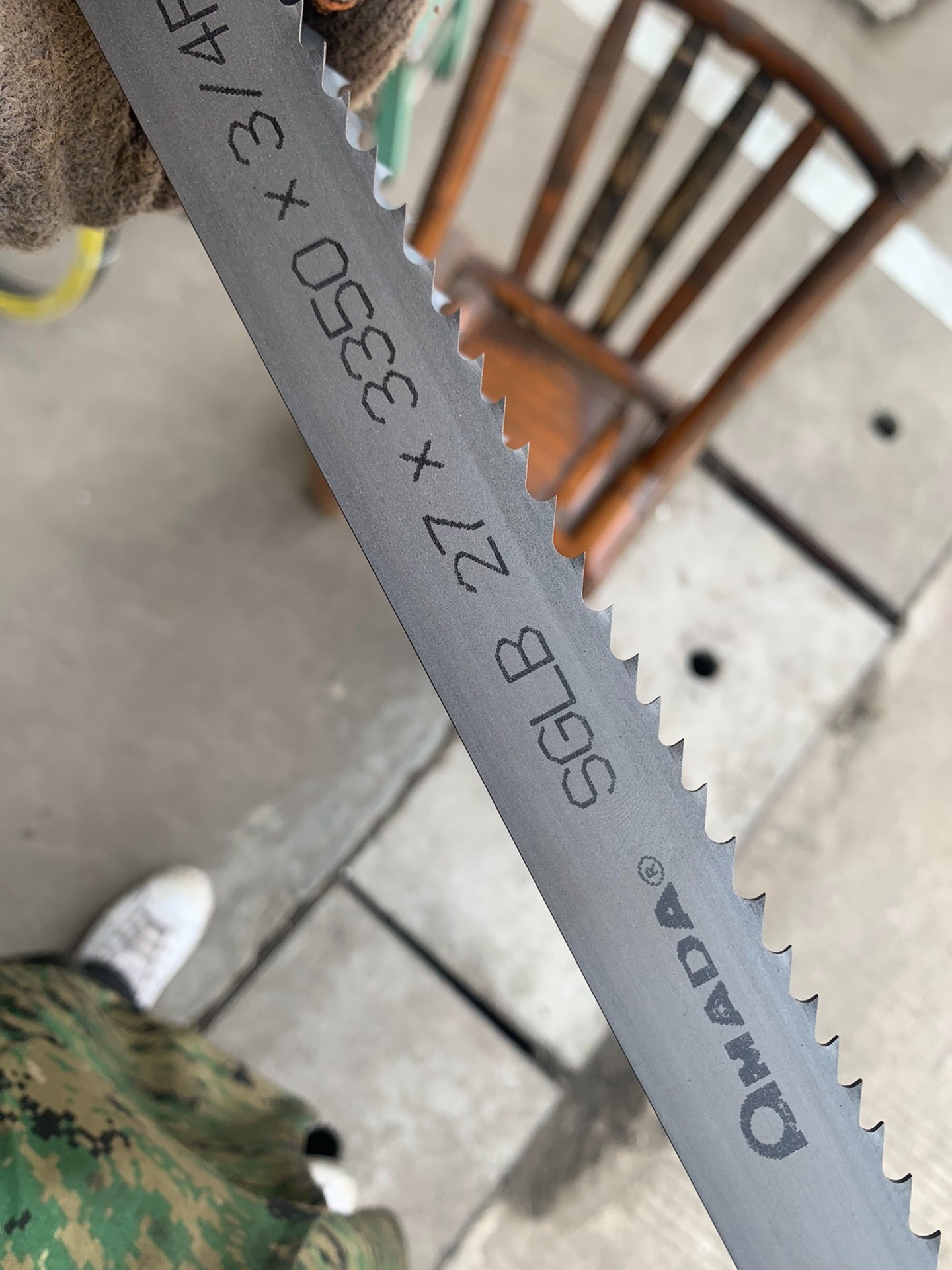
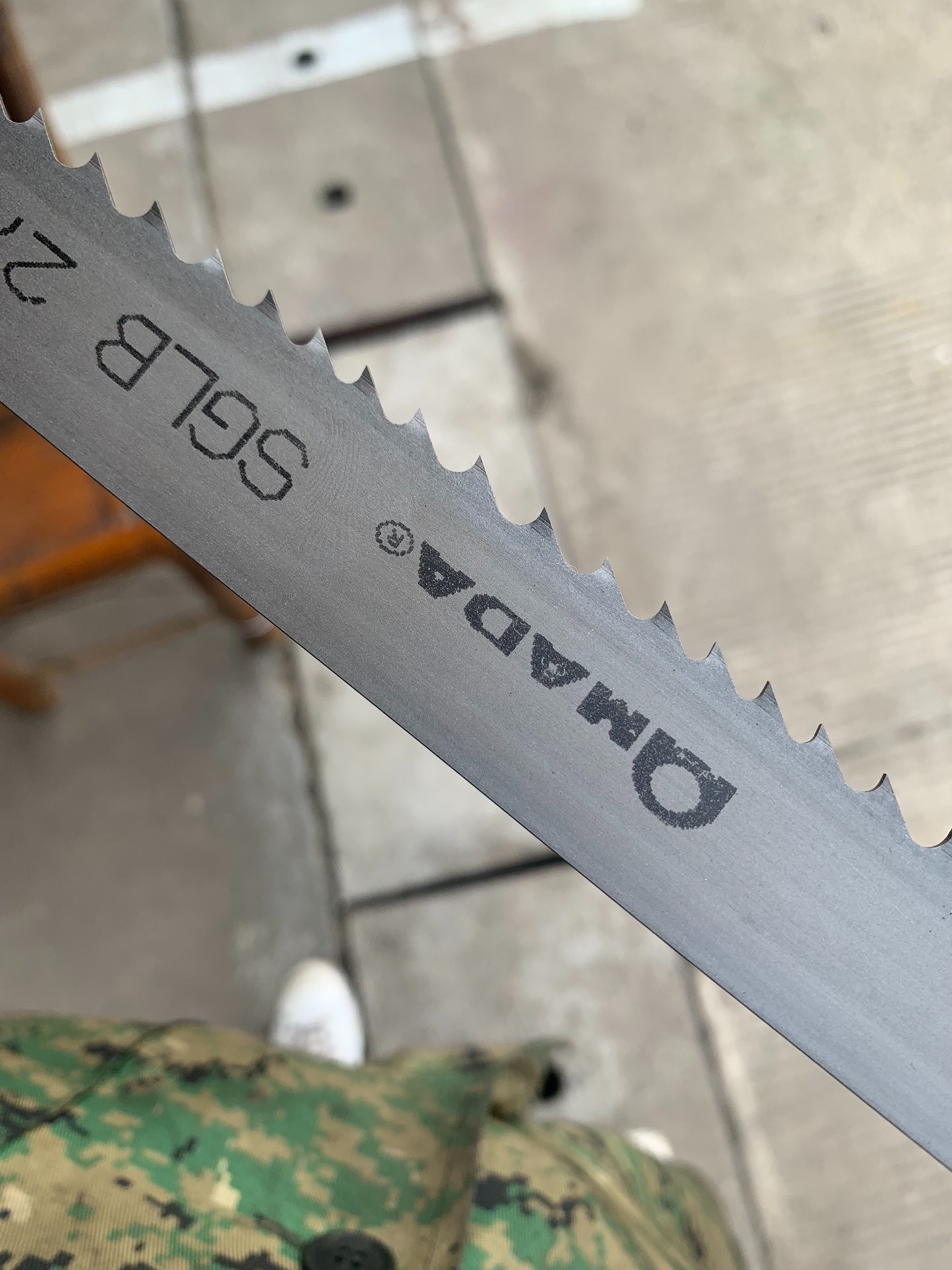
2.3 Recommended TPI Chart (Solid Materials)
Material Thickness | Recommended TPI |
< 3 mm | 24 – 32 TPI |
3 – 6 mm | 18 – 24 TPI |
6 – 12 mm | 14 – 18 TPI |
12 – 25 mm | 10 – 14 TPI |
> 25 mm | 6 – 10 TPI |
2.4 TPI for Tubes and Profiles
For tubes and profiles, both wall thickness and maximum diameter are critical. For thin-wall tubes and profiles, prioritize wall thickness. For thicker materials, diameter becomes more influential.
Approximate TPI for Profiles (Wall Thickness up to 100 mm)
Wall Thickness (mm) | Ø 25 mm | Ø 50 mm | Ø 100 mm | Ø 200 mm | Ø 500 mm |
2 | 14 | 14 | 10-14 | 10-14 | 8-12 |
5 | 14 | 10-14 | 6-10 | 5-8 | 4-6 |
10 | 6-10 | 6-10 | 5-8 | 4-6 | 3-4 |
20 | 4-6 | 4-6 | 3-4 | 3-4 | 2-3 |
50 | 2-3 | 2-3 | 2-3 | 2-3 | 1.4-2 |
100 | 1.4-2 | 1.4-2 | 1-1.3 | 1-1.3 | 0.75-1.25 |
With small diameters, recommended TPI resembles solid materials to avoid vibration and tooth damage when cutting the thin-walled edge. For larger profiles, material strength reduces this issue, allowing fewer teeth for smoother cuts.
2.5 Recommended TPI by Blade Material
Below are recommended TPI values for carbon steel, alloy steel, and high-speed steel blades based on material type and thickness. These values serve as a quick guide for selecting the right blade.
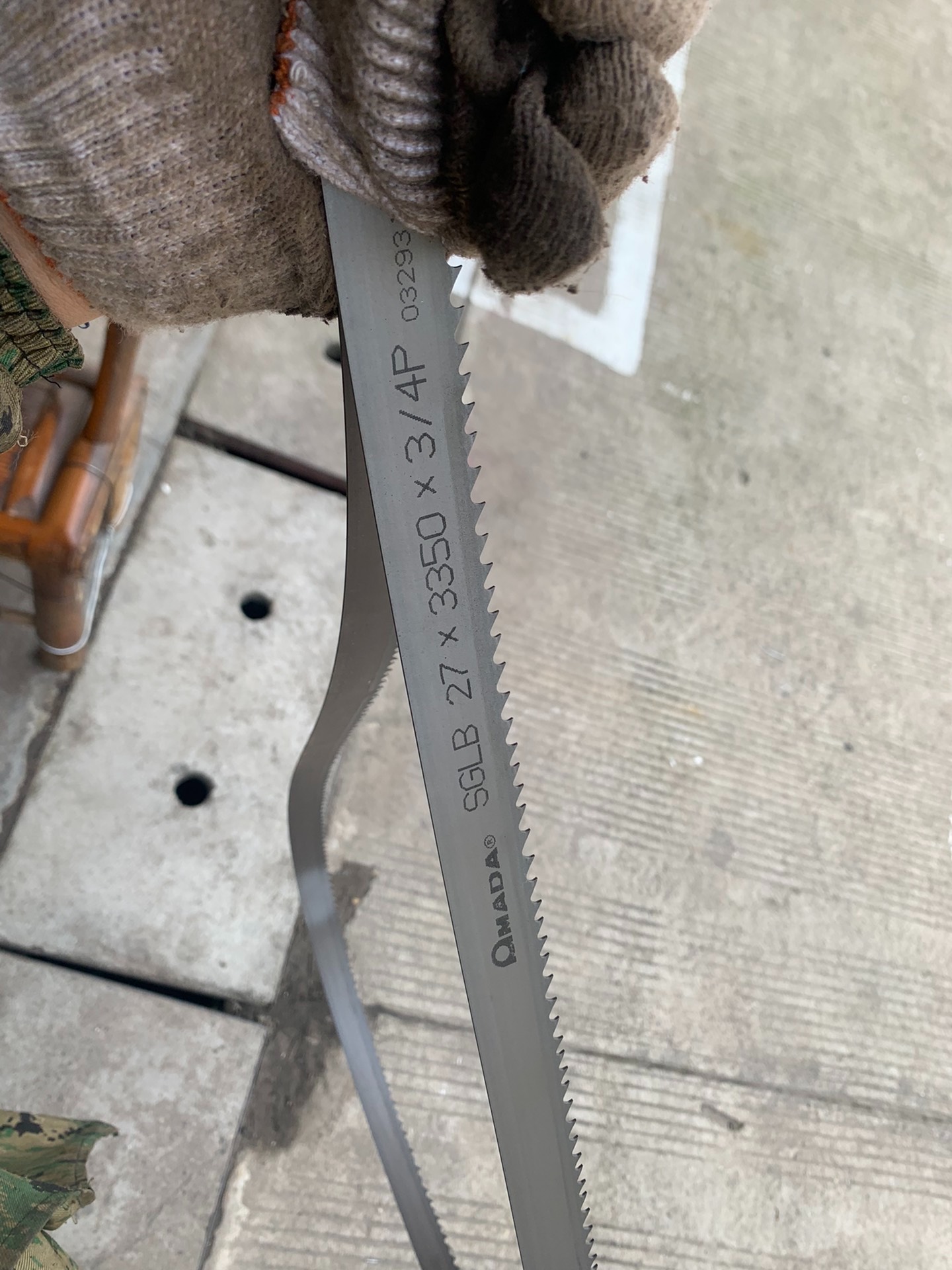
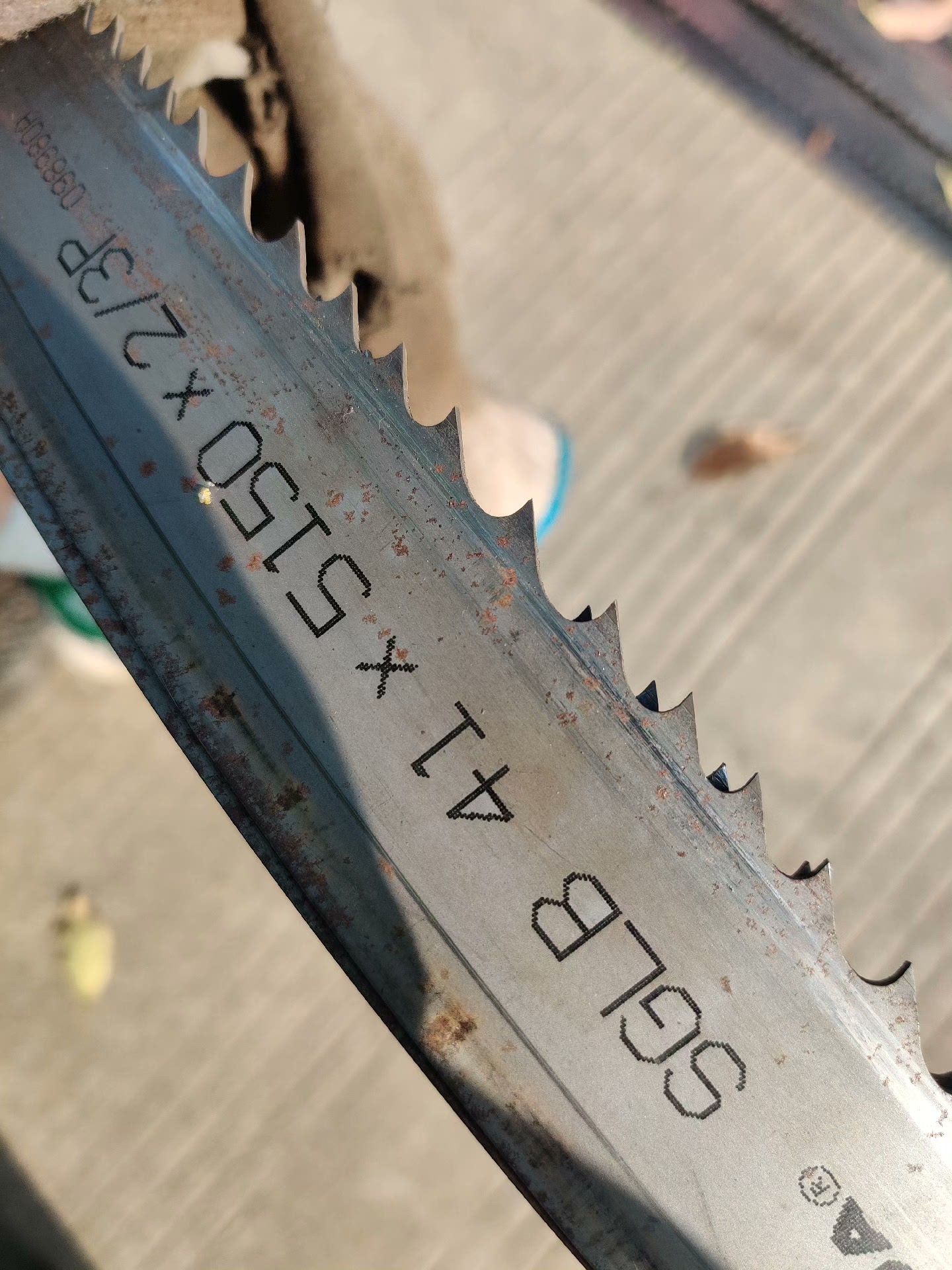
2.6 Carbon Steel Blades
Application | Thickness of Metal | Blade TPI |
For aluminum, brass, copper, soft bronze, magnesium, wood, mild steel, tougher steels (slow speed) | 1/2″ to 3-3/8″ | 6 |
Same as above | 3/8″ to 1″ | 8 |
For aluminum, angle iron, cast iron, bronze, brass, copper, galvanized pipe, mild steel, tougher steels (slow speed) | 3/16″ to 3/4″ | 10 |
Same as above, plus electric cables | 5/32″ to 1/2″ | 14 |
For thin-wall tubing and thin sections | 1/8″ to 1/4″ | 18 |
For extra thin materials | 3/32″ to 1/8″ | 18 |
2.7 Alloy Steel Blades
Application | Thickness of Metal | Blade TPI |
For aluminum, cast iron, bronze, brass, copper, galvanized pipe, mild steel, tougher steels (chrome, tungsten) | 3/16″ to 1″ | 10 |
Same as above, including electric cables | 5/32″ to 3/4″ | 14 |
For thin-wall tubing and soft materials | 1/8″ to 1/2″ | 18 |
For extra thin materials | 3/32″ to 1/8″ | 24 |
2.8 High-Speed Steel (HSS) Blades
Application | Thickness of Metal | Blade TPI |
For aluminum, angle iron, bronze, brass, copper, galvanized pipe, mild steel, tougher steels (stainless, chrome, tungsten) | 7/32″ to 7/8″ | 10 |
Same as above | 3/16″ to 5/8″ | 14 |
For thinner sections | 5/32″ to 3/8″ | 18 |
Tip: For difficult-to-cut materials like stainless and tungsten steels, HSS blades are recommended at slower speeds with proper lubrication.
3.0 Tooth Configuration
3.1 Regular-Tooth Blades
- Straight-faced teeth
- Even spacing with deep gullets
- 0° rake angle
- Suitable for general-purpose sawing and contour cutting of thin sheet metals.
3.2 Hook-Tooth Blades
- Large, widely spaced teeth
- Deep gullets
- Positive 10° rake angle
- Ideal for fast, rough cuts on thick or hard metals.
3.3 Skip-Tooth Blades
- Widely spaced teeth with shallow gullets
- 0° rake angle with 90° tooth form
- Suitable for nonferrous metals and soft materials, reducing clogging.
4.0 Tooth Set Patterns
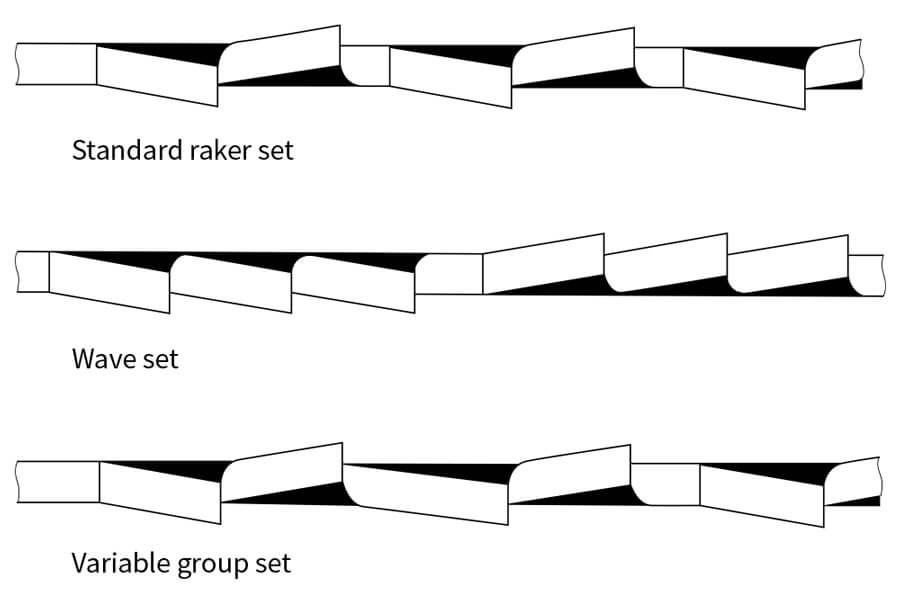
4.1 Standard Tooth Set
- Alternating left and right offsets
- For general-purpose cutting with moderate kerf width.
4.2 Variable (Wavy) Set
- Gradual changes in left and right offsets
- Reduces chatter, ideal for thin materials and hollow sections.
4.3 Straight (Raker) Set
- Minimal or no offset
- Produces fine, narrow kerfs but increases binding risk.
5.0 Additional Considerations
5.1 Kerf Width and Cutting Stress
Carbide-tipped blades create a wider kerf, increasing stress on the workpiece and possibly deforming thin materials. Bi-metal and carbon steel blades produce narrower kerfs, better for thin or delicate materials.
This is particularly important for manual band saw machines, where operator feed rate may vary, increasing the risk of blade wear.
5.2 Vibration Control
Avoid tooth gaps wider than the material thickness to minimize vibration and wear. Ensure multiple teeth are engaged during cutting.
5.3 Cooling and Lubrication
Bi-metal and carbide-tipped blades are sensitive to overheating. Apply proper cooling to extend blade life and improve cutting efficiency.
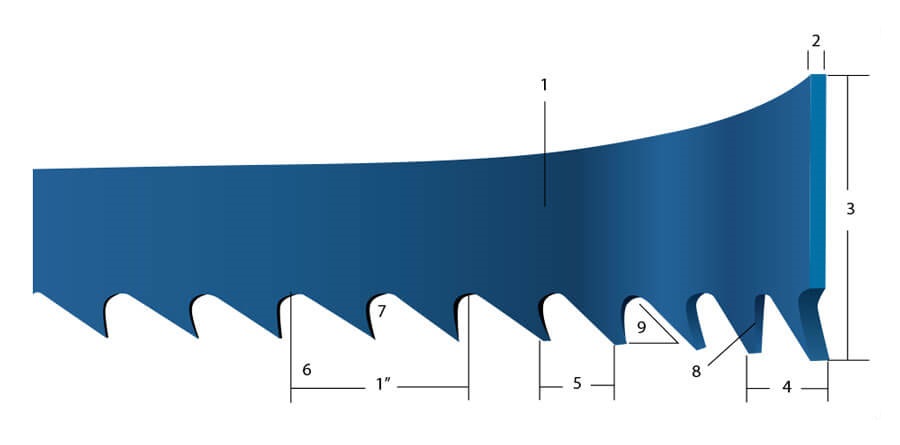
6.0 Bandsaw Blade Terminology
- Back: The non-cutting edge of the blade
- Width/Height: Distance from tooth tip to the back
- Set: The amount teeth are offset from the blade centerline
- Tooth Pitch: Distance between tooth tips (used to calculate TPI)
- Gullet: The curved area between teeth for chip removal
- Tooth Face: The front surface of the tooth
- Rake Angle: The angle of the tooth face relative to a perpendicular line to the blade direction
7.0 Summary
For optimal performance, select your bandsaw blade based on:
- Material type (solid, tube, or profile)
- Desired surface finish
- Cutting speed and efficiency
- Blade material and tooth configuration
- Correct TPI considering material thickness and shape
Always consult blade manufacturer recommendations or catalogs to select the most suitable blade for your cutting applications.
Reference: https://rongfu.com/news/comparing-carbon-steel-bimetal-carbide-tipped-metal-cutting-bandsaw-blades/
https://www.nortonabrasives.com/en-gb/resources/expertise/ultimate-saw-blade-teeth-guide