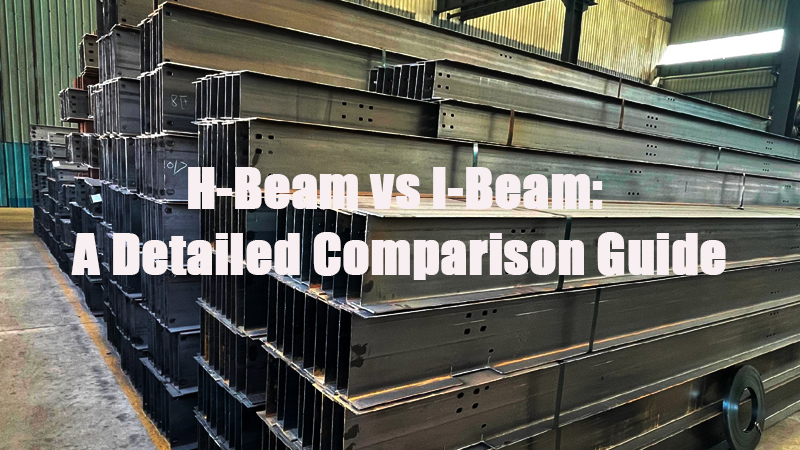
- 1.0Definitions and Design of H-Beams and I-Beams
- 2.0Comparison of Manufacturing Processes Between H-Beams and I-Beams
- 3.0Impact of Manufacturing Processes on Cost
- 4.0Impact of Manufacturing Processes on Delivery Time
- 5.0Impact of Manufacturing Processes on Product Quality
- 6.0Comparison of Material Selection and Structural Strength Between H-Beams and I-Beams
- 7.0Comparison of Strength and Load Capacity Between H-Beams and I-Beams
- 8.0Application Scenarios of H-Beams and I-Beams in Construction Design
- 9.0Lifespan and Maintenance of H-Beams and I-Beams
- 10.0Safety and Compliance of H-Beams and I-Beams
I-beams are structural components with an I-shaped cross-section (similar to a serif capital letter “I”) or an H-shaped one. Other related technical terms include H-beams, I-sections, Universal Columns (UC), W-beams (representing “wide flange”), Universal Beams (UB), Rolled Steel Joists (RSJ), or Double T-beams. They are made of steel and can be used for various construction purposes.
Below, we compare the differences between H-beam and I-beam from the perspective of cross-section.Applications of H-Beams
H-beams are commonly used in projects requiring large spans and high load-bearing capacities, such as bridges and high-rise buildings.
0.1Applications of I-Beams
I-beams are known for being lightweight and economical, making them suitable for residential buildings and light industrial structures.
This article will explore in detail the design, manufacturing processes, application scenarios, and performance of H-beams and I-beams under different conditions.
1.0Definitions and Design of H-Beams and I-Beams
1.1H-Beams
H-beams have an H-shaped cross-section, characterized by wide, flat flanges and a thick web. The large flanges allow for load distribution over a wider area, enhancing load-bearing capacity and structural stability.
The design of H-beams enables them to distribute loads evenly in both vertical and horizontal directions, making them particularly suitable for large buildings, bridges, and industrial projects that require heavy load support.
The thickness of both the web and the flanges provides stronger resistance to bending and shearing forces, making H-beams ideal for high-strength projects.
1.2I-Beams
I-beams have an I-shaped cross-section, with narrower and thicker flanges, mainly designed to bear vertical loads. Their design allows them to effectively resist vertical pressure, especially in floor or roof support structures.
I-beams are lightweight and economical, with a proportionate flange-to-web ratio that makes them widely used in lightweight buildings and medium-sized structures. Compared to H-beams, I-beams have weaker lateral support capacity and are suitable for projects with lower load requirements.
2.0Comparison of Manufacturing Processes Between H-Beams and I-Beams
2.1H-Beams
- Rolling Process:
- Manufactured through multiple stages of cold and hot rolling.
- H-beam rolling machines can precisely control their dimensions and shape.
- H-beam polishing machines remove surface imperfections or enhance smoothness.
- Applicable Situations:
- Suitable for high-precision construction and heavy industrial projects.
- Commonly used in bridges, large building structures, and high-stress facilities.
2.2I-Beams
- Hot Rolling Process:
- Primarily produced on a large scale through hot rolling.
- During production, any bending or twisting in I-beams is corrected to ensure flatness and straightness.
- Punching machines are used to quickly punch holes in the flanges or web of I-beams, facilitating the assembly and connection of steel structures.
- Applicable Situations:
- Commonly used in conventional construction projects such as steel frame buildings and support beams.
3.0Impact of Manufacturing Processes on Cost
Overall, the manufacturing cost of H-beams is higher than that of I-beams.
- H-Beams: Due to the complex rolling processes and high precision requirements, the equipment and production processes are more extensive, leading to higher manufacturing costs.
- I-Beams: The simpler process, primarily large-scale hot rolling production, results in lower manufacturing costs.
4.0Impact of Manufacturing Processes on Delivery Time
I-beams of standard sizes have shorter delivery times than H-beams.
- H-Beams: The complexity of the process results in longer production times and extended delivery schedules.
- I-Beams: The simpler production process allows for faster mass production, resulting in shorter delivery times.
5.0Impact of Manufacturing Processes on Product Quality
- H-Beams: Higher strength and durability, suitable for applications requiring high structural integrity.
- I-Beams: The production is relatively simpler, leading to lower geometric precision and consistency, but still meets the needs of general construction applications.
6.0Comparison of Material Selection and Structural Strength Between H-Beams and I-Beams
6.1H-Beams
- Material Thickness: H-beams are typically made from thicker steel plates, suitable for heavy construction and high-strength engineering, offering higher load-bearing capacity and compressive strength.
- Flange Design: The wide and flat flanges of H-beams allow for load distribution over a larger area, providing higher bending resistance, making them ideal for vertical and horizontal load-bearing.
- Bending Performance: The design of H-beams provides stronger bending rigidity, making them suitable for structures requiring resistance to large-span loads, such as large bridges and factories.
6.2I-Beams
- Material Thickness: I-beams are usually made from thinner steel plates, suitable for lightweight designs, with lower material usage and relatively lower costs.
- Flange Design: The narrow flanges of I-beams are designed to minimize material usage, suitable for bearing vertical pressure but with weaker lateral bending resistance.
- Bending Performance: I-beams perform well in vertical load-bearing, making them suitable for short-span structures like lightweight buildings, but they are less suitable for high-strength lateral loads or large-span projects.
7.0Comparison of Strength and Load Capacity Between H-Beams and I-Beams
- H-Beams: They have strong lateral and vertical load-bearing capacities. Their wide flange design allows them to handle high loads in both directions, with superior bending and compressive performance, making them suitable for large buildings, bridges, and high-rise structures.
- I-Beams: Mainly suitable for projects that bear vertical pressure, such as the framework of lightweight buildings. Their lateral pressure resistance is weaker, but their lightweight design makes them ideal for projects requiring reduced structural weight.
8.0Application Scenarios of H-Beams and I-Beams in Construction Design
8.1Applications of H-Beams
- Large Buildings: Often used in high-rise buildings and large industrial plants, especially in structures that need to bear multi-directional stresses.
- Bridge Engineering: H-beams are widely used in bridge construction, suitable for large spans that bear both lateral and vertical stresses.
- Heavy Industrial Structures: Their high strength and durability make them ideal for supporting heavy equipment structures.
8.2Applications of I-Beams
- Lightweight Buildings: I-beams are suitable for lightweight structures such as residential buildings, warehouses, and shops.
- Short-Span Structures: Due to their strong vertical load-bearing capacity and low cost, they are commonly used in short-span structures, such as floor support beams and lightweight steel-frame factories.
- Weight Reduction Projects: I-beams perform well in projects that require reducing structural weight, such as simple buildings or modular construction.
9.0Lifespan and Maintenance of H-Beams and I-Beams
9.1H-Beams
Due to the thicker flange and web design, H-beams exhibit strong durability in heavy-load projects, with a long service life, making them particularly suitable for high-strength construction environments, and they require low maintenance costs.
9.2I-Beams
I-beams have sufficient service life in lightweight projects but may require more maintenance in large-span or high-stress environments. Their lifespan is relatively shorter, and maintenance costs may be higher.
10.0Safety and Compliance of H-Beams and I-Beams
10.1Safety of H-Beams
H-beams have high structural stability, with strong resistance to bending and shearing, making them perform excellently in seismic and wind-resistant designs, suitable for earthquake-prone regions and high-rise buildings.
10.2Safety of I-Beams
I-beams are suitable for lightweight structures, but in large-span or high-stress projects, additional support or reinforcement is usually required to ensure safety.
10.3Building Codes and Standards
Both the American Institute of Steel Construction (AISC) and international standards (ISO) have clear regulations for the use of H-beams and I-beams. Both must meet specific strength and performance requirements to ensure safety and compliance in construction engineering.