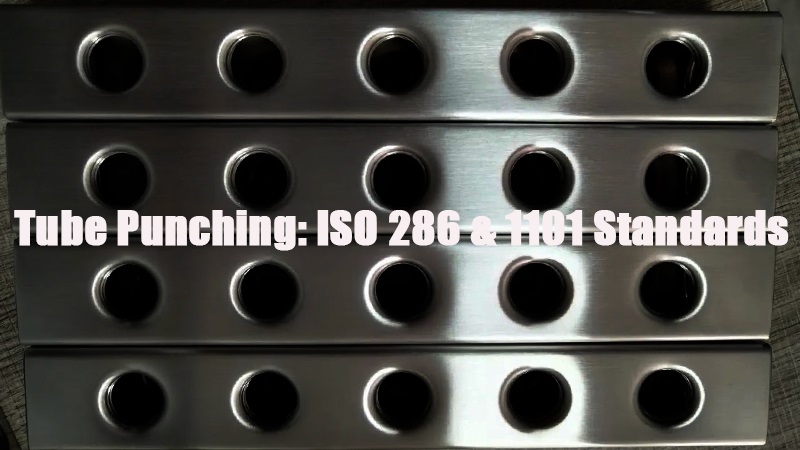
- 1.0 Grundvoraussetzungen für die Rohrlochstanzverarbeitung
- 2.0 Anwendung von ISO-Normen beim Rohrlochstanzen
- 2.1 ISO 286: Normen für Maßtoleranzen
- 2.2 ISO 286 Maßtoleranztabelle – Lochdurchmessertoleranz
- 2.3 ISO 286 Maßtoleranztabelle – Wellendurchmessertoleranz
- 2.4 ISO 286 IT-Grade-Toleranztabelle
- 2.5 ISO 286 Toleranzband-Berechnungstabelle
- 2.6 ISO 286 Durchmessertoleranztabelle (Loch- und Wellendurchmesser)
- 2.7 ISO 286 Toleranzband und Passungstabelle
- 2.8 ISO 1101: Geometrische Toleranzen
- 3.0 Kernaspekte der ISO 1101: Geometrische Toleranzen
- 4.0 ISO 2768: Allgemeine Toleranzen für Maße
- 5.0 Lochpositionierung und andere besondere Überlegungen
- 6.0 Abstandsleitfaden zum Stanzen von Weichstahl
- 7.0 Empfohlene Tonnage zum Stanzen von Weichstahl
Das Lochstanzen von Rohren ist eine wichtige Verarbeitungstechnologie, die in Branchen wie dem Maschinenbau, dem Baugewerbe und der Automobilindustrie weit verbreitet ist. Beim Lochstanzen von Rohren ist die Genauigkeit von Lochdurchmesser, Lochposition und Lochform entscheidend, insbesondere bei Rohren unterschiedlicher Materialien und Spezifikationen.
ISO-Normen bieten detaillierte Toleranzangaben und helfen Herstellern, eine hochpräzise Verarbeitung zu erreichen und sicherzustellen, dass jedes Loch die Konstruktionsanforderungen erfüllt, egal ob es sich um Vierkant- oder Rundrohre handelt.
1.0 Grundvoraussetzungen für die Rohrlochstanzverarbeitung
Das Stanzen von Rohrlöchern erfolgt üblicherweise mit einer Rohrstanzmaschine. Die Genauigkeit der Lochform und -position wirkt sich direkt auf die Anpassungsfähigkeit und Montageeffizienz des Rohrs in nachfolgenden Produktionsschritten aus. Daher ist die Kontrolle der Verarbeitungsgenauigkeit entscheidend für die Verbesserung der Produktqualität.
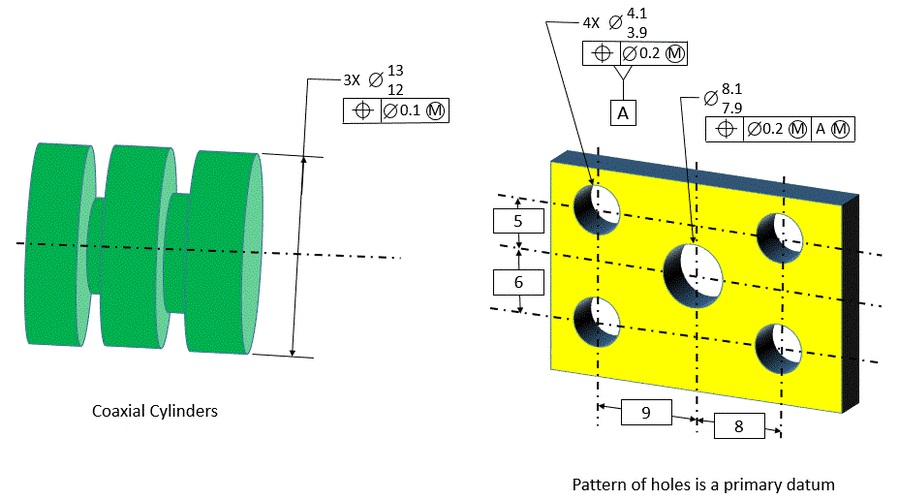
2.0 Anwendung von ISO-Normen beim Rohrlochstanzen
2.1 ISO 286: Normen für Maßtoleranzen
ISO 286 enthält Spezifikationen für Maßtoleranzen beim Stanzen von Rohrlöchern, für den Durchmesser von Abdecklöchern, den Rohrdurchmesser und andere Maßtoleranzen.
Durch die Einhaltung der Norm ISO 286 beim Lochstanzen von Rohren wird sichergestellt, dass das gestanzte Rohr den Konstruktionsanforderungen entspricht und Nacharbeiten oder nicht konforme Produkte aufgrund von Toleranzproblemen minimiert werden.
ISO-Toleranzen für Bohrungen (ISO 286-2) | ||||||||||||||||||||
Nennlochgrößen (mm) | ||||||||||||||||||||
über | 3 | 6 | 10 | 18 | 30 | 40 | 50 | 65 | 80 | 100 | 120 | 140 | 160 | 180 | 200 | 225 | 250 | 280 | 315 | 355 |
inkl. | 6 | 10 | 18 | 30 | 40 | 50 | 65 | 80 | 100 | 120 | 140 | 160 | 180 | 200 | 225 | 250 | 280 | 315 | 355 | 400 |
Mikrometer | ||||||||||||||||||||
E6 | 28 | 34 | 43 | 53 | 66 | 79 | 94 | 110 | 129 | 142 | 161 | |||||||||
20 | 25 | 32 | 40 | 50 | 60 | 72 | 85 | 100 | 110 | 125 | ||||||||||
E7 | 32 | 40 | 50 | 61 | 75 | 90 | 107 | 125 | 146 | 162 | 185 | |||||||||
20 | 25 | 32 | 40 | 50 | 60 | 72 | 85 | 100 | 110 | 125 | ||||||||||
E11 | 95 | 115 | 142 | 170 | 210 | 250 | 292 | 335 | 390 | 430 | 485 | |||||||||
20 | 25 | 32 | 40 | 50 | 60 | 72 | 85 | 100 | 110 | 125 | ||||||||||
E12 | 140 | 175 | 212 | 250 | 300 | 360 | 422 | 485 | 560 | 630 | 695 | |||||||||
20 | 25 | 32 | 40 | 50 | 60 | 72 | 85 | 100 | 110 | 125 | ||||||||||
E13 | 200 | 245 | 302 | 370 | 440 | 520 | 612 | 715 | 820 | 920 | +1 015 | |||||||||
20 | 25 | 32 | 40 | 50 | 60 | 72 | 85 | 100 | 110 | 125 | ||||||||||
F6 | 18 | 22 | 27 | 33 | 41 | 49 | 58 | 68 | 79 | 88 | 98 | |||||||||
10 | 13 | 16 | 20 | 2 | 30 | 36 | 43 | 50 | 56 | 62 | ||||||||||
F7 | 22 | 28 | 34 | 41 | 50 | 60 | 71 | 83 | 96 | 108 | 119 | |||||||||
10 | 13 | 16 | 20 | 25 | 30 | 36 | 43 | 50 | 56 | 62 | ||||||||||
F8 | 28 | 35 | 43 | 53 | 64 | 76 | 90 | 106 | 122 | 137 | 151 | |||||||||
10 | 13 | 16 | 20 | 25 | 30 | 36 | 43 | 50 | 56 | 62 | ||||||||||
G6 | 12 | 14 | 17 | 20 | 25 | 29 | 34 | 39 | 44 | 49 | 54 | |||||||||
4 | 5 | 6 | 7 | 9 | 10 | 12 | 14 | 15 | 17 | 18 | ||||||||||
G7 | 16 | 20 | 24 | 28 | 34 | 40 | 47 | 54 | 61 | 69 | 75 | |||||||||
4 | 5 | 6 | 7 | 9 | 10 | 12 | 14 | 15 | 17 | 18 | ||||||||||
G8 | 22 | 27 | 33 | 40 | 48 | 56 | 66 | 77 | 87 | 98 | 107 | |||||||||
4 | 5 | 6 | 7 | 9 | 10 | 12 | 14 | 15 | 17 | 18 | ||||||||||
H6 | 8 | 9 | 11 | 13 | 16 | 19 | 22 | 25 | 29 | 32 | 36 | |||||||||
0 | 0 | 0 | 0 | 0 | 0 | 0 | 0 | 0 | 0 | 0 | ||||||||||
H7 | 12 | 15 | 18 | 21 | 25 | 30 | 35 | 40 | 46 | 52 | 57 | |||||||||
0 | 0 | 0 | 0 | 0 | 0 | 0 | 0 | 0 | 0 | 0 | ||||||||||
H8 | 18 | 22 | 27 | 33 | 39 | 46 | 54 | 63 | 72 | 81 | 89 | |||||||||
0 | 0 | 0 | 0 | 0 | 0 | 0 | 0 | 0 | 0 | 0 | ||||||||||
H9 | 30 | 36 | 43 | 52 | 62 | 74 | 87 | 100 | 115 | 130 | 140 | |||||||||
0 | 0 | 0 | 0 | 0 | 0 | 0 | 0 | 0 | 0 | 0 | ||||||||||
H10 | 48 | 58 | 70 | 84 | 100 | 120 | 140 | 160 | 185 | 210 | 230 | |||||||||
0 | 0 | 0 | 0 | 0 | 0 | 0 | 0 | 0 | 0 | 0 | ||||||||||
H11 | 75 | 90 | 110 | 130 | 160 | 190 | 220 | 250 | 290 | 320 | 360 | |||||||||
0 | 0 | 0 | 0 | 0 | 0 | 0 | 0 | 0 | 0 | 0 | ||||||||||
J6 | 5 | 5 | 6 | 8 | 10 | 13 | 16 | 18 | 22 | 25 | 29 | |||||||||
-3 | -4 | -5 | -5 | -6 | -6 | -6 | -7 | -7 | -7 | -7 | ||||||||||
J7 | 6 | 8 | 10 | 12 | 14 | 18 | 22 | 26 | 30 | 36 | 39 | |||||||||
-6 | -7 | -8 | -9 | -11 | -12 | -13 | -14 | -16 | -16 | -18 | ||||||||||
J8 | 10 | 12 | 15 | 20 | 24 | 28 | 34 | 41 | 47 | 55 | 60 | |||||||||
-8 | -10 | -12 | -13 | -15 | -18 | -20 | -22 | -25 | -26 | -29 | ||||||||||
JS6 | 4 | 4.5 | 5.5 | 6.5 | 8 | 9.5 | 11 | 12.5 | 14.5 | 16 | 18 | |||||||||
-4 | -4.5 | -5.5 | -6.5 | -8 | -9.5 | -11 | -12.5 | -14.5 | -16 | -18 | ||||||||||
JS7 | 6 | 7.5 | 9 | 10.5 | 12.5 | 15 | 17.5 | 20 | 23 | 26 | 28.5 | |||||||||
-6 | -7.5 | -9 | -10.5 | -12.5 | -15 | -17.5 | -20 | -23 | -26 | -28.5 | ||||||||||
JS8 | 9 | 11 | 13.5 | 16.5 | 19.5 | 23 | 27 | 31.5 | 36 | 40.5 | 44.5 | |||||||||
-9 | -11 | -13.5 | -16.5 | -19.5 | -23 | -27 | -31.5 | -36 | -40.5 | -44.5 | ||||||||||
K6 | 2 | 2 | 2 | 2 | 3 | 4 | 4 | 4 | 5 | 5 | 7 | |||||||||
-6 | -7 | -9 | -11 | -13 | -15 | -18 | -21 | -24 | -27 | -29 | ||||||||||
K7 | 3 | 5 | 6 | 6 | 7 | 9 | 10 | 12 | 13 | 16 | 17 | |||||||||
-9 | -10 | -12 | -15 | -18 | -21 | -25 | -28 | -33 | -36 | -40 | ||||||||||
K8 | 5 | 6 | 8 | 10 | 12 | 14 | 16 | 20 | 22 | 25 | 28 | |||||||||
-13 | -16 | -19 | -23 | -27 | -32 | -38 | -43 | -50 | -56 | -61 | ||||||||||
M6 | -1 | -3 | -4 | -4 | -4 | -5 | -6 | -8 | -8 | -9 | -10 | |||||||||
-9 | -12 | -15 | -17 | -20 | -24 | -28 | -33 | -37 | -41 | -46 | ||||||||||
M7 | 0 | 0 | 0 | 0 | 0 | 0 | 0 | 0 | 0 | 0 | 0 | |||||||||
-12 | -15 | -18 | -21 | -25 | -30 | -35 | -40 | -46 | -52 | -57 | ||||||||||
M8 | 2 | 1 | 2 | 4 | 5 | 5 | 6 | 8 | 9 | 9 | 11 | |||||||||
-16 | -21 | -25 | -29 | -34 | -41 | -48 | -55 | -63 | -72 | -78 | ||||||||||
N6 | -5 | -7 | -9 | -11 | -12 | -14 | -16 | -20 | -22 | -25 | -26 | |||||||||
-13 | -16 | -20 | -24 | -28 | -33 | -38 | -45 | -51 | -57 | -62 | ||||||||||
N7 | -4 | -4 | -5 | -7 | -8 | -9 | -10 | -12 | -14 | -14 | -16 | |||||||||
-16 | -19 | -23 | -28 | -33 | -39 | -45 | -52 | -60 | -66 | -73 | ||||||||||
N8 | -2 | -3 | -3 | -3 | -3 | -4 | -4 | -4 | -5 | -5 | -5 | |||||||||
-20 | -25 | -30 | -36 | -42 | -50 | -58 | -67 | -77 | -86 | -94 | ||||||||||
Platz 6 | -9 | -12 | -15 | -18 | -21 | -26 | -30 | -36 | -41 | -47 | -51 | |||||||||
-17 | -21 | -26 | -31 | -37 | -45 | -52 | -61 | -70 | -79 | -87 | ||||||||||
Platz 7 | -8 | -9 | -11 | -14 | -17 | -21 | -24 | -28 | -33 | -36 | -41 | |||||||||
-20 | -24 | -29 | -35 | -42 | -51 | -59 | -68 | -79 | -88 | -98 | ||||||||||
Platz 8 | -12 | -15 | -18 | -22 | -26 | -32 | -37 | -43 | -50 | -56 | -62 | |||||||||
-30 | -37 | -45 | -55 | -65 | -78 | -91 | -106 | -122 | -137 | -151 | ||||||||||
R6 | -12 | -16 | -20 | -24 | -29 | -35 | -37 | -44 | -47 | -56 | -58 | -61 | -68 | -71 | -75 | -85 | -89 | -97 | -103 | |
-20 | -25 | -31 | -37 | -45 | -54 | -56 | -66 | -69 | -81 | -83 | -86 | -97 | -100 | -104 | -117 | -121 | -133 | -139 | ||
R7 | -11 | -13 | -16 | -20 | -25 | -30 | -32 | -38 | -41 | -48 | -50 | -53 | -60 | -63 | -67 | -74 | -78 | -87 | -93 | |
-23 | -28 | -34 | -41 | -50 | -60 | -62 | -73 | -76 | -88 | -90 | -93 | -106 | -109 | -113 | -126 | -130 | -144 | -150 |
2.2 ISO 286 Maßtoleranztabelle – Lochdurchmessertoleranz
Diese Tabelle beschreibt die Lochdurchmessertoleranz basierend auf verschiedenen IT-Klassen (Toleranzklassen) für verschiedene Lochdurchmesserbereiche.
Größenbereich (mm) | IT7 Toleranz (mm) | IT8 Toleranz (mm) | IT9 Toleranz (mm) |
1 – 3 | ±0,020 | ±0,025 | ±0,030 |
3 – 6 | ±0,025 | ±0,030 | ±0,035 |
6 – 10 | ±0,030 | ±0,035 | ±0,040 |
10 – 18 | ±0,035 | ±0,040 | ±0,045 |
18 – 30 | ±0,040 | ±0,045 | ±0,050 |
30 – 50 | ±0,050 | ±0,060 | ±0,070 |
2.3 ISO 286 Maßtoleranztabelle – Wellendurchmessertoleranz
Diese Tabelle zeigt die Toleranz für den Wellendurchmesser basierend auf verschiedenen IT-Klassen.
Größenbereich (mm) | IT7 Toleranz (mm) | IT8 Toleranz (mm) | IT9 Toleranz (mm) |
1 – 3 | ±0,020 | ±0,025 | ±0,030 |
3 – 6 | ±0,025 | ±0,030 | ±0,035 |
6 – 10 | ±0,030 | ±0,035 | ±0,040 |
10 – 18 | ±0,035 | ±0,040 | ±0,045 |
18 – 30 | ±0,045 | ±0,050 | ±0,060 |
30 – 50 | ±0,060 | ±0,070 | ±0,080 |
2.4 ISO 286 IT-Grade-Toleranztabelle
Diese Tabelle zeigt den Toleranzbereich für verschiedene IT-Klassen und hilft bei der Auswahl der geeigneten Toleranzgenauigkeit.
IT-Grad | Toleranzbereich (mm) |
IT01 | ±0,0025 |
IT2 | ±0,005 |
IT3 | ±0,010 |
IT4 | ±0,015 |
IT5 | ±0,025 |
IT6 | ±0,050 |
IT7 | ±0,080 |
IT8 | ±0,120 |
IT9 | ±0,180 |
2.5 ISO 286 Toleranzband-Berechnungstabelle
Diese Tabelle zeigt die zulässigen Abweichungen zwischen Bohrungen und Wellen für verschiedene Toleranzbänder (wie z. B. H7 und H7).
Passform | Lochtoleranz (mm) | Wellentoleranz (mm) |
H7 | ±0,025 | 0.000 |
H8 | ±0,030 | 0.000 |
h7 | ±0,025 | ±0,000 |
h8 | ±0,030 | ±0,000 |
2.6 ISO 286 Durchmessertoleranztabelle (Loch- und Wellendurchmesser)
In dieser Tabelle sind die Toleranzen für Loch- und Wellendurchmesser in unterschiedlichen Größenbereichen aufgeführt, die für die Passungspräzisionskontrolle bei der mechanischen Bearbeitung gelten.
Größenbereich (mm) | Lochtoleranz (mm) | Wellentoleranz (mm) |
3 – 6 | ±0,025 | ±0,020 |
6 – 10 | ±0,035 | ±0,030 |
10 – 18 | ±0,045 | ±0,035 |
18 – 30 | ±0,060 | ±0,045 |
30 – 50 | ±0,080 | ±0,060 |
2.7 ISO 286 Toleranzband und Passungstabelle
In dieser Tabelle sind die verschiedenen Toleranzbereiche (z. B. H7, h7 und P7) für Loch- und Wellenpassungen aufgeführt, um die Passgenauigkeit sicherzustellen.
Passform | Lochtoleranz (mm) | Wellentoleranz (mm) |
H7 | ±0,025 | 0.000 |
H8 | ±0,030 | 0.000 |
h7 | ±0,025 | ±0,000 |
h8 | ±0,030 | ±0,000 |
Platz 7 | ±0,030 | 0.000 |
2.8 ISO 1101: Geometrische Toleranzen
Die Norm ISO 1101 stellt sicher, dass Lochposition und -form nach dem Stanzen den Konstruktionsanforderungen entsprechen, insbesondere bei der Präzisionsbearbeitung, bei der die Genauigkeit der Lochposition entscheidend ist. Durch die entsprechende Festlegung geometrischer Toleranzen können Hersteller die genaue Position und Form jedes Lochs gewährleisten und so Fehler bei der Montage und beim Schweißen vermeiden.
ISO 1101 ist eine internationale Norm, die geometrische Toleranzen für mechanische Teile, wie Form, Maßgenauigkeit und Montageanforderungen, definiert. Sie bietet Symbole und Methoden zur Kennzeichnung zulässiger geometrischer Abweichungen in Fertigungs- und Montageprozessen. Geometrische Toleranzen werden typischerweise auf Teile angewendet, die hohe Präzision erfordern, wie Lager, Zahnräder und Zahnstangen.
3.0 Kernaspekte der ISO 1101: Geometrische Toleranzen
Symbole für geometrische Toleranzen
ISO 1101 definiert verschiedene Symbole zur Darstellung unterschiedlicher geometrischer Anforderungen. Zu den gängigen Symbolen für geometrische Toleranzen gehören:
- Geradlinigkeit (⎯): Stellt sicher, dass eine Oberfläche oder Kontur innerhalb eines angegebenen Bereichs gerade bleibt.
- Ebenheit (▭): Stellt sicher, dass eine Oberfläche innerhalb einer angegebenen flachen Ebene bleibt.
- Rundheit (O): Stellt sicher, dass die Rundheit einer kreisförmigen Kontur innerhalb eines akzeptablen Bereichs liegt.
- Zylindrizität (◯): Stellt sicher, dass eine zylindrische Form sowohl hinsichtlich der Achse als auch des Durchmessers innerhalb eines angegebenen Toleranzbereichs bleibt.
- Rechtwinkligkeit (⊥): Stellt sicher, dass die Beziehung zwischen zwei Oberflächen oder Achsen senkrecht ist.
- Parallelität (∥): Stellt sicher, dass zwei Oberflächen oder Linien parallel bleiben.
- Konzentrizität (⌀): Stellt sicher, dass sich die Achsen zweier kreisförmiger Features überlappen.
- Positionstoleranz (⊙): Definiert die Positionstoleranz für Löcher, Wellen oder andere Merkmale im Raum.
3.1 Geometrische Toleranzen mit Bemaßung
Geometrische Toleranzen werden üblicherweise mit der Bemaßung kombiniert, um die genaue Form und die Montageanforderungen eines Werkstücks festzulegen. Zum Beispiel:
- Geometrische Toleranzen für Löcher: Werden häufig verwendet, um die Position und Abweichung von Löchern in einer Ebene anzugeben.
- Geometrische Toleranzen der Welle: Können Geradheit, Rundheit oder Konzentrizität umfassen.
3.2 Anwendungen geometrischer Toleranzen
In der Praxis werden geometrische Toleranzen neben anderen Maßtoleranzen verwendet, um die korrekte Funktion des Produkts bei Montage und Gebrauch sicherzustellen. ISO 1101 enthält detaillierte Regeln für die Interpretation und Anwendung dieser Toleranzsymbole, um sicherzustellen, dass Fertigungsprozesse den Konstruktionsspezifikationen entsprechen.
3.3 Allgemeine Tabellen für geometrische Toleranzen
Toleranztyp | Symbol | Bedeutung | Anwendungsbereich |
Geradheit | ⎯ | Stellt sicher, dass eine Oberfläche oder Linie innerhalb eines angegebenen Geradheitsbereichs liegt | Für alle linearen Konturen und Flächen einsetzbar |
Ebenheit | ▭ | Stellt sicher, dass eine Oberfläche flach ist und alle Punkte innerhalb einer angegebenen Ebene liegen | Wird für flache bearbeitete Teile verwendet |
Rundheit | O | Stellt sicher, dass eine Kontur innerhalb eines angegebenen Rundheitsbereichs liegt | Wird für kreisförmige Elemente wie Wellen und Löcher verwendet |
Zylindrizität | ◯ | Stellt sicher, dass eine zylindrische Oberfläche innerhalb eines angegebenen Zylindrizitätsbereichs liegt | Wird für alle zylindrischen Teile verwendet |
Rechtwinkligkeit | ⊥ | Stellt eine senkrechte Beziehung zwischen zwei Flächen oder Achsen sicher | Wird für Teile verwendet, die eine präzise Montage erfordern |
Parallelität | ∥ | Stellt sicher, dass zwei Oberflächen oder Linien parallel sind | Wird für Komponenten verwendet, die eine präzise Montage erfordern |
4.0 ISO 2768: Allgemeine Toleranzen für Maße
ISO 2768 bietet allgemeine Toleranzrichtlinien für Abmessungen in der mechanischen Konstruktion und umfasst Maßtoleranzen für lineare und Winkelmaße. Sie wird häufig für unkritische Abmessungen verwendet, die keine präzise Toleranzkontrolle erfordern. Beim Stanzen von Rohrlöchern trägt diese Norm dazu bei, die allgemeine Maßgenauigkeit für Teile aufrechtzuerhalten, die nicht direkt an wichtigen Funktionsverbindungen beteiligt sind, aber dennoch Qualitätsstandards erfüllen müssen.
4.1 ISO 2768 Toleranztabelle – Allgemeine Toleranzen für Längenmaße
Abmessung (mm) | Toleranz (mm) |
0.5 – 3 | ±0,05 |
3 – 6 | ±0,10 |
6 – 30 | ±0,15 |
30 – 120 | ±0,20 |
120 – 400 | ±0,30 |
400 – 1000 | ±0,50 |
4.2 ISO 2768 Toleranztabelle – Allgemeine Toleranzen für Winkelmaße
Winkel (°) | Toleranz (°) |
0 – 10 | ±1,0 |
10 – 30 | ±1,5 |
30 – 90 | ±2,0 |
90 – 180 | ±2,5 |
Diese Toleranzen werden angewendet, um sicherzustellen, dass die Teile korrekt zusammengebaut werden können, auch wenn sie hinsichtlich der Maßgenauigkeit nicht so kritisch sind.
5.0 Lochpositionierung und andere besondere Überlegungen
Neben Maß- und Geometrietoleranzen ist die Kontrolle der Lochposition ein weiterer kritischer Faktor beim Rohrlochstanzen. Die Position der Löcher im Verhältnis zur Gesamtstruktur des Rohrs muss den vorgegebenen Positionstoleranzen der Konstruktion entsprechen. ISO 1101 legt die Definition von Positionstoleranzen für Löcher fest, um sicherzustellen, dass die Löcher an den richtigen Stellen im Verhältnis zum Rohr gestanzt werden.
Positionstoleranz (ISO 1101): Die Positionstoleranz definiert die zulässige Abweichung von der Position einer Bohrung. Sie wird üblicherweise durch einen Referenzpunkt definiert und ist entscheidend für die korrekte Ausrichtung von Bohrungen mit anderen Teilen, z. B. beim Schweißen oder Montieren von Rohren.
6.0 Abstandsleitfaden zum Stanzen von Weichstahl
Abstandsleitfaden zum Stanzen von Weichstahl | |||||||||||||||||||
Dicke von Weichstahl | |||||||||||||||||||
Stempel Größe |
1/8 | 1/4 | 3/8 | 1/2 | 5/8 | 3/4 | 7/8 | 1″ | |||||||||||
3/16 | 13/64 | ||||||||||||||||||
1/4 | 17/64 | ||||||||||||||||||
5/16 | 21/64 | 11/32 | |||||||||||||||||
3/8 | 25/64 | 13/32 | 13/32 | ||||||||||||||||
7/16 | 29/64 | 15/32 | 15/32 | ||||||||||||||||
1/2 | 33/64 | 17/32 | 17/32 | 9/16 | |||||||||||||||
9/16 | 37/64 | 19/32 | 19/32 | 5/8 | |||||||||||||||
5/8 | 41/64 | 21/32 | 21/32 | 11/16 | 11/16 | ||||||||||||||
11/16 | 45/64 | 23/32 | 23/32 | 3/4 | 3/4 | ||||||||||||||
3/4 | 49/64 | 25/32 | 25/32 | 13/16 | 13/16 | 27/32 | |||||||||||||
13/16 | 53/64 | 27/32 | 27/32 | 7/8 | 7/8 | 29/32 | |||||||||||||
7/8 | 57/64 | 29/32 | 29/32 | 15/16 | 15/16 | 31/32 | 31/32 | ||||||||||||
15/16 | 61/64 | 31/32 | 31/32 | 1 | 1 | 1-1/32 | 1-1/32 | ||||||||||||
1 | 1-1/64 | 1-1/32 | 1-1/32 | 1-1/16 | 1-1/16 | 1-3/32 | 1-3/32 | 1-1/8 | |||||||||||
1-1/16 | 1-5/64 | 1-3/32 | 1-3/32 | 1-1/8 | 1-1/8 | 1-5/32 | 1-5/32 | 1-3/16 | |||||||||||
1-1/8 | 1-9/64 | 1-5/32 | 1-5/32 | 1-3/16 | 1-3/16 | 1-7/32 | 1-7/32 | 1-1/4 | |||||||||||
1-3/16 | 1-13/64 | 1-7/32 | 1-7/32 | 1-1/4 | 1-1/4 | 1-9/32 | 1-9/32 | 1-5/16 | |||||||||||
1-1/4 | 1-17/64 | 1-9/32 | 1-9/32 | 1-5/16 | 1-5/16 | 1-11/32 | 1-11/32 | 1-3/8 | |||||||||||
1-5/16 | 1-21/64 | 1-11/32 | 1-11/32 | 1-3/8 | 1-3/8 | 1-13/32 | 1-13/32 | 1-7/16 | |||||||||||
1-3/8 | 1-25/64 | 1-13/32 | 1-13/32 | 1-7/16 | 1-7/16 | 1-15/32 | 1-15/32 | 1-1/2 | |||||||||||
1-7/16 | 1-29/64 | 1-15/32 | 1-15/32 | 1-1/2 | 1-1/2 | 1-17/32 | 1-17/32 | 1-9/16 | |||||||||||
1-1/2 | 1-33/64 | 1-17/32 | 1-17/32 | 1-9/16 | 1-9/16 | 1-19/32 | 1-19/32 | 1-5/8 |
7.0 Empfohlene Tonnage zum Stanzen von Weichstahl
Empfohlene Tonnage zum Stanzen von Weichstahl | |||||||||||||||||||||
Dicke von Weichstahl |
Stempelgröße | ||||||||||||||||||||
3/16 | 1/4 | 5/16 | 3/8 | 7/16 | 1/2 | 9/16 | 5/8 | 11/16 | 3/4 | 13/16 | 7/8 | 15/16 | 1″ | 1-1/8 | 1-1/4 | ||||||
3/16 1/4 |
.187 | 3 | 4 | 5 | 6 | 7 | 7 | 8 | 9 | 10 | 11 | 12 | 13 | 14 | 15 | 17 | 19 | ||||
.250 | 5 | 6 | 8 | 9 | 10 | 11 | 12 | 14 | 15 | 16 | 18 | 19 | 20 | 22 | 25 | ||||||
3/8 | .375 | 11 | 13 | 15 | 17 | 19 | 21 | 22 | 24 | 26 | 28 | 30 | 34 | 38 | |||||||
1/2 | .500 | 20 | 22 | 25 | 28 | 30 | 32 | 35 | 38 | 40 | 45 | 50 | |||||||||
5/8 | .625 | 31 | 34 | 38 | 41 | 44 | 47 | 50 | 56 | 62 | |||||||||||
3/4 | .750 | 45 | 49 | 52 | 56 | 60 | 68 | 75 | |||||||||||||
7/8 | .875 | 61 | 66 | 70 | 79 | 88 | |||||||||||||||
1 | |||||||||||||||||||||
1.000 | 80 | 90 |
7.1 Abschluss
ISO-Toleranznormen spielen eine entscheidende Rolle bei der präzisen Ausführung von Rohrlochstanzungen und anderen Bearbeitungsvorgängen. Durch die Einhaltung dieser international anerkannten Normen können Hersteller sicherstellen, dass die gestanzten Löcher sowohl die dimensionalen als auch die geometrischen Anforderungen erfüllen, was zu hochwertigen, zuverlässigen Produkten führt.
7.2 Anhang: Häufig verwendete Toleranzen beim Rohrlochstanzen
Typ | Toleranz (mm) | Hinweise |
Lochdurchmesser | ±0,10 – ±0,20 | Abhängig von Rohrgröße und Material |
Lochposition | ±0,10 – ±0,20 | Basierend auf dem Referenzpunkt oder Datum |
Rechtwinkligkeit | ±0,05 – ±0,10 | Stellt sicher, dass die Löcher senkrecht zum Rohr stehen |
Rundheit der Löcher | ±0,05 – ±0,10 | Sorgt dafür, dass die Löcher kreisförmig bleiben |
Ebenheit des Lochs | ±0,05 – ±0,10 | Stellt sicher, dass die Oberfläche des gestanzten Lochs eben bleibt |
Durch Bezugnahme auf diese Tabellen und Befolgen der entsprechenden Normen können Hersteller sicherstellen, dass der Lochstanzvorgang präzise erfolgt und die Rohre im Endprodukt richtig zusammenpassen.
https://www.dimensionalconsulting.com/tolerance-of-position.html
https://slideplayer.com/slide/15857807/
https://www.clevelandsteeltool.com/