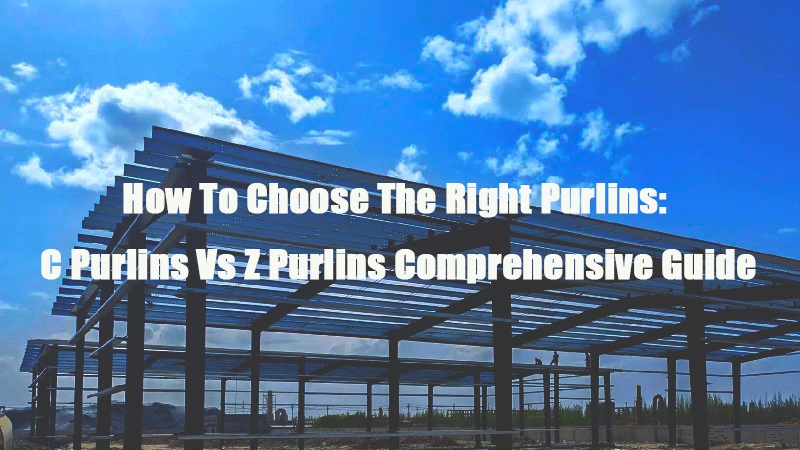
- 1.0What Are the Differences Between C Purlins and Z Purlins?
- 2.0When Should You Choose C Purlins?
- 3.0Why Are Z Purlins Preferred for Large-Span Roofs?
- 4.0Detailed Installation Methods for C Purlins and Z Purlins
- 5.0Common Issues and Maintenance Guide for Purlins
- 6.0How to Choose Suitable Purlins for Building Steel Structures
- 7.0Comparison of Manufacturing Processes for C Purlins and Z Purlins
C purlins and Z purlins are essential structural components in modern building construction, providing support and reinforcement to roof structures and walls. They are commonly used for columns, beams, girders, studs, floors, composite parts, and other components.
In this article, we will delve into the different characteristics and importance of C purlins and Z purlins and discuss how to make the best choice based on specific requirements.
1.0What Are the Differences Between C Purlins and Z Purlins?
1.1Cross-sectional Shape
C Purlins: The cross-section resembles the letter “C.” They have a symmetrical structure with an open groove design, usually at a 90-degree angle, which is perpendicular to its base.
Z Purlins: The cross-section resembles the letter “Z,” with two connected grooves and an angle typically less than 90 degrees, usually between 60 and 75 degrees. They are suitable for longer-span building structures.
1.2Load-Bearing Capacity
C Purlins: Suitable for shorter-span buildings, C section purlins offer stable performance under uniform loads.
Z Purlins: Suitable for larger loads or longer-span buildings, Z section steel purlins provide relatively high resistance to torsion and bending, capable of handling greater loads with fewer support points.
1.3Installation Method
C Purlin Installation:
- Calculate the installation position and spacing.
- Install brackets on the supporting structure.
- Use bolts to secure the C purlins to the brackets.
- Ensure the purlins are aligned and level.
Z Purlin Installation:
- Determine the location and spacing of the overlap connections.
- Overlap and connect Z purlins according to design drawings.
- Secure the overlap area with bolts and angle steel connectors.
- Install support members and reinforcement.
- Check the alignment and stability of the overlap areas.
1.4Installation Accessories
There are noticeable differences in the parts needed for installing C purlins and Z purlins:
Support Components
C Purlins:Brackets: Basic support components for C purlins, usually installed on steel columns or walls of a building.
Purlin Seats: Directly connected to C purlins, providing stable support.
Z Purlins:Support Components: Often require additional support structures to accommodate the overlapping design of Z purlins, ensuring a secure connection between purlins.
Overlap Support Components: Specifically designed to support the overlapping sections of Z purlins, ensuring the stability of the overall structure.
Fasteners
C Purlins:Bolts: Used to secure C purlins to the support structure, typically used with brackets or purlin seats.
Connection Plates: In some cases, connection plates are used to secure C purlins to other structural components.
Z Purlins:Overlap Bolts: Used to secure the overlapping sections of Z purlins, ensuring a strong connection between purlins.
Angle Steel Connectors: Used to enhance the stability of connections between Z purlins and other structural components, especially at overlap points.
Reinforcement Components
C Purlins:Stiffening Ribs: Additional stiffening ribs may be required in applications with long spans or high loads to improve load-bearing capacity.
Reinforcement Plates: Used to increase the strength and stability of C purlins.
Z Purlins:Stiffening Ribs: Typically used to enhance the torsional performance of Z purlins, especially in long-span applications.
Side Support Components: Improve the stability of Z purlins, preventing deformation under load.
End Components
C Purlins:End Plates: Used to close the ends of purlins.
End Fixing Bolts: Secure the connection between the purlin ends and the support structure.
Z Purlins:End Support Components: Due to the slanted angle of Z purlins, special end support components are typically required to stabilize purlin installation.
Overlap End Plates: Used to handle the overlapping ends of Z purlins, ensuring a secure connection.
1.5Application Scenarios
C Purlins:
- Lightweight Construction: Used in lightweight buildings where installation is easy, such as roofing and wall structures for small factories, warehouses, machine rooms, and residential roofs.
- Small-Scale Spans: Suitable for smaller span roof systems.
- Cost-Effective Choice: Ideal for projects with budget constraints, aiming to reduce material and construction costs.
Z Purlins:
- Large-Span Buildings: Suitable for roofs and wall structures of large-span buildings such as large industrial plants, sports halls, exhibition centers, and other large-scale structures.
- Complex Structures: Z purlins provide multi-directional support, offering uniform support in multiple directions and enhancing the overall stability and safety of the structure.
- High-Requirement Projects: Designed for buildings that need to withstand extreme weather conditions, earthquakes, and other natural disasters.
2.0When Should You Choose C Purlins?
2.1Low Roof Slope
When the roof slope is relatively small (usually slope i<1/3), C purlins can be designed as unidirectional bending members. This means that under smaller slopes, C purlins can effectively bear roof loads and maintain the stability of the structure.
2.2Lightweight Construction or Small-Scale Spans
C purlins are suitable for lightweight buildings that do not require large spans, such as small warehouses, workshops, and residential roof structures.
2.3Cost-Effectiveness
C purlins are ideal for projects with limited budgets or those seeking cost efficiency. C section steel and C channel purlins offer a cost-effective solution for construction needs.
2.4Ease of Processing and Installation
C purlins can be easily cut, drilled, and connected according to on-site requirements, making them convenient for quick installation.
2.5Durability and Corrosion Resistance
C purlins that have undergone hot-dip galvanization or other anti-corrosion treatments can maintain stable performance in various environments, offering a long service life. These roofing C purlins are ideal for applications where long-term durability is a priority.
3.0Why Are Z Purlins Preferred for Large-Span Roofs?
3.1Superior Load-Bearing Capacity and Stability
Stable Structural Design: The cross-section of Z purlins resembles the letter “Z,” with two flanges parallel to each other. This design enhances the purlins’ bending resistance and facilitates easy connections with other purlins, supports, and structures, forming a stable system.
Even Load Distribution: In large-span roofs, Z purlins can evenly distribute roof loads, reducing stress on single points. This feature makes them ideal for large-scale construction projects.
3.2Suitable for Complex Loads and Stress Environments
Multi-Directional Support: The cross-sectional shape of Z purlins allows them to provide uniform support in multiple directions, making them suitable for complex loads and stress requirements, such as wind and snow loads. This is particularly important for large-span roofs.
Wind Resistance: The inherent design of Z purlins offers strong wind resistance, ensuring structural stability even in strong wind conditions.
3.3Ease of Construction and Installation
Standardized Production: Z purlins are typically produced in standardized sizes and specifications, making them easy to install on-site.
Easy Connections: The parallel flanges of Z purlins facilitate easy connections with other components. They can be securely connected to support frames, roof panels, and other structures using bolts, welding, or other methods.
3.4Durability and Corrosion Resistance
Material Selection: Z purlins are usually made from high-quality steel, which is hot-dip galvanized for excellent durability and corrosion resistance.
Adaptability to Various Environments: Z purlins can withstand various harsh environments, such as high temperatures, humidity, and corrosive conditions, over a long period
4.0Detailed Installation Methods for C Purlins and Z Purlins
4.1C Purlin Installation Method
4.2Preparation:
Measurement and Marking: Measure and mark the purlin installation positions according to the design drawings.
Support Structure Check: Verify that the support structure (such as steel columns or walls) is secure.
4.3Bracket Installation:
Install Brackets: Mount brackets on the support structure, usually securing them with bolts to the steel columns or walls.
Bracket Spacing: The spacing of the brackets is typically determined by the span and load of the purlins.
4.4Purlin Installation:
Position Purlins: Place the C purlins onto the brackets, ensuring that the centerline of the purlins aligns with the support structure.
Secure Purlins: Use bolts to fix the C purlins to the brackets. The fixing points of the purlins should be evenly distributed.
Check Level: Use a level to check that the purlins are horizontal and adjust the brackets as needed to ensure the purlins are level.
4.5Connection and Reinforcement:
Connect Purlins: Typically use connectors or additional brackets to secure the connection points.
Reinforcement Measures: Implement necessary reinforcement measures, such as adding lateral supports or bracing.
4.6Acceptance Check:
Check Installation: Inspect the installation of the purlins to ensure all bolts are tightened, and the purlins are aligned and level.
Safety Inspection: Conduct a safety inspection of the overall structure to ensure that the installation meets design standards and safety requirements.
4.7Notes:
Wear protective equipment such as helmets and gloves during installation.
Familiarize yourself with the use of tools like electric drills and hole drills before operation to ensure safety.
Regularly check the levelness and connection firmness of the purlins during installation to meet design requirements.
5.0Common Issues and Maintenance Guide for Purlins
5.1Common Issues:
Corrosion and Rust:
Cause: Prolonged exposure to humid or corrosive environments.
Impact: Without proper anti-corrosion treatment, accelerated corrosion can reduce the strength of purlins and affect structural stability.
Deformation and Bending:
Cause: Overloading or improper installation.
Impact: Affects the load-bearing capacity of the purlins and the overall structure of the building.
Loose Connections:
Purlin fixing bolts
Cause: Wear of bolts or connectors, or improper tightening during installation.
Impact: Leads to unstable support of purlins and potential structural instability or damage.
Damage at Overlap Points:
Cause: Improper design or construction at overlap points.
Impact: Size deviations or inaccurate hole positioning during processing can cause cracks or fractures at overlap points, affecting overall load-bearing capacity.
Cracks and Damage:
Cause: Material quality issues, impact from external forces, or metal fatigue from prolonged use.
Impact: Affects the structural integrity and lifespan of the purlins.
5.2Maintenance Guide:
Regular Inspections:
Conduct regular inspections (e.g., every six months or annually) to check for deformation, cracks, corrosion, or looseness.
Tighten any loose bolts promptly.
Anti-Corrosion Treatment:
Apply anti-corrosion coatings or set up protective layers.
Protect galvanized purlins during installation to avoid scratching or damaging the coating.
Proper Use:
Avoid stacking or hanging excessive weight on purlins to ensure they remain within their load limits.
If additional loads are required, redesign the structure and replace purlins as needed.
Repair and Replacement:
Address any issues with purlins promptly by repairing or replacing damaged components.
Replace damaged parts and remove rust during repairs.
Choose materials that meet design requirements for replacements and process them according to design drawings.
Enhanced Design and Construction Management:
During the design phase, thoroughly consider the load and stability requirements for purlins, including spacing, length, and cross-sectional dimensions.
Follow design drawings strictly during construction to ensure the quality of purlin installation.
6.0How to Choose Suitable Purlins for Building Steel Structures
Common C Purlin Sizes
Size (Inches) | Size (Millimeters) | Notes |
2 x 3 | 50 x 75 | One of the common sizes |
2 x 4 | 50 x 100 | One of the common sizes |
2 x 6 | 50 x 150 | One of the common sizes |
2 x 8 | 50 x 200 | One of the common sizes |
4 x 4 | 100 x 100 | Suitable for heavier loads |
4 x 6 | 100 x 150 | Suitable for heavier loads |
6 x 4 | 150 x 100 | Suitable for larger spans |
6 x 6 | 150 x 150 | Suitable for larger spans |
8 x 8 | 200 x 200 | Suitable for extra-large spans |
Common Z Purlin Sizes
Size (Inches) | Size (Millimeters) | Notes |
2 x 3 | 50 x 75 | One of the common sizes |
2 x 4 | 50 x 100 | One of the common sizes |
2 x 6 | 50 x 150 | One of the common sizes |
2 x 8 | 50 x 200 | One of the common sizes |
4 x 4 | 100 x 100 | Suitable for heavier loads |
4 x 6 | 100 x 150 | Suitable for heavier loads |
6 x 6 | 150 x 150 | Suitable for larger spans |
8 x 6 | 200 x 150 | Suitable for extra-large spans |
7.0Comparison of Manufacturing Processes for C Purlins and Z Purlins
The manufacturing processes for C purlins and Z purlins are similar in fundamental principles, including raw material preparation, cutting, forming, assembly, and subsequent processing. However, there are specific differences in details and focus. Here’s a comparison:
7.1Material Selection:
Typically uses steel plates (such as hot-rolled or cold-rolled steel plates), including steel, galvanized steel plates, or aluminum alloys.
7.2Uncoiling:
Use a Decoiler to unroll and flatten the coil steel for subsequent stamping and forming operations.
Cutting:Steel plates are cut according to design requirements for further processing.
7.3Forming:
C Purlins: The steel plate is bent into a C-shaped cross-section using a C purlin forming machine.
Z Purlins: The steel plate is bent into a Z-shaped cross-section using a Z roll forming machine, involving multiple bending steps.
Modern processing includes CZ interchangeable purlin machines, which can simultaneously process C or Z purlins and quickly switch between the two.
7.4Post-Processing:
After forming, additional processing such as punching or bending may be required, based on special or customized purlins.
7.5Inspection:
Inspect the dimensions, strength, and surface treatment of the purlins to ensure they meet standards.
7.6Summary:
C Purlins are typically used for lighter loads and shorter spans, and are more economical and easier to install.
Z Purlins are better suited for heavier loads and longer spans, offering greater stability and flexibility for complex structures.
Make a reasonable choice based on project requirements and budget considerations.
This translation covers the essentials for choosing and understanding purlins in steel structures, including their sizes and manufacturing processes. Let me know if you need any further details or adjustments!
References: