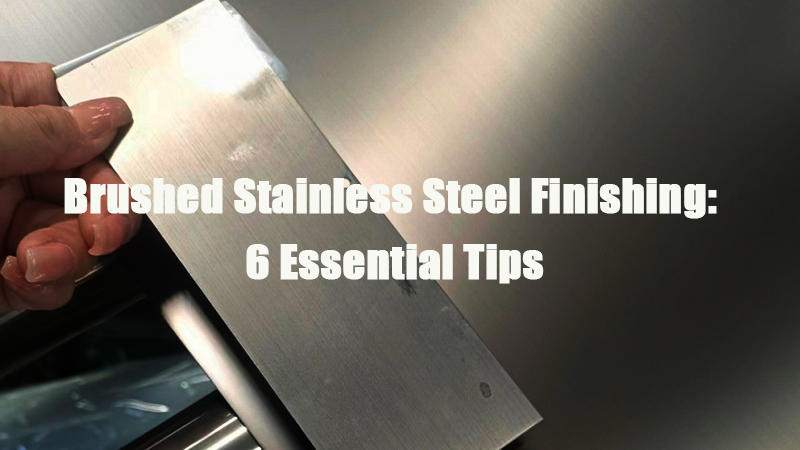
- 1.0 Definition and Uses of Brushed Stainless Steel
- 1.1 Features of Brushed Stainless Steel
- 1.2 Grades of Stainless Steel Surface Treatments
- 1.3 Ra (Average Roughness) Classification
- 1.4 Common Applications of Brushed Stainless Steel
- 1.5 Differences Between Brushed Stainless Steel and Mirror Stainless Steel
- 1.6 Relationship Between Satin and Brushed Finishes
- 2.0 Selecting the Right Tools for Brushing – Process Flow
- 3.0 Determining the Correct Brushing Direction
- 4.0 Using Appropriate Grinding Pressure
- 5.0 Preventing Over-Grinding and Damage
- 6.0 Cleaning and Maintaining Brushed Stainless Steel
- 7.0 Common Questions About Brushed Stainless Steel
1.0 Definition and Uses of Brushed Stainless Steel
Brushed stainless steel refers to the process of creating a continuous, linear texture on the surface of stainless steel through mechanical friction (using abrasive belts or wheels) or chemical treatments. This gives the metal a matte finish with countless fine lines.
Commonly brushed metals include stainless steel, aluminium and nickel.
The intensity of the brushed finish is specified as a surface roughness and is typically 0.5–1.5 micrometres Ra.
The brushing process enhances the aesthetics, wear resistance, and surface texture of stainless steel.
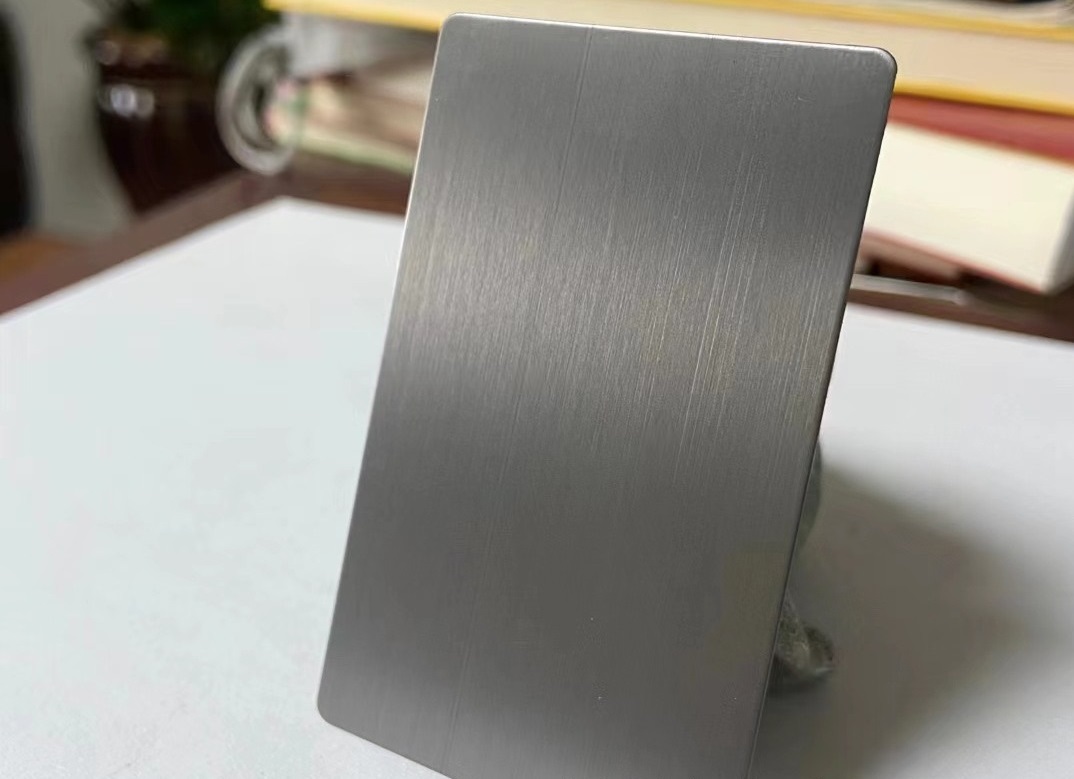
1.1 Features of Brushed Stainless Steel
- Matte Texture:Brushed stainless steel surfaces have uniform lines and a matte effect.
- High Wear Resistance:The brushing process helps hide minor surface scratches, making it more durable.
- Fingerprint Resistance:Compared to mirror-finish stainless steel, brushed stainless steel is less likely to show fingerprints or stains.
- Strong Decorative Appeal: With its textured appearance, brushed stainless steel is often used for decorative and artistic purposes.
1.2 Grades of Stainless Steel Surface Treatments
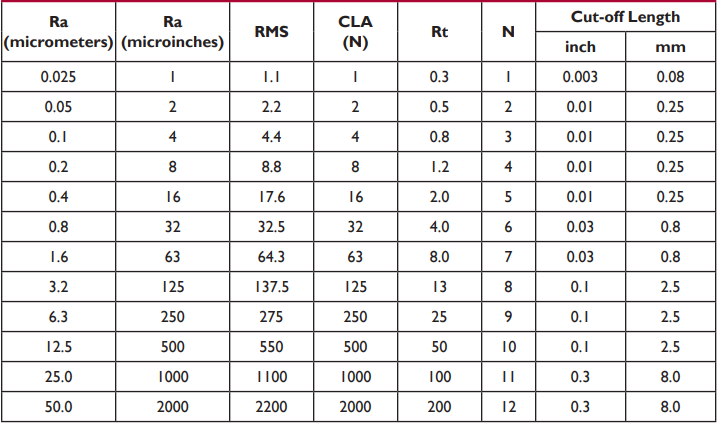
Stainless steel surfaces undergo various treatment processes to form different finish grades, such as No.1, No.2D, No.2B, No.4, No.6, No.7, and No.8.
- No.1: Rough and non-reflective.
- No.2D: Matte, with medium smoothness.
- No.2B: Smooth with a slight reflective sheen, commonly seen as the standard finish.
- No.4: Brushed finish with a matte look, resistant to fingerprints and scratches.
- No.6: Finer brushed texture with a higher gloss.
- No.7: Glossy, with minor polishing marks.
- No.8 (Mirror): Highly polished, with a reflective, flawless finish.
1.3 Ra (Average Roughness) Classification
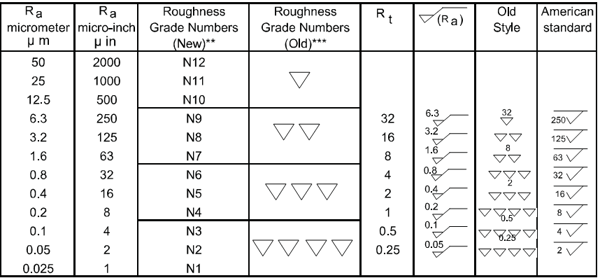
- Ra 12.5 – 25.0 μm: Roughly processed surface
- Ra 3.2 – 6.3 μm: Moderately processed surface
- Ra 1.6 – 3.2 μm: Standard fine finish
- Ra 0.8 – 1.6 μm: Fine finish
- Ra 0.2 – 0.8 μm: Ultra-fine finish
- Ra ≤ 2 μm: Mirror finish
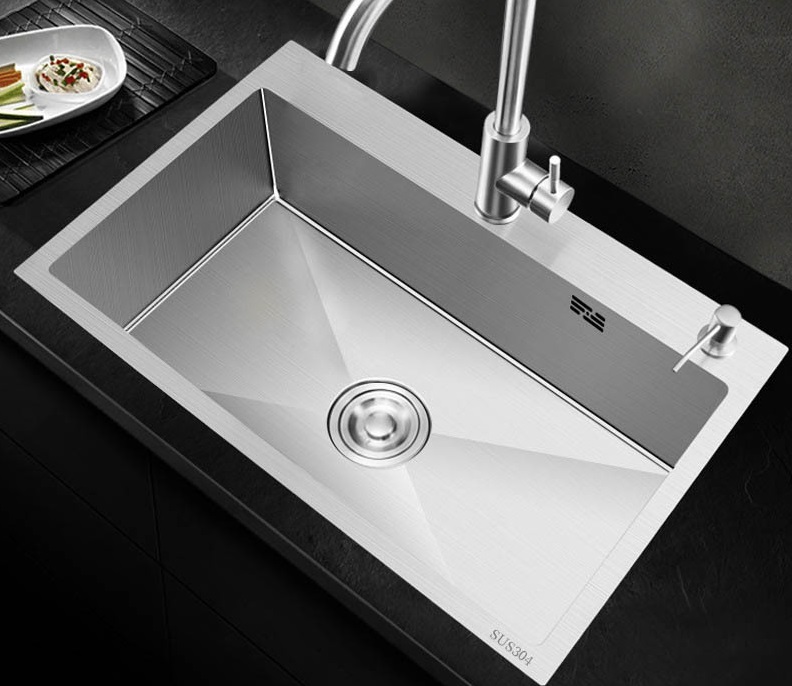
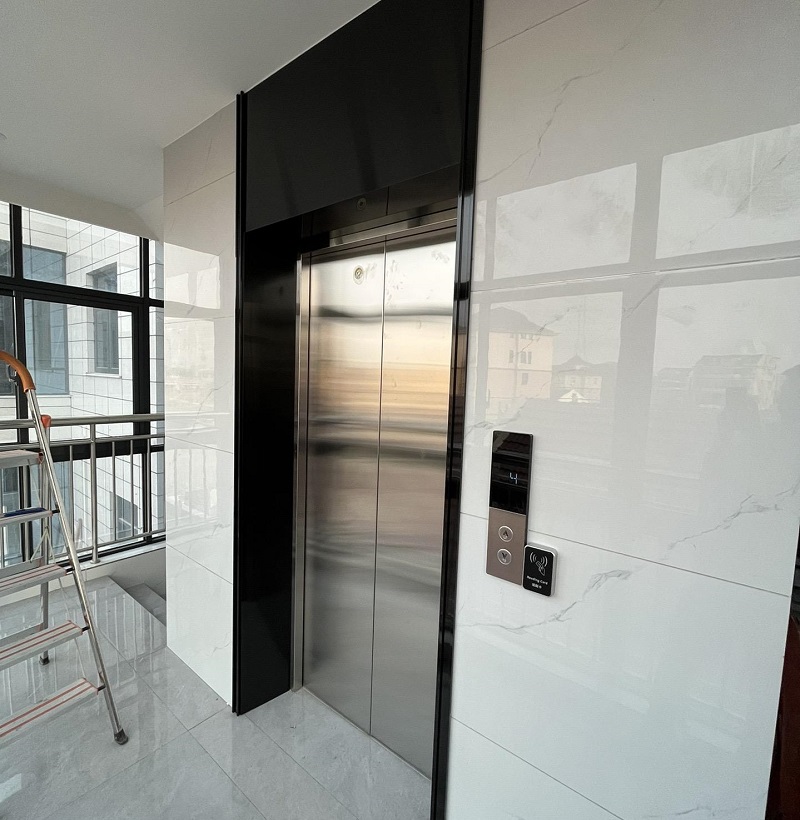
1.4 Common Applications of Brushed Stainless Steel
Brushed stainless steel has a wide range of applications in both commercial and residential designs. Common uses include:
- Household Appliances: Fridge, microwave, dishwasher, and range hood exteriors and panels.
- Kitchen Equipment:Sinks, countertops, cabinet doors, utensils, and cookware.
- Architectural Decoration: Elevator panels, wall cladding, handrails, door frames, and ceiling decorations.
- Furniture and Hardware:Chairs, cabinets, door handles, lighting fixtures, handrails, and mirrors.
- Automotive and Transportation:Interior trim, train cabin decorations, and subway handrails.
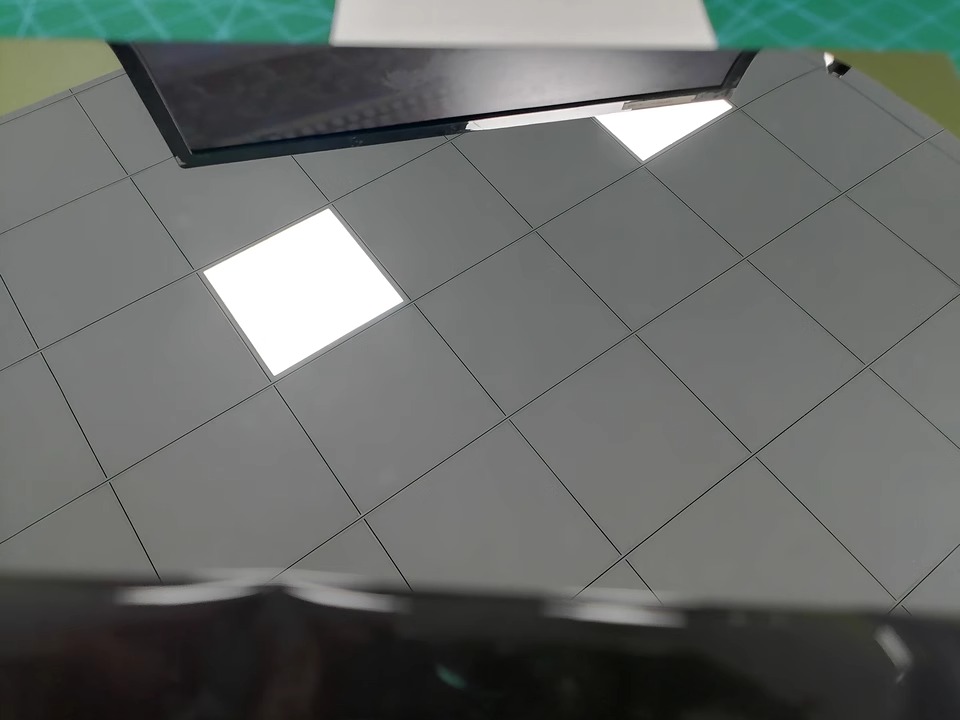
1.5 Differences Between Brushed Stainless Steel and Mirror Stainless Steel
- Brushed Stainless Steel: Features continuous linear texture with a matte finish, non-reflective, hides scratches, and is fingerprint-resistant.
- Mirror Stainless Steel: Highly polished, reflective, and smooth like a mirror. It has a high-end appearance but is more prone to fingerprints, stains, and scratches, which are more noticeable.
1.6 Relationship Between Satin and Brushed Finishes
Both satin and brushed finishes are used for stainless steel surface treatments. Brushed focuses on directionality and lines, while satin emphasizes a smooth, matte effect.
- Brushed Finish:Produces a linear texture on the surface, typically in a single direction, using mechanical or hand polishing with tools like sandpaper or wire brushes.
- Satin Finish: Also known as silk or matte finish, it is smoother and more uniform, typically achieved through finer polishing techniques.
2.0 Selecting the Right Tools for Brushing – Process Flow
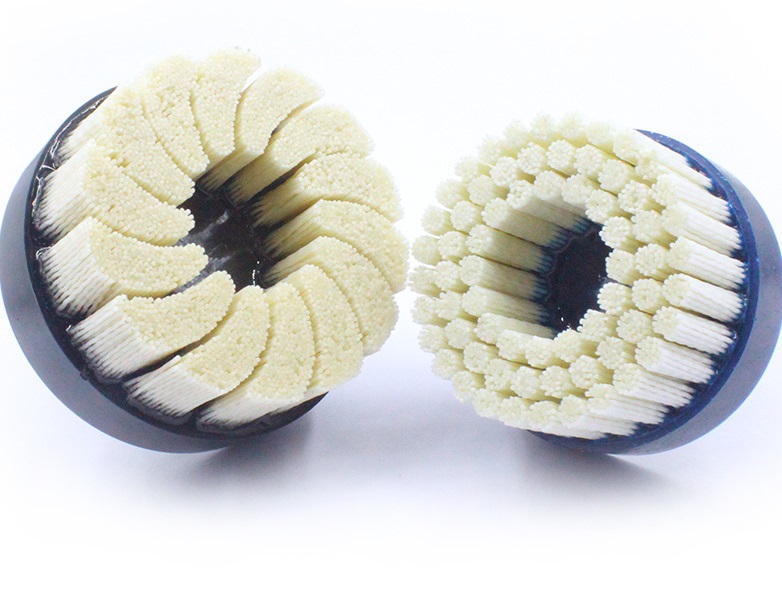
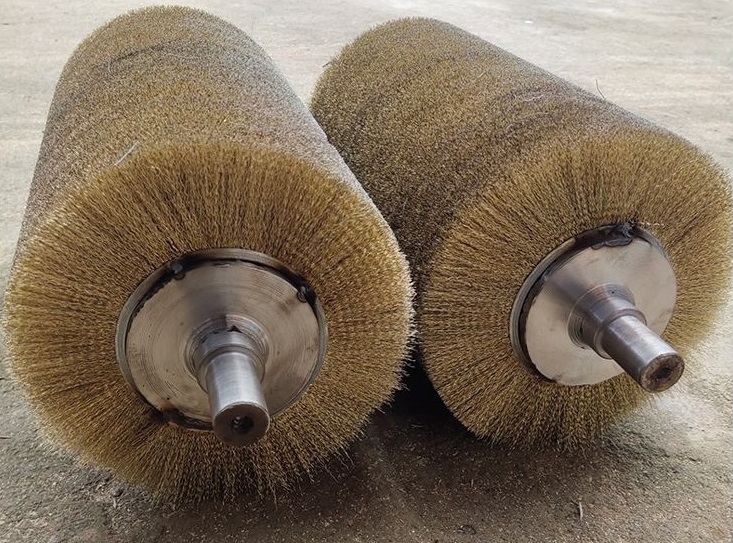
2.1 Preparation Process
- Tool Selection: Wire brush, stainless steel cleaner.
- Function: Before brushing, remove the oxide layer, dirt, and rust. The wire brush efficiently removes the rough layer, ensuring better brushing results. Cleaners help remove dirt and grease.
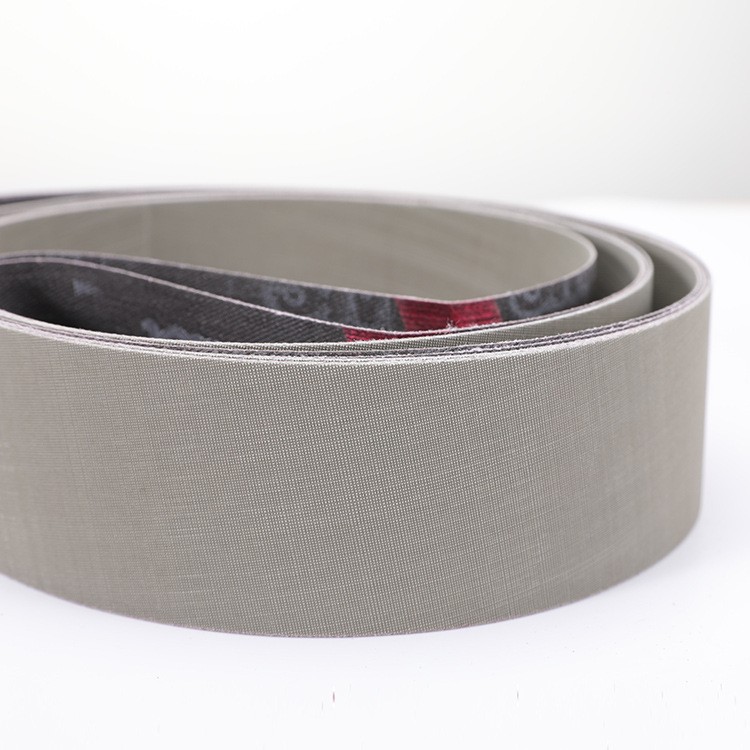
2.2 Rough Processing Step
- Tool Selection:Coarse sandpaper or abrasive belt, electric grinder, angle grinder.
- Function:Rough processing removes larger surface defects and begins to form the brushed texture. Usually, coarse sandpaper (e.g., 60# to 120#) is used for grinding.
- Tips:
Manual Tools: Use coarse sandpaper for small areas or edges for precise control.
Mechanical Tools: Electric belt grinders or angle grinders are more efficient for large areas but require skill to avoid uneven surfaces.
2.3 Finishing Process
- Tool Selection:Fine sandpaper or fine abrasive belt, specialized brushing pad, belt grinder, or polishing machine.
- Function:Fine sandpaper (e.g., 320# to 600#) or fine abrasive belts are used to refine the brushing texture.
- Tips:
oSuitable for detail work and small-scale finishing.
oAdjust speed and pressure to ensure uniform texture.
2.4 Post-Processing
- Tool Selection: Polishing wheel, polishing pad.
- Function: This step focuses on removing micro-scratches and enhancing surface smoothness. Polishing tools provide a more refined finish.
3.0 Determining the Correct Brushing Direction
Whether horizontal, vertical, diagonal, or cross-brushing, the correct brushing direction not only enhances the aesthetic appeal but also helps avoid messy scratches on the surface. Below are the detailed explanations regarding brushing directions:
3.1 Brushing Along the Metal Grain
Stainless steel surfaces typically have a natural grain or direction. When brushing, it is crucial to follow this natural grain to avoid irregular scratches.
3.2 Effects of Different Brushing Directions
- Horizontal Brushing:Horizontal brushing usually results in horizontal linear patterns. This is commonly used for large decorative panels, cabinet doors, and other surfaces in commercial and residential environments.
- Vertical Brushing:Vertical brushing creates vertical linear patterns. This is often applied in environments where a sense of height is needed, such as decorative panels and elevator interiors.
- Diagonal Brushing:Diagonal brushing produces more dynamic and unique patterns, suitable for decorative elements with a design focus, such as art decor and feature furniture.
- Cross-Brushing:Brushing in two or more directions creates complex texture effects. This method is often used for high-end custom projects or highly decorative applications, such as luxury homes, art installations, and feature walls.
4.0 Using Appropriate Grinding Pressure
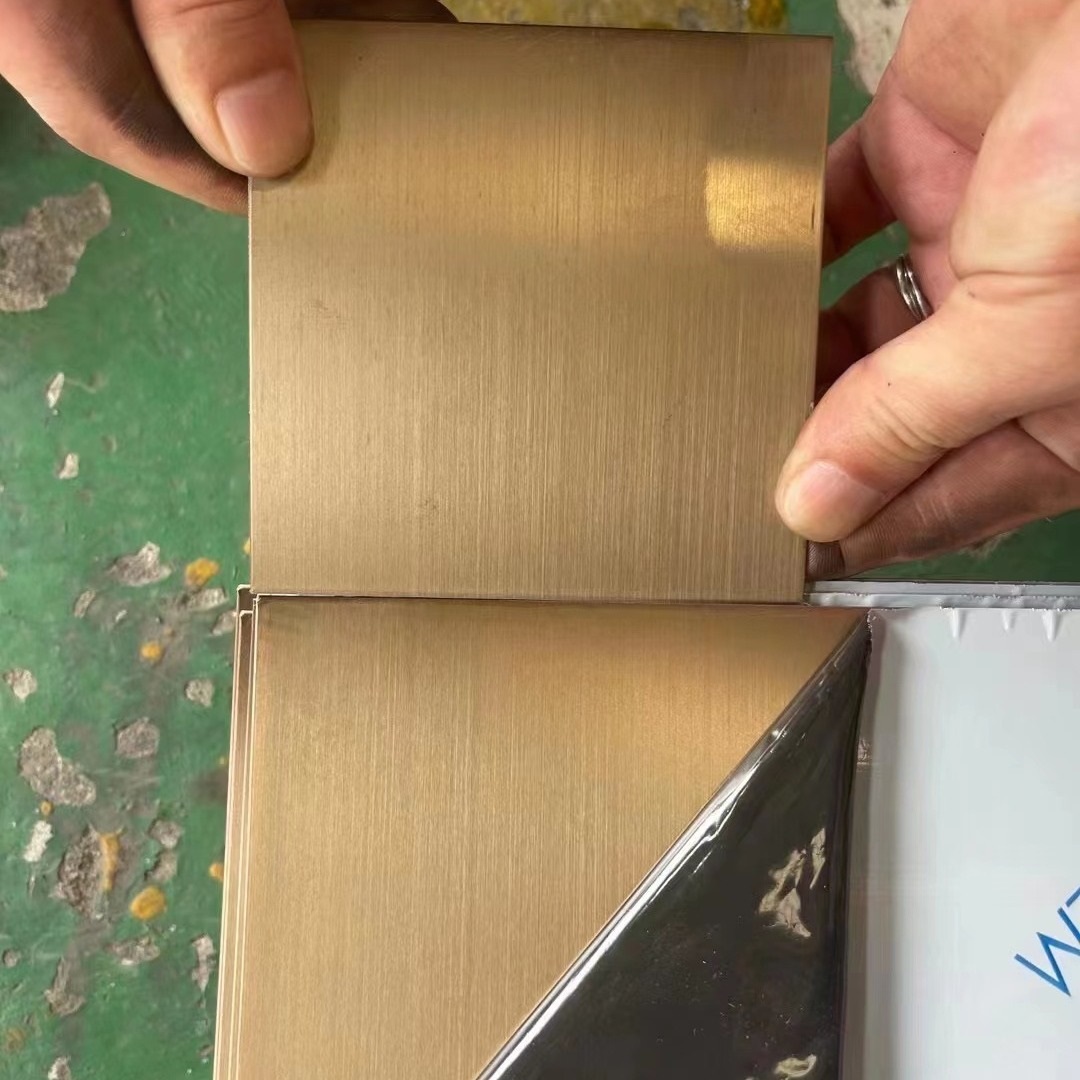
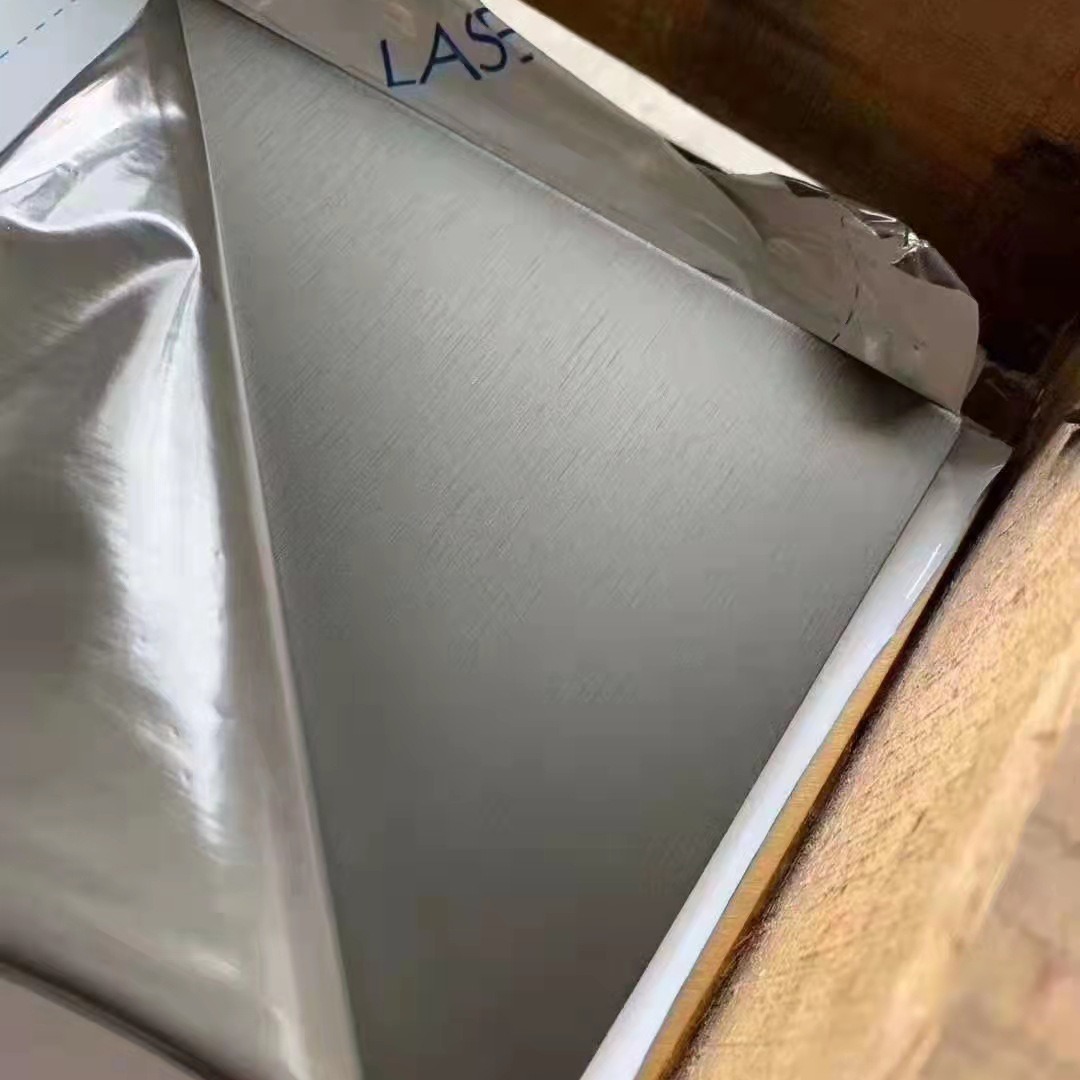
Grinding pressure plays a critical role in stainless steel brushing. Choosing the right pressure ensures uniform surface brushing patterns. By controlling the grinding pressure, you can effectively avoid surface scratches or dents. Below are details on using appropriate grinding pressure:
4.1 Impact of Pressure on Surface Finish
- Excessive Pressure: Applying too much pressure may cause noticeable scratches, dents, or uneven textures on the stainless steel surface. This is especially true when using coarse sandpaper or sanding belts, which can easily damage the surface.
- Moderate Pressure:Moderate grinding pressure ensures the stainless steel surface is treated evenly, resulting in smooth and fine brushing patterns.
Testing: Test on a small, inconspicuous area and adjust the pressure until the desired result is achieved.
Even Pressure: Keep your hand steady and apply pressure evenly to avoid excessive force or localized pressure.
4.2 Gradually Increasing Pressure
When brushing, it is advisable to gradually increase the grinding pressure.
- Initial Stage:Use finer sandpaper or sanding belts for light grinding. The purpose of this step is to remove minor surface imperfections and pre-treat the material for rougher work.
- Transition Stage: Gradually transition to coarser sandpaper or sanding belts, increasing the pressure. This stage helps remove more significant imperfections and irregular textures, but even pressure is still necessary.
- Final Stage:Use fine sandpaper or polishing pads for the final treatment. At this point, adjust the pressure appropriately to ensure the surface achieves the required smoothness and gloss.
Recommendations:
- FineSandpaper: Use for initial grinding with gentle pressure to maintain surface smoothness.
- Coarse Sandpaper: Use when more material removal is needed, gradually increasing pressure while avoiding excessive force.
- Polishing Pads: Use for the final fine and gentle polishing to achieve a smooth finish.
5.0 Preventing Over-Grinding and Damage
To prevent over-grinding and damage, control grinding time and frequency, and use proper lubrication and cooling. This helps avoid excessive grinding and material damage.
Here are specific methods to prevent over-grinding:
5.1 Avoid Excessive Wear: Different thicknesses of stainless steel tolerate grinding differently. Over-grinding can cause the material to become too thin.
- Select the Appropriate Grinding Time: Set an appropriate grinding time based on the material’s thickness and condition.
- Control Grinding Frequency: Avoid frequent grinding in the same area.
- Regular Inspections:Regularly inspect the surface condition of the material.
5.2 Proper Lubrication and Cooling: Adequate lubrication and cooling can effectively prevent heat buildup from friction during grinding.
- Use Lubricating Oil: This reduces friction and helps remove metal debris produced during grinding.
- Water Cooling:Water can be sprayed or used as a flow to cool the surface during grinding. (Electric brushing machines usually have water-cooling systems.)
- Cooling Breaks:Periodically stop to let the material cool, avoiding the impact of sustained high temperatures on the material. (This method is less efficient.)
6.0 Cleaning and Maintaining Brushed Stainless Steel
Cleaning and maintaining brushed stainless steel require choosing appropriate stainless steel cleaners. Avoid using acidic or chloride-based cleaners, and use soft cloths for wiping. Regular cleaning and applying fingerprint-resistant coatings can effectively prevent fingerprints and stains from remaining.
6.1 Using the Right Cleaning Products
- Neutral Cleaners: Choose pH-neutral cleaners that can effectively remove common dirt without affecting the surface finish.
- Soft Cloth Wiping:Use soft, lint-free cloths or microfiber cloths for wiping to avoid scratching the stainless steel surface.
- Avoid Acidic or Chloride-Based Cleaners:These chemicals may corrode the stainless steel surface, causing damage.
Use Specialized Stainless Steel Cleaners: These can effectively remove dirt and form a protective layer on the surface, reducing fingerprints and stains.
6.2 Preventing Fingerprints:
Use Stainless Steel Protective Films: These are used to protect the material from damage during processing, transportation, and installation.
7.0 Common Questions About Brushed Stainless Steel
What is the difference between brushed stainless steel and mirror stainless steel?
Brushed stainless steel has noticeable linear patterns, while mirror stainless steel is highly polished with a reflective mirror-like finish.
What is the difference between brushed stainless steel and brushed nickel?
Brushed stainless steel uses a stainless steel alloy with fine brushed patterns on the surface, while brushed nickel is a nickel alloy that undergoes brushing treatment, resulting in a softer color.
What is a polishing wheel?
A polishing wheel is a tool used for polishing metal surfaces, typically made of cloth, wool, or synthetic materials. It is used to remove scratches and improve the surface smoothness of stainless steel.
What is a sanding belt?
A sanding belt is a belt-shaped sandpaper used for grinding and sanding, typically mounted on belt sanders and polishing machines to remove surface imperfections on stainless steel.
References
https://en.wikipedia.org/wiki/Brushed_metal