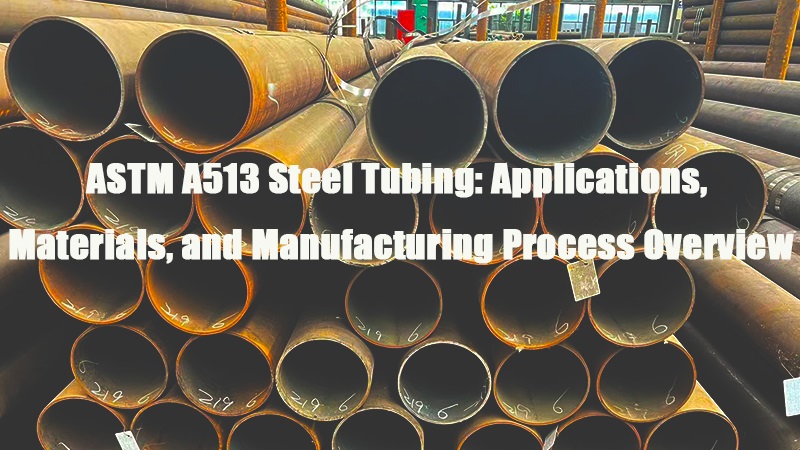
- 1.0ASTM A513 Manufacturing Process Classifications
- 2.0Main Materials of ASTM A513
- 3.0Yield Strength Range of Common ASTM A513 Materials
- 4.0Applications of ASTM A513 in Cold Forming Processes
- 5.0TABLE 1:Chemical Requirements for Standard Low-Carbon Steels
- 6.0TABLE 2:Chemical Requirements for Other Carbon and Alloy Steels
- 7.0TABLE 3:Tolerances for Product Analysis for Steels Shown in Tables 1 and 2
ASTM A513 Steel Tubing: Applications, Materials, and Manufacturing Process Overview
ASTM A513 is a standard established by the American Society for Testing and Materials (ASTM) for welded and cold-worked steel tubing commonly used in metal processing.
It is primarily applicable to mechanical tubing produced by electric-resistance welding and cold drawing.
Through various manufacturing processes and material types, ASTM A513 provides a range of steel tubing options to meet the application needs of diverse mechanical and metal structure markets.
1.0ASTM A513 Manufacturing Process Classifications
Type | Manufacturing Process | Characteristics | Applications |
Type 1 | Hot Rolled Electric-Resistance Welded (ERW) Tubing | Lower surface and dimensional accuracy, moderate strength, suitable for general structural and mechanical purposes | Furniture frames, mechanical supports, industrial equipment supports |
Type 2 | Heat-Treated Electric-Resistance Welded (ERW) Tubing | Enhanced strength and toughness through heat treatment, suitable for high-pressure applications | Automotive parts, high-strength mechanical frames, structural supports |
Type 3 | Cold Drawn Welded Tubing | Improved dimensional accuracy and surface quality through cold drawing, higher yield and tensile strength | Mechanical parts, precision equipment, high-precision piping systems |
Type 4 | Heat-Treated Cold Drawn Welded Tubing | Combines the precision of cold drawing with the strength from heat treatment, suitable for high-stress and impact applications | High-stress mechanical parts, impact-resistant structural components, shafts, rotating parts |
Type 5 | Cold Rolled Electric-Resistance Welded (ERW) Tubing | High accuracy and smooth surface, suitable for precision machining | Precision machinery components, automotive parts, precision engineering equipment |
Type 6 | Cold Rolled and Cold Drawn Electric-Resistance Welded Tubing | Highest dimensional accuracy and surface finish, excellent strength and toughness | High-precision mechanical systems, aerospace equipment, high-demand engineering structures |
2.0Main Materials of ASTM A513
Material Type | Main Grades | Carbon Content | Characteristics | Applications |
Low Carbon Steel | SAE 1008, SAE 1010 | 0.08%-0.10% | Good ductility, easy to form, weld, and cold work, moderate strength, high surface finish | Furniture frames, mechanical supports, industrial equipment supports, automotive parts |
SAE 1020, SAE 1026 | 0.20%-0.26% | Higher tensile and yield strength, maintains good ductility and workability, suitable for welding and machining | Medium-strength mechanical components, precision-machined parts | |
Alloy Steel | 4130 | 0.30% | High strength, good wear resistance, excellent toughness and fatigue performance, good weldability and heat treatability | High-stress structural components, aerospace equipment, climbing gear, race car frames |
4140 | 0.40% | Extremely high strength and wear resistance, suitable for impact and fatigue stress applications, good quenching and tempering properties | High-strength mechanical parts, industrial equipment components, heavy machinery parts | |
Low Alloy High Strength Steel | – | – | Small amounts of alloying elements (e.g., chromium, nickel, molybdenum) added to improve strength and corrosion resistance | Structural and load-bearing components, such as bridges, building frames, truck chassis |
3.0Yield Strength Range of Common ASTM A513 Materials
Material Type | Main Grades | Yield Strength Range (MPa) | Characteristics |
Low Carbon Steel | SAE 1008, 1010 | 205 – 275 | Good ductility, moderate strength, suitable for general structural and mechanical purposes. |
SAE 1020, 1026 | 275 – 380 | Higher yield strength, suitable for structural components and mechanical parts requiring more strength. | |
Alloy Steel | 4130 | 435 – 600 | High strength, suitable for high-stress and fatigue applications, good weldability and heat treatability. |
4140 | 620 – 850 | Extremely high yield strength and wear resistance, suitable for high-load and impact-stress parts. | |
Low Alloy High Strength Steel | – | 345 – 690 | Alloying elements improve strength and corrosion resistance, ideal for structural components such as building frames and bridges. |
4.0Applications of ASTM A513 in Cold Forming Processes
ASTM A513 performs exceptionally well in cold forming processes and is widely used in various industries.
4.1Advantages of ASTM A513 in Cold Forming:
- Excellent machinability
- Balanced strength and ductility
- Easy to weld
4.2Tube Bending:
ASTM A513 material has good ductility and toughness, making it easy to bend tubes without cracking or losing strength.
Applications: Used in manufacturing bent tubes, such as automotive exhaust systems, furniture structures, and building frames.
4.3Stamping and Punching:
Low carbon steel has excellent stamping properties, making it easy to perform complex stamping and punching operations with industrial punch presses while maintaining good surface quality after forming.
Applications: Used to produce various stamped parts, such as mechanical components and metal housings.
4.4Edging and Flanging:
The low-carbon steel types of ASTM A513 exhibit good plasticity in edging and flanging processes, allowing them to form without cracking.
Applications: Used in the production of pipe connectors, flanges, and other edged or flanged parts.
4.5Deep Drawing:
Low carbon steel offers good resistance to deep drawing through cold forming, resulting in smooth surfaces and uniform deformation.
Applications: Suitable for producing parts that require deep drawing processes, such as metal cups, metal containers, and metal cans.
4.6Bending:
The bendability of ASTM A513 materials makes them perform well in bending processes, suitable for manufacturing parts with complex geometries.
Applications: Used in bending various metal pipes and sheets, such as support components in building structures and machinery equipment.
5.0TABLE 1:Chemical Requirements for Standard Low-Carbon Steels
This table provides the chemical composition requirements for different low-carbon steel grades specified in ASTM A513. It includes common low-carbon steel types such as SAE 1008, SAE 1010, and SAE 1020.
The table details the range of carbon, manganese, phosphorus, and sulfur content for each grade. These composition standards ensure consistent quality and performance of the steel during manufacturing, meeting the needs of various applications.
Grade Designation | Carbon (%) | Manganese (%) | Phosphorus, max (%) | Sulfur, max (%) |
MTB 1010 | 0.02–0.15 | 0.30–0.60 | 0.035 | 0.035 |
MT 1015 | 0.10–0.20 | 0.30–0.60 | 0.035 | 0.035 |
MT X 1015 | 0.10–0.20 | 0.60–0.90 | 0.035 | 0.035 |
MT 1020 | 0.15–0.25 | 0.30–0.60 | 0.035 | 0.035 |
MT X 1020 | 0.15–0.25 | 0.70–1.00 | 0.035 | 0.035 |
Notes:
- Chemistry represents heat analysis. Product analysis, except for rimmed or capped steel, is to be in accordance with usual practice as shown in Table 3.
- Rimmed or capped steels used for these grades are characterized by a lack of uniformity in their chemical composition, making product analysis not appropriate unless misapplication is clearly indicated.
- “MT” indicates Mechanical Tubing.
6.0TABLE 2:Chemical Requirements for Other Carbon and Alloy Steels
This table outlines the chemical composition requirements for other types of carbon and alloy steels under ASTM A513. It covers a range of grades from low-carbon steels to various alloy steels, such as 1006, 1015, 4130, and 4140.
The table specifies the maximum and minimum content of elements like carbon, manganese, phosphorus, sulfur, silicon, nickel, chromium, and molybdenum. These specifications are crucial for the material’s mechanical properties, durability, and machinability.
Grade Designation | Carbon (%) | Manganese (%) | Phosphorus, max (%) | Sulfur, max (%) | Silicon (%) | Nickel (%) | Chromium (%) | Molybdenum (%) |
1006 | 0.08 max | 0.45 max | 0.030 | 0.035 | … | … | … | … |
1008 | 0.10 max | 0.50 max | 0.035 | 0.035 | … | … | … | … |
1009 | 0.15 max | 0.60 max | 0.035 | 0.035 | … | … | … | … |
1010 | 0.08–0.13 | 0.30–0.60 | 0.035 | 0.035 | … | … | … | … |
1012 | 0.10–0.15 | 0.30–0.60 | 0.035 | 0.035 | … | … | … | … |
1015 | 0.13–0.18 | 0.30–0.60 | 0.035 | 0.035 | … | … | … | … |
1016 | 0.13–0.18 | 0.60–0.90 | 0.035 | 0.035 | … | … | … | … |
1017 | 0.15–0.20 | 0.30–0.60 | 0.035 | 0.035 | … | … | … | … |
1018 | 0.15–0.20 | 0.60–0.90 | 0.035 | 0.035 | … | … | … | … |
1019 | 0.15–0.20 | 0.70–1.00 | 0.035 | 0.035 | … | … | … | … |
1020 | 0.18–0.23 | 0.30–0.60 | 0.035 | 0.035 | … | … | … | … |
1021 | 0.18–0.23 | 0.60–0.90 | 0.035 | 0.035 | … | … | … | … |
1022 | 0.18–0.23 | 0.70–1.00 | 0.035 | 0.035 | … | … | … | … |
1023 | 0.20–0.25 | 0.30–0.60 | 0.035 | 0.035 | … | … | … | … |
1024 | 0.18–0.25 | 1.30–1.65 | 0.035 | 0.035 | … | … | … | … |
1025 | 0.22–0.28 | 0.30–0.60 | 0.035 | 0.035 | … | … | … | … |
1026 | 0.22–0.28 | 0.60–0.90 | 0.035 | 0.035 | … | … | … | … |
1027 | 0.22–0.29 | 1.20–1.55 | 0.035 | 0.035 | … | … | … | … |
1030 | 0.28–0.34 | 0.60–0.90 | 0.035 | 0.035 | … | … | … | … |
1033 | 0.30–0.36 | 0.70–1.00 | 0.035 | 0.035 | … | … | … | … |
1035 | 0.32–0.38 | 0.60–0.90 | 0.035 | 0.035 | … | … | … | … |
1040 | 0.37–0.44 | 0.60–0.90 | 0.040 | 0.050 | … | … | … | … |
1050 | 0.48–0.55 | 0.60–0.90 | 0.040 | 0.050 | … | … | … | … |
1060 | 0.55–0.65 | 0.60–0.90 | 0.040 | 0.050 | … | … | … | … |
1340 | 0.38–0.43 | 1.60–1.90 | 0.035 | 0.040 | 0.15–0.35 | … | … | … |
1524 | 0.19–0.25 | 1.35–1.65 | 0.040 | 0.050 | … | … | … | … |
4118 | 0.18–0.23 | 0.70–0.90 | 0.035 | 0.040 | 0.15–0.35 | … | 0.40–0.60 | 0.08–0.15 |
4130 | 0.28–0.33 | 0.40–0.60 | 0.035 | 0.040 | 0.15–0.35 | … | 0.80–1.10 | 0.15–0.25 |
4140 | 0.38–0.43 | 0.75–1.00 | 0.035 | 0.040 | 0.15–0.35 | … | 0.80–1.10 | 0.15–0.25 |
5130 | 0.28–0.33 | 0.70–0.90 | 0.035 | 0.040 | 0.15–0.35 | … | 0.80–1.10 | … |
8620 | 0.18–0.23 | 0.70–0.90 | 0.035 | 0.040 | 0.15–0.35 | 0.40–0.70 | 0.40–0.60 | 0.15–0.25 |
8630 | 0.28–0.33 | 0.70–0.90 | 0.035 | 0.040 | 0.15–0.35 | 0.40–0.70 | 0.40–0.60 | 0.15–0.25 |
7.0TABLE 3:Tolerances for Product Analysis for Steels Shown in Tables 1 and 2
This table defines the tolerance ranges for elemental content in ASTM A513 steel products. It provides allowable variations for elements such as carbon, manganese, phosphorus, sulfur, silicon, nickel, chromium, and molybdenum.
Element | Limit, or Maximum of Specified Range, % | Variation, Over the Maximum Limit or Under the Minimum Limit |
Carbon | ||
To 0.15, incl | 0.02 | 0.03 |
Over 0.15 to 0.40, incl | 0.03 | 0.04 |
Over 0.40 to 0.55, incl | 0.03 | 0.05 |
Manganese | ||
To 0.60, incl | 0.03 | 0.03 |
Over 0.60 to 1.15, incl | 0.04 | 0.04 |
Over 1.15 to 1.65, incl | 0.05 | 0.05 |
Phosphorus | … | 0.01 |
Sulfur | … | 0.01 |
Silicon | ||
To 0.30, incl | 0.02 | 0.03 |
Over 0.30 to 0.60 | 0.05 | 0.05 |
Nickel | To 1.00, incl | 0.03 |
Chromium | To 0.90, incl | 0.03 |
Over 0.90 to 2.10 | 0.05 | 0.05 |
Molybdenum | ||
To 0.20, incl | 0.01 | 0.01 |
Over 0.20 to 0.40 | 0.02 | 0.02 |
- Individual determinations may vary from the specified heat limits or ranges to the extent shown in this table, except that any element in a heat may not vary both above and below a specified range.
- Where the ellipsis (…) appears in this table, there is no requirement.
References: