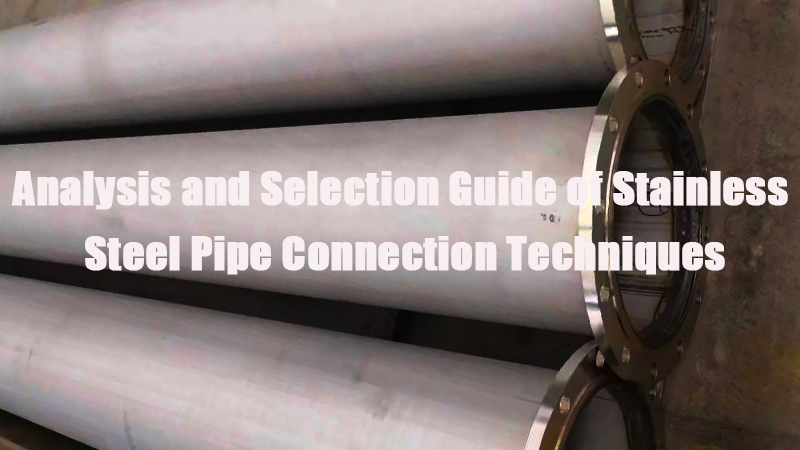
In modern pipeline engineering, stainless steel pipes are increasingly used due to their high strength, corrosion resistance, and long service life. These qualities make them the preferred choice in the construction, automotive, and firefighting industries.
However, the performance of pipelines depends not only on the material but also on the type of connection used. The connection method plays a critical role in the overall efficiency and reliability of the system.
This article will explore various connection techniques for stainless steel pipes, including flanges, to help you choose the best solution for your needs.
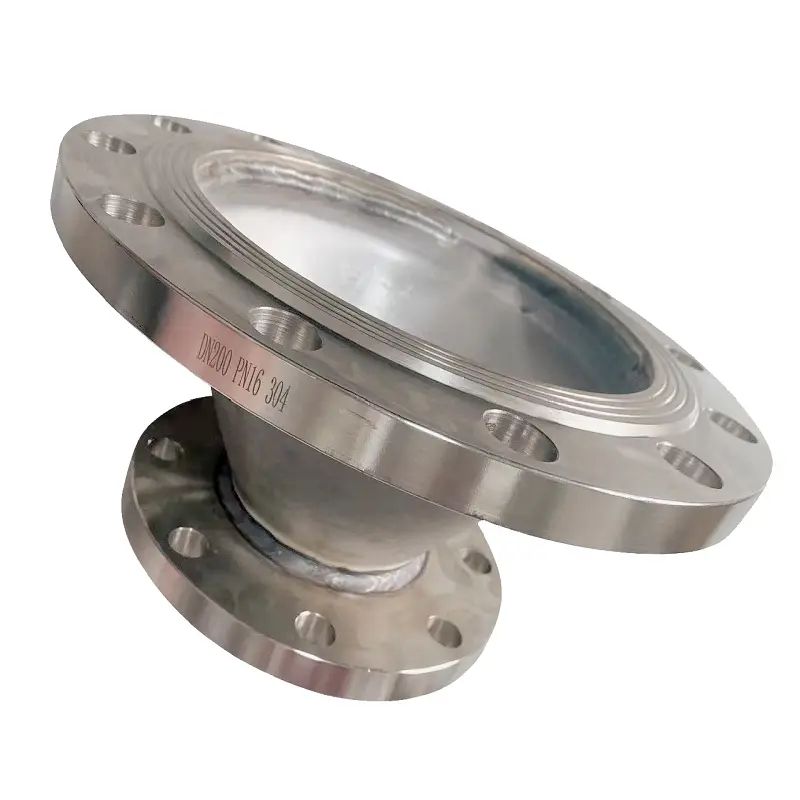
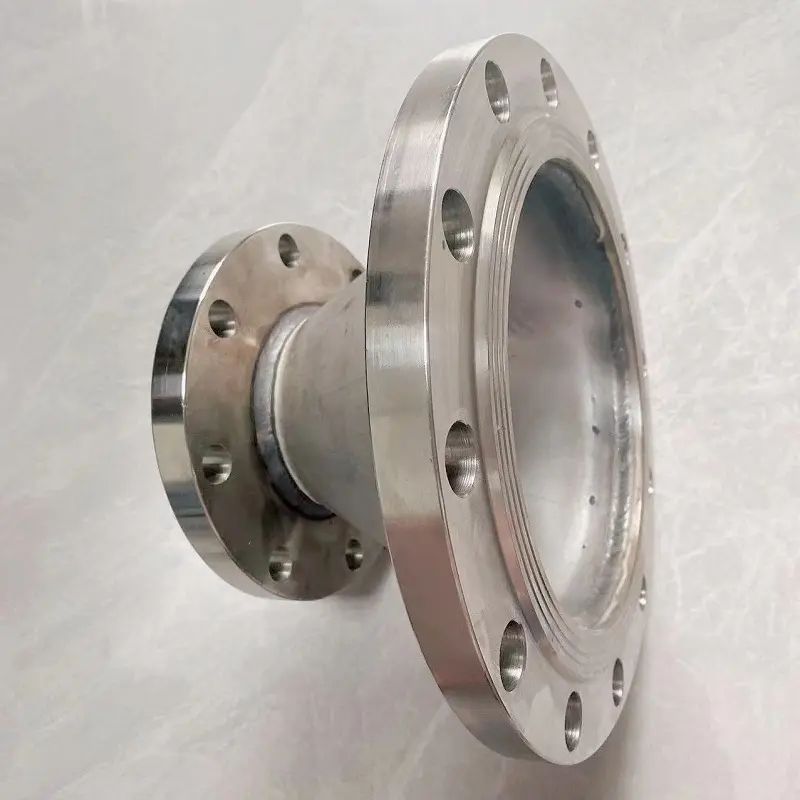
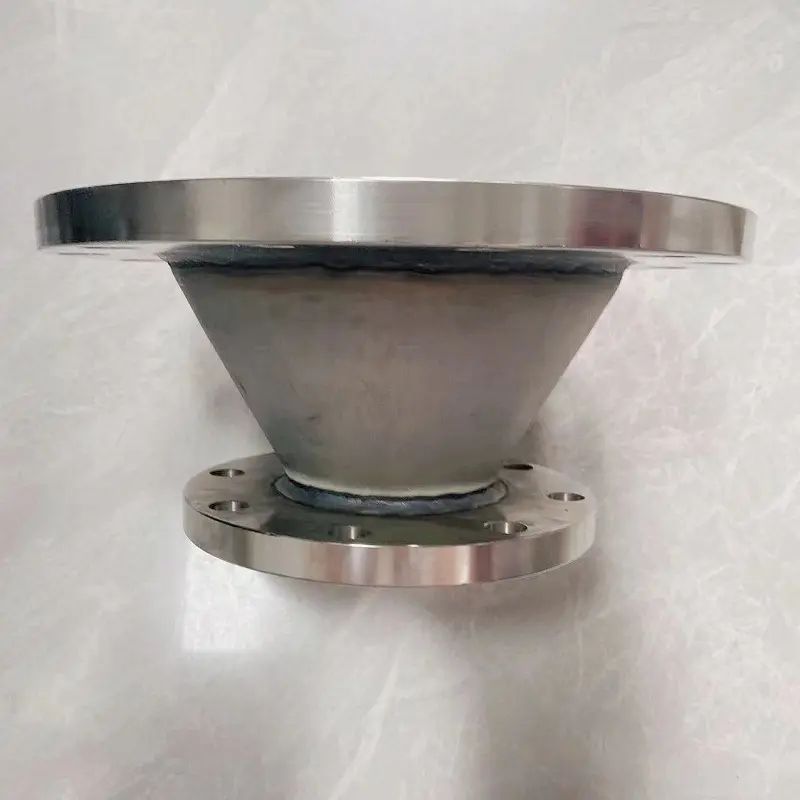
1.0 Why Are Stainless Steel Pipe and Flange Connections So Important?
In pipeline systems, the type of connection directly affects the following aspects:
- Sealing Performance: Determines whether leaks occur.
- Strength and Stability: The ability to withstand pressure and temperature changes.
- Construction Efficiency: Impacts installation costs and project duration.
- Maintainability: Ease of disassembly and repair.
Each connection method has its advantages and disadvantages, and selecting the most suitable one is critical in practical applications.
2.0 Comparison of 6 Main Connection Methods: Pros and Cons Breakdown
2.1 Crimping Connection
- Principle: A hydraulic tool is used to crimp the stainless steel fitting onto the pipe, with an O-ring seal to prevent leakage.
- Advantages:
- Fast installation, suitable for medium and small pipe installations.
- Good sealing performance for normal pressure conditions.
- Disadvantages:
- Thin pipe walls lead to lower connection strength (only about 1/3 of the pipe’s strength).
- Non-removable, making maintenance difficult.
- Improper handling of pipe ends may damage the O-ring and cause leakage.
2.2 Compression Connection
- Principle: A hydraulic tool compresses the stainless steel fitting, using a wide-band rubber seal to achieve sealing.
- Advantages:
- Higher connection strength than crimping.
- Suitable for environments with high sealing requirements.
- Disadvantages:
- The fitting may rotate at the ring-shaped compression point, affecting sealing performance.
2.3 Flanged Connection
- Principle: Two fittings with flanges are bolted together, with a flat sealing gasket to achieve sealing.
- Advantages:
- High connection strength, suitable for high-pressure and large-diameter pipelines.
- Easy to disassemble and maintain, stable and reliable over long-term use.
- Disadvantages:
- Higher cost, especially for flange plates and bolts.
- Installation requires high-quality sealing gaskets.
2.4 Grooved Connection
- Principle: A clamp and tapered seal ring compress stainless steel fittings with protruding rings to create the connection.
- Advantages:
- Simple installation, removable, and suitable for temporary structures.
- Ideal for fire protection and large-diameter water supply pipelines.
- Disadvantages:
- Requires precise grooving of pipe ends.
- Not suitable for use in negative pressure environments, higher cost.
2.5 Welded Connection
- Principle: Two pipe fittings are directly fused together through a welding process.
- Advantages:
- High connection strength, suitable for high-pressure and high-temperature environments.
- Seamless joints with excellent sealing properties.
- Disadvantages:
- Welds are prone to rust, reducing pipeline lifespan.
- Requires high welding skills and difficult construction techniques.
2.6 Tapered Thread Connection
- Principle: Two fittings are tightened by threads, achieving sealing through thread pressure.
- Advantages:
- Easy to disassemble and install, suitable for temporary pipelines or maintenance scenarios.
- Lower cost, widely applicable.
- Disadvantages:
- Weaker sealing requires auxiliary materials (such as PTFE tape) to ensure long-term sealing.
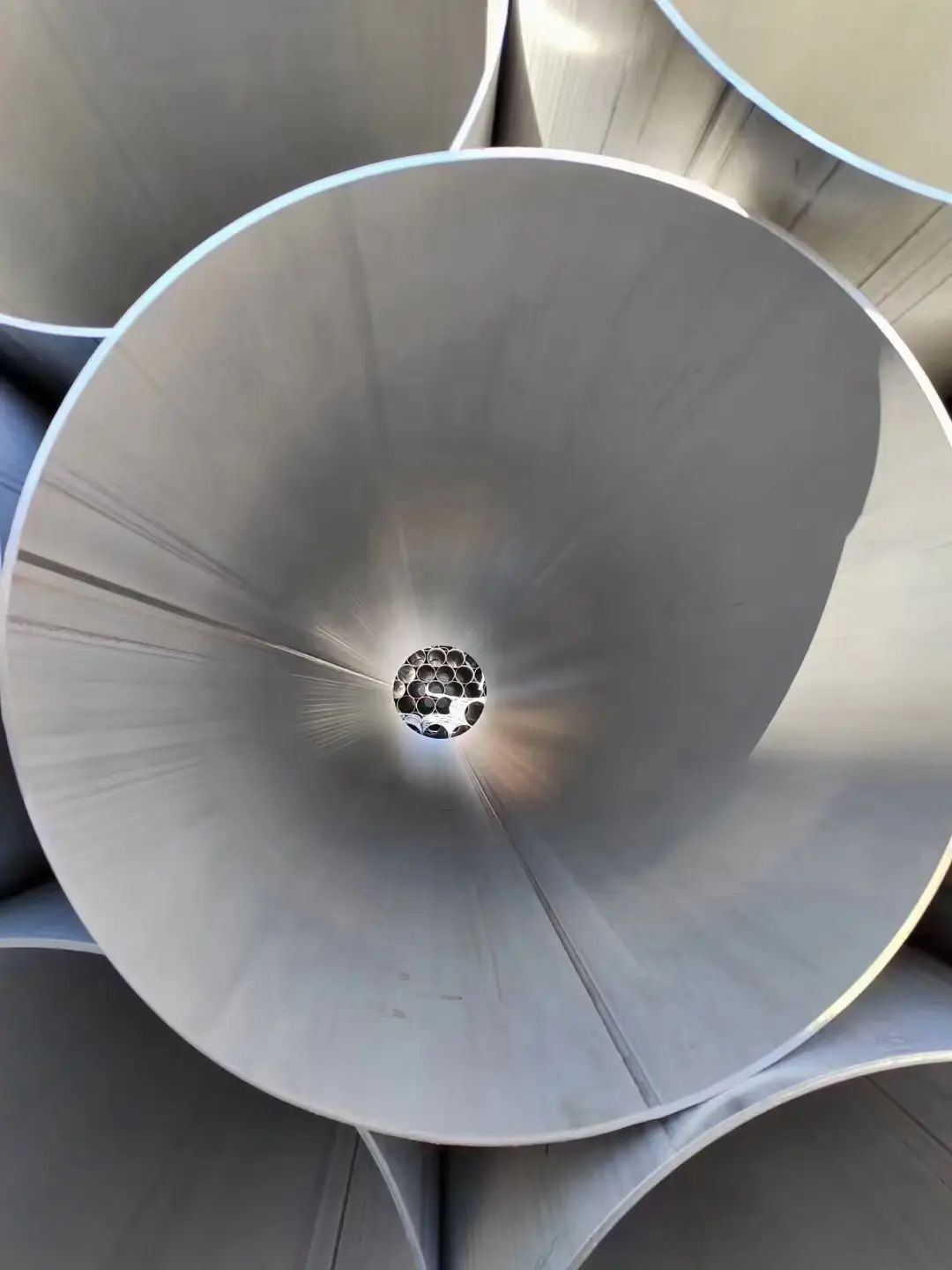
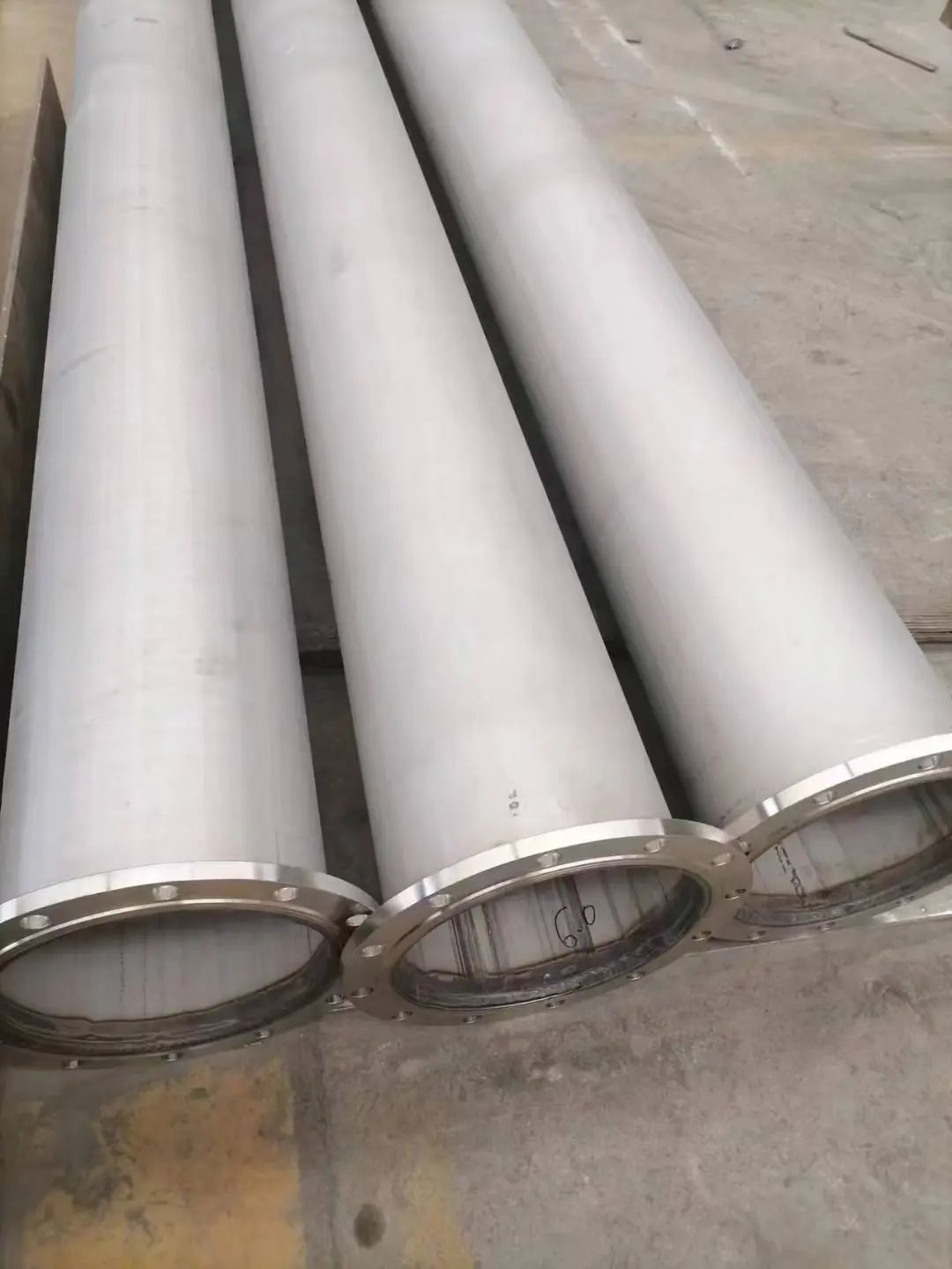
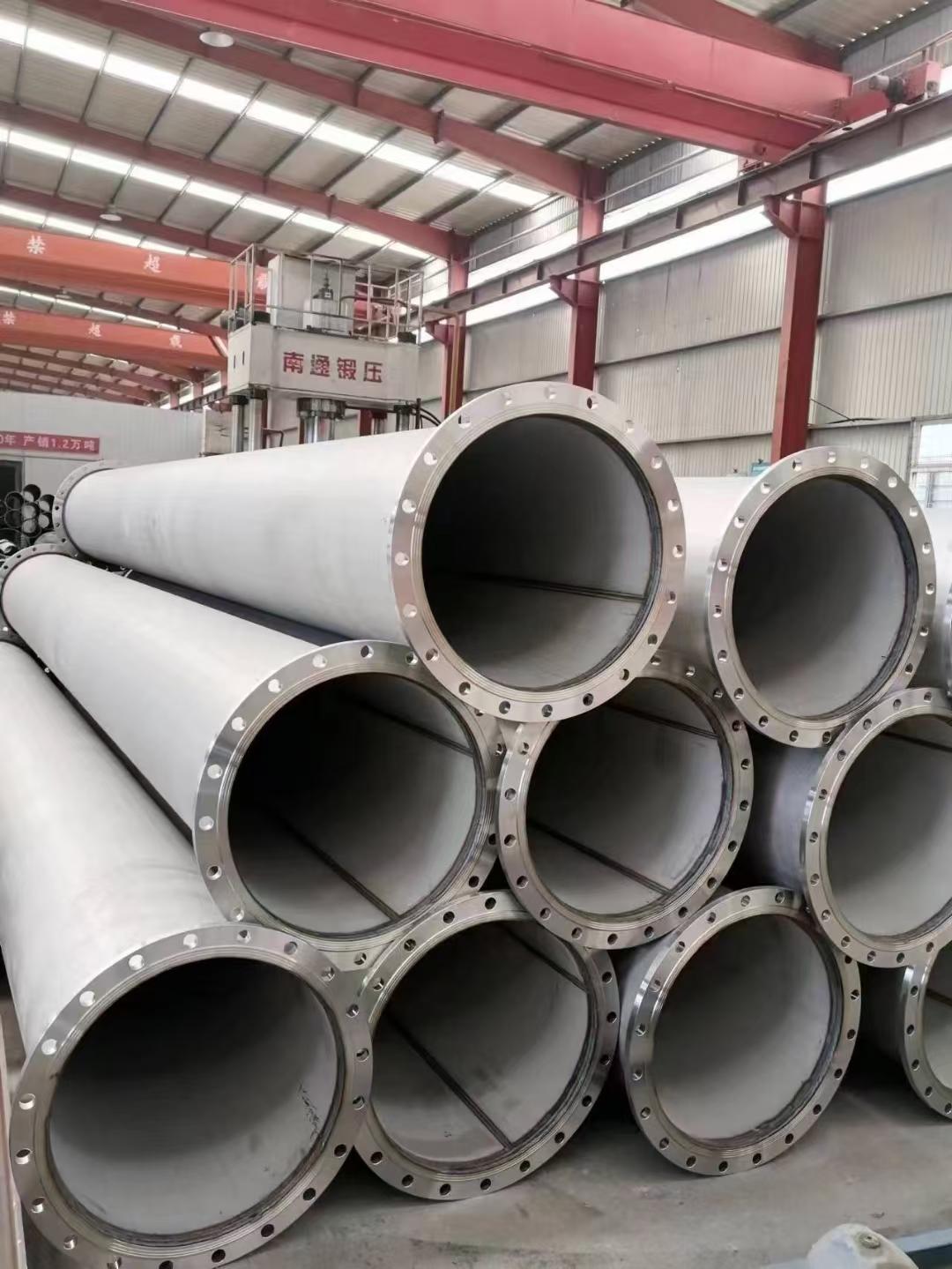
3.0 Single Crimping vs. Double Crimping: Evolution of Mainstream Connection Methods
Single Crimping Connection:
- Uses a hydraulic tool to quickly crimp the fitting onto the pipe, with a built-in rubber seal, suitable for low to medium-pressure water pipelines.
- Features: Fast installation, good sealing performance, but limited connection strength. Not suitable for high-pressure environments.
Double Crimping Connection:
- Based on the single crimping method, the pipe fitting’s diameter is extended, and additional pressure is applied at both ends to improve sealing and safety.
- Features: Enhanced durability, gradually becoming the mainstream connection method for metal pipes, especially suitable for thin-walled stainless steel water pipes.
4.0 Application Analysis of Special Connection Methods
Socket Weld Connection:
- The pipe fittings are joined through an expansion and insertion method, followed by welding.
- Advantages: More precise welding, suitable for complex projects or high sealing requirements.
Grooved Connection:
- Common in fire protection water supply and temporary construction projects, suitable for pipelines with a diameter above DN100.
- Features: Simple installation, removable, suitable for both long-term and short-term projects.
This comparison highlights the importance of selecting the right connection method based on the specific requirements of your pipeline system, ensuring both performance and reliability.