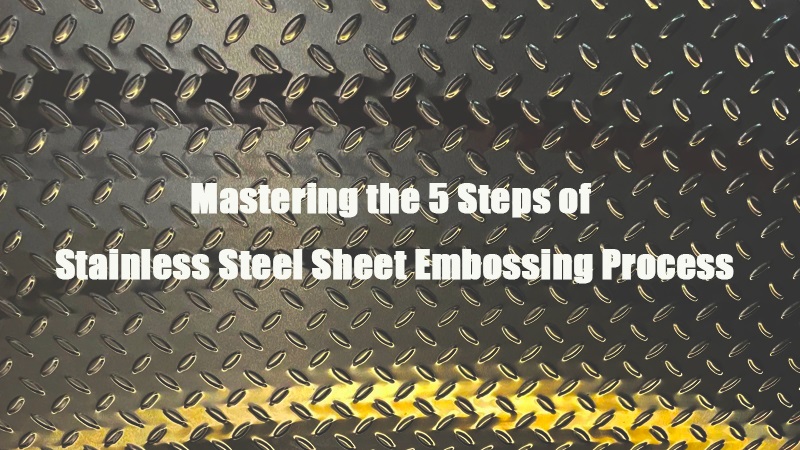
5 Steps to Master the Sheet Metal Embossing Process
0.1 Introduction to Stainless Steel Sheet Embossing Process
Embossed stainless steel sheets are created by rolling patterns from mold rollers onto the sheets using an embossing machine.
Sheet metal embossing is a stamping process for producing raised or sunken designs or relief in sheet metal. passing sheet or a strip of metal between rolls of the desired pattern. It is often combined with foil stamping to create a shiny, 3D effect.
0.2 Main Features of Embossed Stainless Steel Sheets
Embossed stainless steel sheets are aesthetically pleasing and widely used in architectural decoration, such as embossed metal wall decor. The raised and recessed textures on the surface increase friction, making them ideal for slip-resistant areas like stairs and floors, as well as subway car floors.
Stainless steel embossed sheets are highly durable, offering rust resistance, anti-pollution properties, and excellent corrosion resistance, all while being easy to clean.
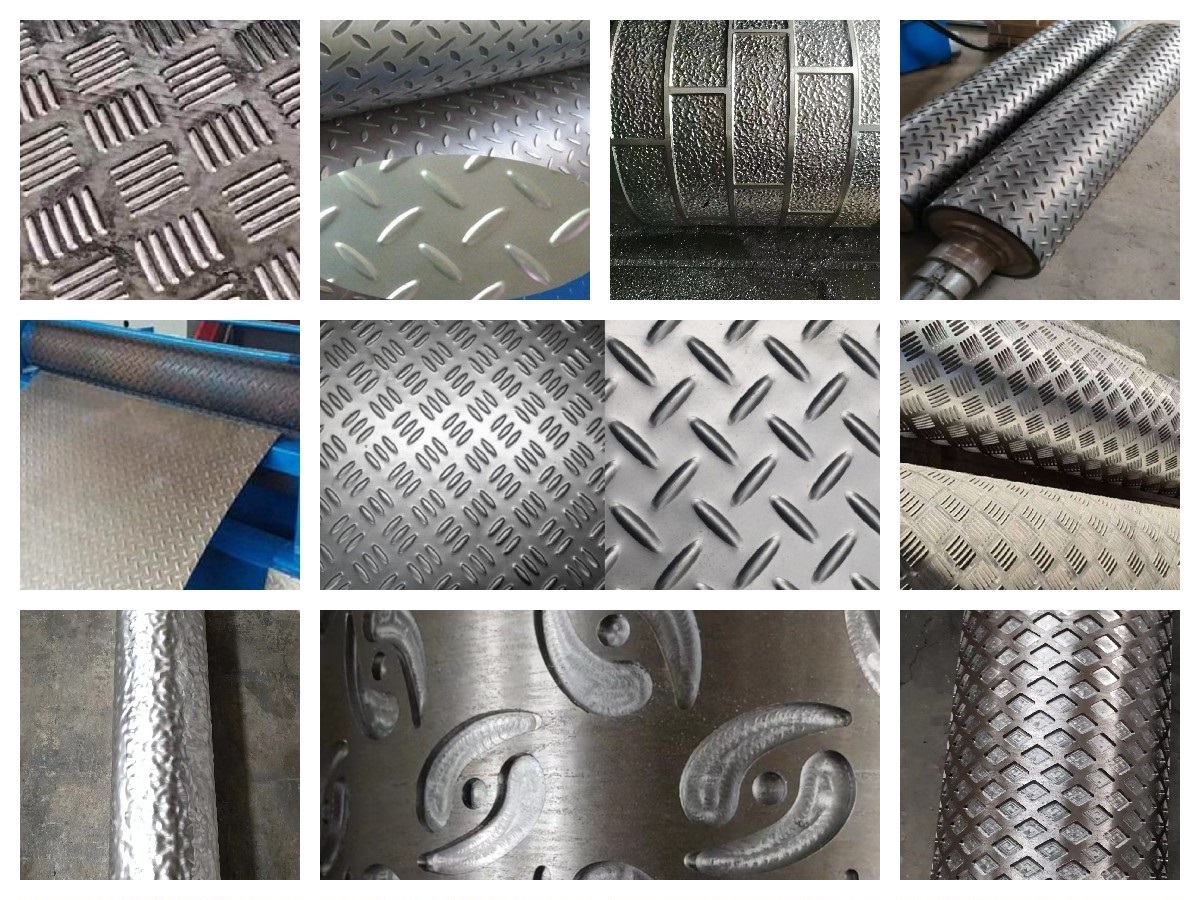
0.3 Common Patterns for Embossed Stainless Steel Sheets
- Checkerboard
- Ripple pattern
- Dot pattern
- Leather texture
- Mesh pattern
- Cube
- Chrysanthemum
- Antique square
- Wood grain
- Diamond
- Small square
- Linen
- Small linen
- Sand
- Rice grain
- Strip
- Grid
- Leather pattern
0.4 Major Applications of Embossed Stainless Steel Sheets
Architectural Decoration: Used for embossed metal wall art, ceilings, columns, and other wall decoration materials.
Furniture and Kitchenware: Materials for cabinet doors, countertops, and embossed metal plates.
Elevator Decoration: Embossed stainless steel for interior and door decor in elevators.
Industrial Areas: Suitable for slip-resistant walkways and work platforms.
Transportation: Used in subway, train floors, and handrails.
Key Steps and Considerations in the Stainless Steel Embossing Process
1.0 Selection of Stainless Steel Material
1.1 Common Materials for Embossed Stainless Steel Sheets:
- Aluminium (all alloys)
- Aluminium (T1/T2)
- Brass
- Card stock
- Cold rolled steel
- Copper
- Galvanized steel
- High strength, low alloy, steel
- Hot rolled steel
- Steel (all alloys)
- Zinc
Stainless Steel Sheets:
- 304 Stainless Steel: The standard material for embossed sheets with good corrosion resistance.
- 316 Stainless Steel: Offers better corrosion resistance than 304, often used in high-end or outdoor environments.
- 430 Stainless Steel: More cost-effective, suitable for indoor metal embossed tileswhere corrosion resistance is less critical.
1.2 Material Thickness and Pattern Depth:
- Thinner sheets (0.5-1.0mm): Suitable for decorative uses, with relatively shallow patterns.
- Thicker sheets (1.5mm and above): Enable deeper embossing, creating more pronounced patterns, ideal for slip-resistant applications.
2.0 Embossing Mold Roller
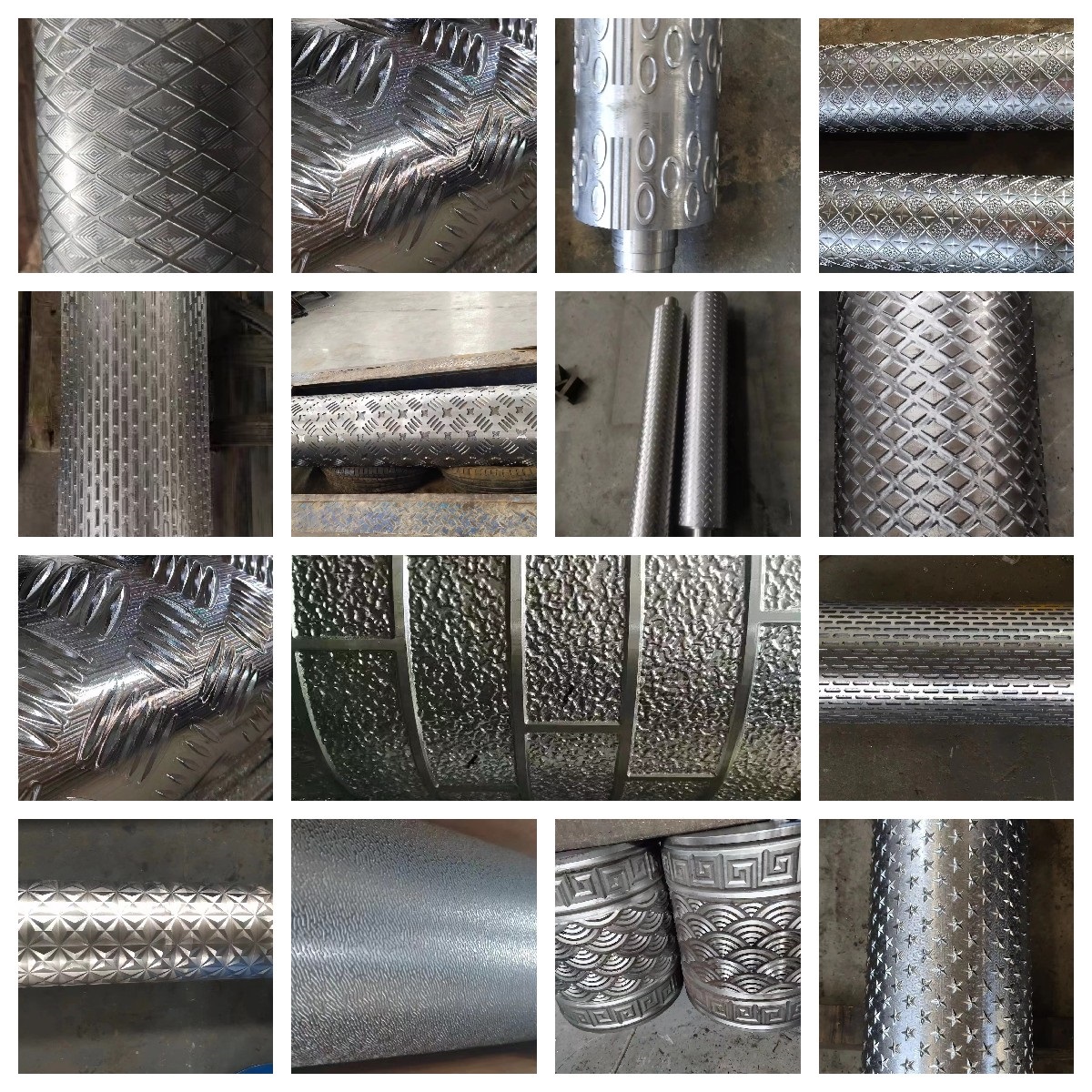
2.1 Designing the Embossing Mold:
Pattern Design: The design must consider the ductility of the stainless steel and the depth of the embossing to ensure clear pattern reproduction.
Embossing Depth: Adjust the depth according to the sheet thickness and intended use. Thicker sheets can support deeper embossing, while thinner sheets are better suited for shallow patterns.
Mold Size: The mold roller’s size must precisely match the stainless steel sheet dimensions to avoid misalignment or deformation during embossing.
Pattern Continuity: Ensure continuous and symmetrical patterning to avoid seams or misalignment.
2.2 Materials for Mold Rollers:
- High-Strength Alloy Steel: Mold rollers, typically made from Cr12MoV or D2 steel, can withstand the high pressure and friction involved in embossing stainless steel.
2.3 Ensuring Mold Precision:
- High-Precision Machining: Since stainless steel is hard, the mold’s precision must be in the micron range, achieved through CNC machining.
2.4 Mold Maintenance:
Cleaning: Regular cleaning of molds is necessary to remove grease and metal debris, ensuring the quality of the embossing.
Wear Detection: Regularly inspect molds for wear or cracks, particularly those used frequently, to maintain pattern clarity.
Lubrication: Proper lubrication extends the mold’s lifespan.
Storage: Mold rollers should be stored in dry conditions to prevent rust or surface damage.
3.0 Stainless Steel Embossing Machine Settings
Types of Common Embossing Machines:
Hydraulic Embossing Machines: Suitable for large-scale production or embossing thick sheets, especially for industrial slip-resistant flooring.
Mechanical Embossing Machines: Ideal for small to medium-scale production, compact and cost-effective.
Rolling Machines: Designed for large-volume production of thin embossed stainless steel sheets, such as those used for elevator decoror home appliances.
3.1 Adjusting Embossing Machine Parameters:
Pressure Adjustment: Set pressure based on the thickness, hardness, and desired pattern depth of the stainless steel.
Speed Adjustment: Increase speed for thinner materials and reduce it for thicker ones.
Temperature Adjustment: In some cases, heating the stainless steel can improve its plasticity, especially for thicker sheets or deep embossing processes.
3.2 Ensuring Stability During Embossing:
Machine Calibration: Regularly calibrate the machine to ensure correct pressure, speed, and temperature settings.
Monitoring Machine Status: Continuously monitor machine operation to detect any anomalies in temperature, pressure, or speed.
Vibration Control: Ensure the mold rollers are installed on a stable platform to prevent vibrations from affecting the embossing quality.
4.0 Handling Embossed Stainless Steel Sheets
4.1 Flattening Stainless Steel Sheets:
Surface Flatness Check: Use a leveling machine to ensure the sheets are smooth without dents or raised areas.
Material Pre-Treatment: For harder stainless steel, light annealing before embossing can reduce internal stress and prevent irregular deformation or cracking during embossing.
Securing Workpieces: Ensure the stainless steel sheet is securely fixed during embossing to prevent shifting, which could distort the pattern or cause wrinkling along the edges.
4.2 Ensuring Pattern Clarity and Uniformity:
Precise, Defect-Free Mold: The mold pattern must be flawless.
Even Pressure: Ensure consistent pressure across the sheet.
Material Thickness Control: Maintain uniform material thickness.
4.3 Real-Time Monitoring of Key Parameters (Pressure, Temperature, etc.):
Pressure Monitoring: Continuously monitor the pressure to ensure uniform embossing.
Temperature Control: Adjust temperature as needed to improve material plasticity.
Speed Monitoring: Maintain consistent speed to avoid uneven embossing.
5.0 Post-Embossing Treatment
5.1 Surface Treatment After Embossing:
Surface Cleaning: Remove residual oil, metal debris, and particles to maintain the product’s appearance.
Polishing: Depending on the product, the surface may be polished. Common polishing methods include mechanical, chemical, or electrochemical polishing.
Brushing: Brushing the surface gives the stainless steel a more textured visual effect.
5.2 Protective Film and Anti-Rust Treatment:
- Surface Protective Film: Apply a protective film using an automatic laminating machine to prevent scratches or damage during transport and further processing.
- Anti-Rust Treatment:
- Passivation Treatment: Use chemical passivation to remove surface oxides and impurities.
- Anti-Fingerprint Coating: Apply a transparent coating to prevent fingerprints and smudges.
5.3 Packaging and Storage:
Protective Packaging: Ensure the sheets are packaged securely to prevent damage.
Moisture-Proof Storage: Store the sheets in a moisture-controlled environment to avoid rust.
Labeling and Documentation: Properly label and document the embossed stainless steel sheets for easy identification.
https://link.springer.com/article/10.1007/s00542-010-1158-x
https://en.wikipedia.org/wiki/Embossing_(manufacturing)